Are you hoping to eventually be considered for a management position after you are done with your forklift training? Maybe you are wondering if you have what it takes to run a warehouse. Alternately, perhaps you are trying to choose between two positions being offered and you need to determine who would be the better boss to work under. Whatever the case is, this list of traits should help, whether you are evaluating yourself or someone else.
Getting your forklift license is the easy part, and starting your new career is exciting. It is the process in-between that makes most people cringe. If your current employer is having you get certified, so you can be promoted to a forklift operator then you have it made and get to skip all the less fun steps. Otherwise, like most other careers, you are going to need a resume. If you have never written a resume before then just the thought of the process is probably intimidating. Even if you have created one for a different line of work, you need a completely new one to apply for forklift positions.
Houston, home to the wonders of the Astrodome and NASA’s Mission Control, is more than just revolutionary sports stadiums and space traffic control. The economy is always growing in Texas and booming right along with it is Houston forklift training.
The city has the fourth most people in the United States, a fact that is not well-known. With all that population, you know there are going to be great hidden pockets to live, work, eat and play. With the city limits spread out over nearly 600 square miles, the density is not intense, making it a perfect place if you want the advantages of a big city without feeling like you are living on top of everyone else.
According to the United States Bureau of Labor Statistics (BLS), forklift operator careers should expand by more than 12 percent between 2015 and 2020. The conservative BLS estimates does not factor in the impact of the recent dramatic decline in energy prices. Lower energy prices increase consumer demand, as well as provide transportation companies with significant savings. The BLS outlook for forklift operators includes an average annual salary of $30,220 for the 496,570 forklift specialists employed as of 2014.
Since forklifts are used today in a wide variety of indoor and outdoor environments, you can expect there to be a significant number of differences in the job description from one employer to the next. Despite the varied environments, there are a few basic responsibilities that tend to remain constant regardless of employer. If you are thinking about enrolling to get your forklift certification this list will give you a general idea of what to expect. Just keep in mind that depending on where you work, you could have significantly more or less responsibilities.
Wondering how to get your forklift certification? With hundreds of jobs requiring this qualification, getting trained is definitely a smart move. This blog will guide you through the steps needed to earn your license and explain just how long it can take.
Ready to start a new chapter in your career? Keep reading!
Key Takeaways
- In – person forklift training typically lasts 2 to 4 hours, while the duration of online training can vary.
- Forklift certifications usually last for 3 years and require renewal.
- Being certified increases job opportunities and demonstrates a commitment to workplace safety.
Steps to Get Forklift Certified
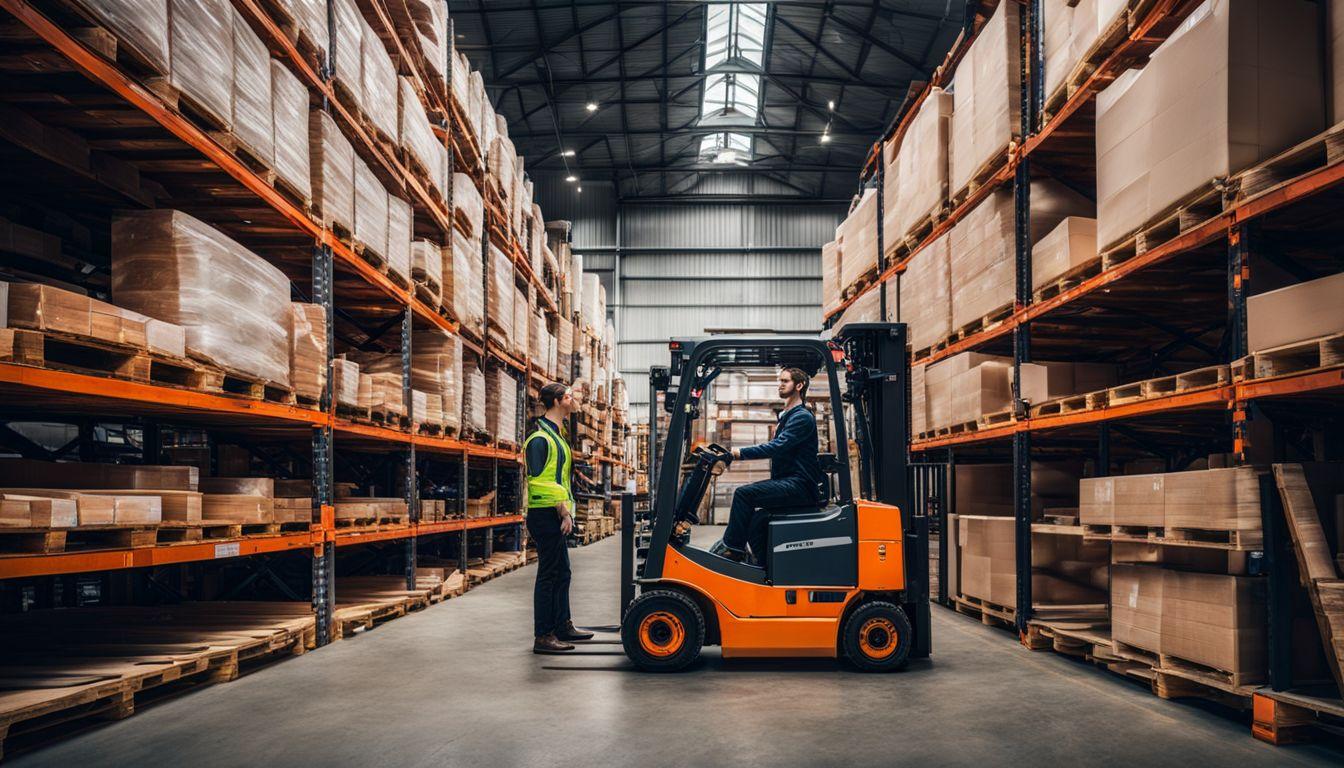
To get forklift certified, you need to choose the right certification course, enroll in the program, attend classes and study, complete the training, and receive your certification.
Choose the right certification course
Choosing the right forklift certification course is crucial. A counterbalance forklift, one of the most common types, may only require a day or two of training. On the other hand, rough terrain forklift training could take 2 to 4 hours.
Courses can be taken in-person or online depending on your preference and convenience. Remember that costs will vary with each type of course and location; Online courses can cost as low as $50 ranging upwards to $400, while in-person programs may have different pricing models.
No matter what you choose though, make sure it covers both theoretical and practical aspects essential to pass the training program successfully.
Enroll in the program
Securing a spot in the desired forklift certification program is the next crucial move. Popularity and convenience have resulted in a variety of options to choose from, both online and offline.
Online courses offer flexibility with schedules, while classroom training offers hands-on learning experiences.
The costs associated with enrolling can jump anywhere between $50 – $200 depending on your chosen course’s complexity or type. The specific forklift model can also influence this cost; counterbalance forklift training taking only one to two days to complete whereas other types like rough terrain may require up to eight hours of commitment.
Therefore, it’s essential to select a program that aligns best with your needs and budget before enrollment.
Attend classes and study
Signing up for the certification program is just the first step. The core of getting forklift certified lies in attending classes and studying diligently. Most training courses include theoretical lessons that cover safety protocols, OSHA regulations, equipment maintenance, and operational techniques.
Alongside theory, practical sessions help students grasp real-world handling of forklifts under expert guidance. These may take place on actual work sites or simulated environments to ensure hands-on experience.
Self-study helps reinforce these concepts outside class hours as you gear up for the final assessment that determines your eligibility to receive the certification.
Complete the training
To become forklift certified, it is crucial to complete the training program. The duration of the training can vary depending on the type of forklift and the specific course, but in-person programs typically take about two to four hours to finish successfully.
Participants will be required to pass both theoretical and practical components of the training before receiving their certification. This includes video instructional segments and written materials to ensure a comprehensive understanding of forklift operation and safety protocols.
So, once you have enrolled in the program, attended classes, and studied diligently, completing the training is the final step towards becoming a certified forklift operator.
Receive your certification
After successfully completing the forklift certification program, you will receive your certification. This is proof that you have met all the requirements and are qualified to operate a forklift safely and efficiently.
Certifications typically last for three years, after which they need to be renewed. Once you have your certification in hand, you’ll have the necessary skills and knowledge to excel in a wide range of industries that require forklift operation.
Don’t miss out on the opportunity to enhance your career prospects by becoming certified!
Duration of Forklift Training
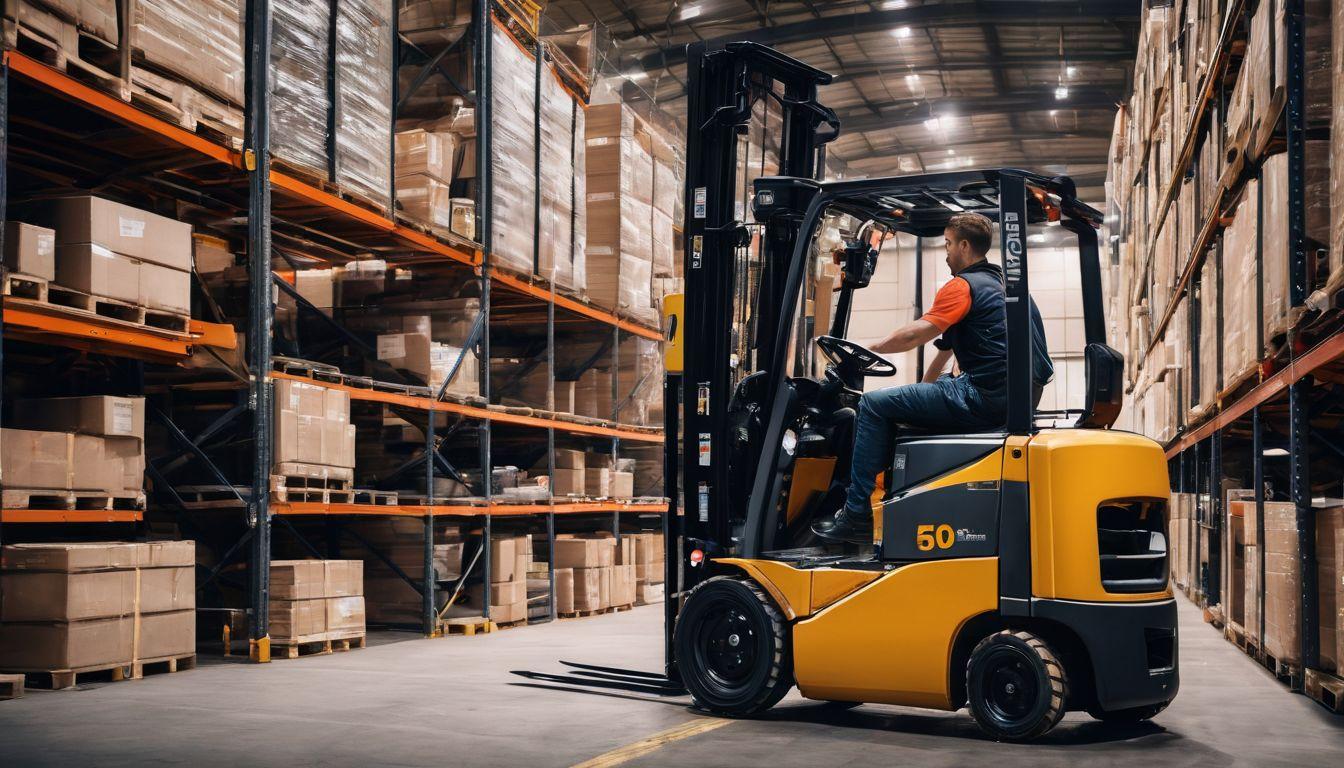
In-person training typically lasts 2-4 hours, while the duration of online training is around two hours.
In-person training typically takes 2-4 hours
In-person forklift training typically lasts for about 2 to 4 hours. During this time, participants will go through a comprehensive program that covers all the necessary skills and knowledge needed to operate a forklift safely and efficiently.
The training sessions include both theoretical instruction and hands-on practice, giving learners the opportunity to understand important concepts and put them into action. By the end of the training, participants will have gained the confidence and competence required to obtain their forklift certification.
Online training duration may vary
Online forklift training offers flexibility in terms of duration. The length of the online training program can depend on various factors, including the specific course and provider chosen.
Some online programs may offer self-paced learning, allowing individuals to complete the training at their own speed. This means that the duration of online forklift training can vary from a few hours to several days, depending on how quickly a person completes the required coursework and assessments.
It’s important to check with the specific online program or provider for more information on the estimated duration of their forklift certification course.
Certification Validity
Certifications typically last for three years and require renewal.
Certifications usually last for 3 years
Forklift certifications typically have a validity period of three years. This means that once you successfully complete the certification training and obtain your license, it will remain valid for three years before needing renewal.
It’s important to keep track of your certification expiration date and make sure to renew it promptly to ensure continued compliance with safety regulations. This regular renewal requirement helps ensure that forklift operators stay up-to-date with the latest safety standards and practices in order to maintain a safe working environment.
Renewal requirements
To maintain your forklift certification, you will need to renew it every three years. Renewal requirements typically involve completing a refresher course or passing a knowledge test to demonstrate that you are still competent in operating a forklift safely.
It’s important to stay up-to-date with any changes in regulations or best practices during this renewal process. Keep in mind that the cost and duration of the renewal may vary depending on the training provider and location.
So, make sure to check with your certification program for specific details when it’s time to renew your forklift certification.
Importance and Benefits of Forklift Certification
Having a forklift certification is crucial for anyone operating a forklift. It not only ensures the safety of the operator but also promotes workplace safety. Obtaining proper certification demonstrates that you have received the necessary training and have the skills to operate a forklift safely and efficiently.
One of the key benefits of being certified is that it improves your employability. Many employers require their forklift operators to be certified, as it shows their commitment to maintaining a safe working environment.
With certification, you are more likely to stand out among other job applicants and increase your chances of getting hired.
Another important benefit is that certification helps reduce accidents in the workplace. Forklifts can be dangerous if not operated correctly, leading to injuries or even fatalities.
By completing proper training and obtaining certification, you learn how to handle various situations effectively, including load handling, avoiding hazards, and understanding equipment limitations.
Furthermore, being certified allows you to confidently handle different types of forklifts. Different industries may require specific types of forklifts based on their needs. By having diverse certifications under your belt, such as counterbalance or rough terrain forklifts, you become more versatile as an operator and broaden your employment opportunities.
Overall, obtaining a forklift certification brings numerous advantages both personally and professionally. It enhances workplace safety measures while providing greater job prospects within various industries where operating a forklift is necessary.
Conclusion
Obtaining forklift certification can typically be completed within a day or two of training. In-person programs usually last about two to four hours, while online courses may vary in duration.
Remember, investing the time and effort into becoming certified is essential for both your safety and career advancement in operating forklifts.
FAQs
1. How can I get forklift certified?
You can obtain OSHA forklift certification through scheduled training sessions near your location or online classes.
2. What is involved in the process of getting forklift certified?
Forklift certification typically involves classroom lessons, written tests, and hands-on operating exercises to ensure you meet OSHA standards.
3. How long does it usually take to complete a forklift certification course?
The timeframe of becoming a certified operator varies from one day to a week, depending on the program design and trainee capacity.
4. Are there any prerequisites required before starting my forklift training?
While requirements might vary per program, most often just age restrictions apply; therefore it’s best to check with your chosen provider.
If you’re feeling a bit swamped by the myriad types of forklifts out there, unsure which one would perfectly serve your requirements, don’t worry! You’re not alone. This is a familiar scene that most of us encounter initially when we find ourselves navigating through this vast sea of forklift options.
But guess what? After investing countless hours pouring over resources at the Forklift Academy and undergoing some pretty rigorous forklift training myself, I’ve managed to amass quite an insightful knowledge bank in this area.
In this article, we will delve into the world of top 7 types of forklifts, exploring their uses in detail and guiding you on how to make an informed choice that best suits your needs.
Common Types of Forklifts
There are several common types of forklifts including electric forklifts, IC forklifts, reach trucks, order pickers, and pallet jacks.
Electric Forklifts
Electric forklifts are perfect for indoor use. They produce zero emissions, keep noise levels down and reduce operational costs because they work on rechargeable batteries. Unlike their internal combustion counterparts, there’s no need to constantly refill them with fuel.
Plus, the absence of a motor makes electric forklifts easier to maintain and operate. The ability to maneuver in tight spaces also comes as an added advantage, making these machines highly suitable for warehouses or areas where space is limited.
IC Forklifts
IC forklifts, also known as internal combustion forklifts, are primarily operated by engines using fuels like diesel, gasoline or liquid propane gas. They offer the advantage of unlimited runtime because refueling them is quick and easy.
This type of forklift offers solid power output which makes it an excellent choice when dealing with heavy loads.
The IC Forklift’s robust performance excels even in cold weather conditions where electric counterparts might struggle. Plus, their high lifting capacities put them right at home in demanding environments such as construction sites or lumber yards.
Unlike an electric forklift that requires hours to recharge, IC Forklifts only need minutes to fill up on fuel and get back into action.
Reach Trucks
Reach trucks are a staple in many warehouses due to their exceptional maneuverability. They’re designed with two outer legs that distribute the load weight, and a single set of wheels located at the back.
This allows them to move smoothly even in narrow aisles and tight spaces while lifting heavy loads high up onto warehouse shelving. The ‘reach’ feature means they can extend their forks beyond the compartment area, effectively reaching into racking for placement or retrieval of pallets.
These characteristics make reach trucks highly efficient and flexible for use in various indoor settings, earning your workplace a gold star from Forklift Academy.
Order Pickers
Order pickers are a type of forklift commonly used in warehouses and distribution centers. They are designed specifically for picking orders from shelves at various heights. Order pickers have a platform that elevates the operator to reach items on high racks, allowing them to efficiently retrieve products and materials. One of the requirements to use the order picker is the mandatory use of a fall protection device or harness.
The elevated platform provides better visibility, making it easier for operators to identify and select the correct items. With their maneuverability and ability to navigate narrow aisles, order pickers are essential for efficient order fulfillment in busy warehouse environments.
Pallet Jacks
Pallet jacks are a popular type of forklift used primarily in warehouse settings. They are designed to lift and move pallets, making them an essential tool for material handling. Pallet jacks typically have forks that slide underneath the pallet, allowing operators to easily maneuver heavy loads.
With their compact size and maneuverability, they are ideal for navigating narrow aisles and tight spaces. Pallet jacks come in both manual and electric models, offering options for different operational needs.
These versatile machines are commonly found in industries such as logistics, distribution centers, and manufacturing facilities where efficient pallet movement is crucial.
Understanding Different Forklift Types
There are several different types of forklifts that serve various purposes, such as industrial reach forklift trucks, industrial counterbalance forklifts, rough terrain forklifts, industrial side loader forklifts, and telescopic handler forklifts.
Industrial Reach Forklift Trucks
Industrial reach forklift trucks are a type of forklift that are specifically designed to reach high shelves and racks. With their extendable forks, these trucks can effortlessly lift and transport heavy loads to great heights, making them ideal for use in warehouses and distribution centers.
The ability to navigate narrow aisles also makes industrial reach forklift trucks highly versatile and efficient in maximizing storage space. By utilizing advanced hydraulic systems, operators can easily maneuver the truck’s mast and position the load precisely where it needs to go without any hassle.
Overall, industrial reach forklift trucks are essential equipment in industries that require frequent handling of goods at elevated locations.
Industrial Counterbalance Forklifts
Industrial counterbalance forklifts are one of the most common types of forklifts used in warehouses and industrial settings. These forklifts are designed with a weight at the back of the truck to balance out heavy loads at the front.
With their sturdy construction, they can easily lift and transport bulky items without tipping over. Industrial counterbalance forklifts are versatile and can be used both indoors and outdoors, making them suitable for a wide range of applications.
These forklifts come in various sizes and lifting capacities, allowing them to handle different types of materials. They have a simple design with two forks at the front that slide underneath pallets or other objects for lifting.
Rough Terrain Forklifts
Rough terrain forklifts are designed to efficiently operate in challenging outdoor environments. These powerful machines feature large, rugged tires that provide excellent traction on uneven surfaces such as construction sites or gravel yards.
With their sturdy build and high ground clearance, rough terrain forklifts can navigate through obstacles and handle heavy loads with ease. These versatile forklifts are commonly used in industries such as agriculture, construction, and mining where regular forklifts may struggle to perform.
Whether it’s lifting materials on a worksite or transporting equipment across rough terrains, rough terrain forklifts are equipped to handle the toughest tasks effectively and efficiently.
Industrial Side Loader Forklifts
Industrial side loader forklifts are a versatile and efficient solution for handling long and bulky loads in tight spaces. With their unique design, these forklifts allow operators to load and unload materials from the side, rather than from the front or rear like traditional forklifts.
This makes them ideal for navigating narrow aisles and confined areas where maneuverability is crucial. Equipped with sturdy forks that extend sideways, industrial side loader forklifts provide excellent stability and can lift heavy loads with ease.
Their ability to transport long items such as lumber, pipes, or steel beams makes them indispensable in industries like construction, manufacturing, and logistics.
Telescopic Handler Forklifts
Telescopic handler forklifts, also known as telehandlers, are versatile machines commonly used in construction and agricultural industries. These forklifts have a telescoping boom that extends outward and upward, allowing them to reach high heights and lift heavy loads.
With their ability to extend and retract the boom, telehandlers can easily maneuver in tight spaces. They are equipped with forks or attachments such as buckets or platforms to handle a variety of materials.
Telehandlers are particularly useful for tasks like stacking pallets, loading/unloading trucks, or reaching elevated areas on construction sites. Their flexibility and lifting capacity make them an essential tool for many job sites.
In addition to their impressive lifting capabilities, telescopic handler forklifts offer other features that enhance productivity and safety. Many models come with 4-wheel drive functionality for better traction on rough terrains, making them suitable for outdoor applications as well.
Some telehandlers may have a rotating capability which allows operators to move the load horizontally without repositioning the entire machine. This feature is especially helpful when working in confined areas where turning space is limited.
When operating a telescopic handler forklift, it’s important to receive proper training and certification from accredited institutions like Forklift Academy or the Forklift Training Academy.
Familiarize yourself with the controls and safety guidelines before operation to ensure optimal performance while minimizing risks of accidents or damage.
Applications of Forklift Types
– Food and beverage industry: Forklifts are commonly used in the food and beverage industry to efficiently transport pallets of products within warehouses or distribution centers.
– General warehouse use: Forklifts are essential for various tasks in warehouses, including loading/unloading trucks, moving pallets, and stacking materials on high shelves.
– Cold storage: Forklifts designed for cold storage environments can withstand low temperatures while safely moving goods in refrigerated warehouses.
– Retail: Forklifts play a vital role in retail operations by assisting with inventory management, stocking shelves, and transporting merchandise from the backroom to the sales floor.
– Freight transportation: Forklifts equipped with specialized attachments enable efficient loading/unloading of cargo containers or trailers at shipping docks.
Food and beverage industry
In the food and beverage industry, forklifts play a crucial role in various operations. They are used to transport goods within warehouses and production areas, making it easier to move heavy pallets of ingredients or finished products.
Forklifts also help with stacking products on shelves, maximizing storage space. Additionally, they aid in loading and unloading trucks for transportation purposes. Overall, forklifts are essential equipment in the food and beverage industry, improving efficiency and productivity.
General warehouse use
General warehouse use is one of the most common applications for forklifts. These versatile machines are essential in warehouses for moving and stacking goods efficiently. Whether it’s unloading trucks, organizing inventory, or loading pallets onto shelves, forklifts play a crucial role in daily operations.
With their ability to navigate narrow aisles and lift heavy loads, forklifts make it easier to maximize storage space in warehouses. They can quickly transport goods from one location to another, saving valuable time and reducing manual labor.
Forklift operators are trained to handle different types of loads with care while ensuring safety regulations are followed.
In a bustling warehouse environment, having reliable and well-maintained forklifts is key to maintaining productivity levels. Regular maintenance checks and routine inspections ensure that the machines are always ready for use.
From small electric forklifts to larger IC models, there is a wide range of options available based on the specific needs and requirements of each warehouse operation.
Cold storage
Cold storage is a crucial application for forklifts in industries such as food and beverage. These specialized types of forklifts are designed to withstand low temperatures and operate efficiently in cold environments.
They are equipped with features like insulated cabins, temperature-controlled compartments, and special tires that provide increased traction on slippery surfaces. Forklifts used in cold storage facilities play a vital role in transporting goods from one area to another safely and efficiently, ensuring that perishable items remain fresh throughout the entire process.
Retail
Retail businesses rely heavily on forklifts to efficiently move and handle inventory. With the wide range of forklift types available, retailers can choose the one that best suits their specific needs.
Whether it’s unloading shipments, organizing stock in the backroom, or moving products onto store shelves, forklifts play a vital role in keeping retail operations running smoothly.
The right forklift can help improve productivity, reduce manual labor, and enhance safety in a retail setting.
Freight transportation
Freight transportation is a crucial application for different types of forklifts. Whether it’s moving pallets of goods in a warehouse or loading and unloading trucks, forklifts play a vital role in keeping the supply chain running smoothly.
Different types of forklifts, such as industrial counterbalance forklifts and side loader forklifts, are commonly used in freight transportation. They are designed to handle heavy loads efficiently and navigate narrow spaces with ease.
With their versatility and strength, these forklifts help ensure that goods get transported from one place to another safely and efficiently.
How to Choose the Right Forklift
To choose the right forklift, consider the environment and terrain, evaluate weight and size of materials to be lifted, determine necessary lift height, assess the need for specialized attachments, and consider budget and maintenance costs.
Consider the environment and terrain
When choosing the right forklift, it is important to consider the environment and terrain in which it will be used. Different types of forklifts are designed to operate in specific environments.
For indoor use, electric forklifts or reach trucks are suitable options. If you need a forklift to work outdoors on rough terrains, a rough terrain forklift would be more appropriate.
By considering the environment and terrain, you can select a forklift that is best suited to handle the demands of your specific workplace conditions without compromising safety or efficiency.
Evaluate the weight and size of materials to be lifted
To choose the right forklift, it’s important to evaluate the weight and size of the materials you’ll be lifting. This will help determine the capacity and reach requirements of the forklift needed.
Assessing the weight and size of your materials ensures that you select a forklift that can handle them safely and efficiently. By accurately evaluating these factors, you can ensure smooth operations and avoid any potential accidents or damage to both the materials being lifted and the forklift itself.
Determine the necessary lift height
To choose the right forklift, it is crucial to determine the necessary lift height. This involves assessing how high materials need to be lifted in your specific environment. Factors such as storage racks or shelves should be considered when determining lift height requirements.
By accurately determining lift height needs, you can ensure that the chosen forklift will have the capability to safely and efficiently handle your lifting tasks without any limitations.
Assess the need for specialized attachments
To choose the right forklift, it’s important to assess the need for specialized attachments. Specialized attachments can enhance the versatility and efficiency of a forklift, allowing it to perform specific tasks beyond standard lifting and carrying operations.
These attachments can include options like clamps, fork positioners, rotators, and side shifters. By evaluating your specific requirements and considering what additional functions may be necessary for your operations, you can determine whether specialized attachments are needed.
This will ensure that your forklift is equipped to handle tasks such as handling different pallet types or fragile loads with precision and safety. Assessing the need for specialized attachments helps in selecting a forklift that best suits your unique operational needs without compromising on productivity or workplace safety.
Consider budget and maintenance costs
When choosing the right forklift, it’s important to consider budget and maintenance costs. Assessing how much you are willing to spend on purchasing or renting a forklift is crucial in making a cost-effective decision.
In addition, don’t forget to factor in ongoing maintenance expenses such as regular servicing, repairs, and replacement parts. By considering both your budget and long-term maintenance costs, you can ensure that you make an informed choice that fits within your financial capabilities.
Conclusion
In conclusion, understanding the various types of forklifts and their uses is crucial in determining which one is best suited for your specific needs. Whether you’re working in a warehouse, cold storage facility, or retail space, there’s a forklift type that can help improve efficiency and productivity.
By considering factors such as environment, material weight, lift height, attachments needed, and budgetary constraints, you’ll be able to choose the right forklift that meets all your requirements.
FAQs
1. What are the top 7 types of forklifts?
The top 7 types of forklifts include individual, stand up and Cherry Picker forklift among others.
2. How is a Cherry Picker forklift used?
A Cherry Picker forklift is often used in warehouses or outdoor jobs to lift workers or materials to great heights.
3. When should I use an Individual Forklift?
Individual Forklifts are mainly utilized when there’s a need to move heavy objects around a warehouse or construction site.
4. Can you tell me more about the Stand Up Forklift?
Stand Up Forklifts allow operators easy access, making them ideal for applications with shorter run times where getting on and off frequently is required.
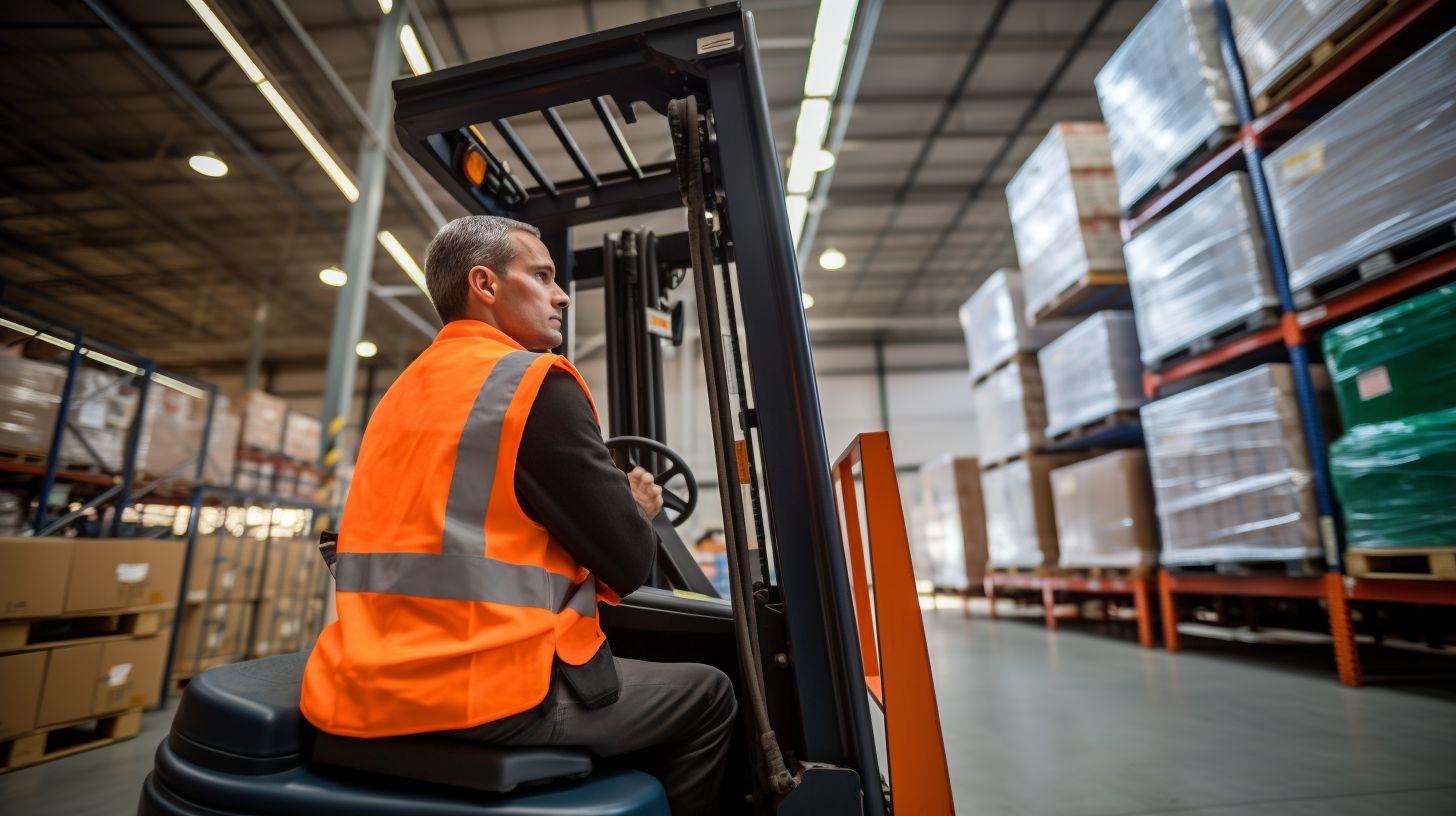
Understanding the implications of Occupational Safety and Health Administration (OSHA) in forklift training can seem intimidating. Established by the U.S. Department of Labor, OSHA plays a vital role in ensuring safe operational practices across diverse industries.
This blog post decodes OSHA’s regulations specific to forklift training, helping you ascertain your compliance as an employer or operator. Dive in, and discover a world where safety meets skill!
Key Takeaways
- OSHA stands for Occupational Safety and Health Administration in forklift training.
- OSHA plays a crucial role in ensuring safe and healthy working conditions by setting guidelines and enforcing them through regular inspections.
- Employers are required to follow OSHA’s guidelines for formal instruction, practical training, and creating detailed operating procedures.
- Forklift operators must meet certain qualifications under OSHA standards, including demonstrating competence in operating a forklift safely, understanding workplace conditions, and completing formal instruction.
Understanding OSHA in Forklift Training
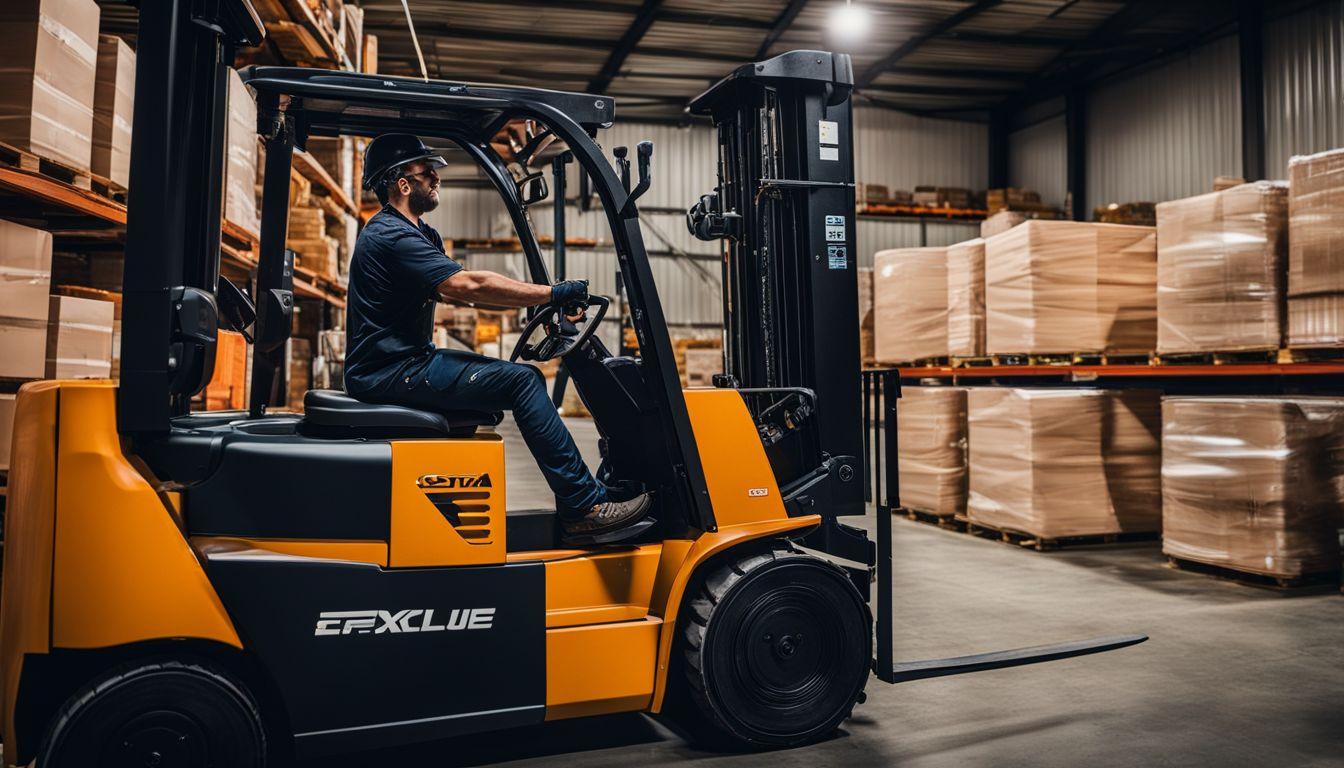
The Occupational Safety and Health Administration (OSHA) plays a crucial role in ensuring forklift operators receive proper training to prevent accidents and ensure workplace safety.
Overview of the Occupational Safety and Health Administration (OSHA)
OSHA, short for Occupational Safety and Health Administration, operates under the U.S. Department of Labor. It is a federal government agency responsible for upholding safe and healthy working conditions across America by setting guidelines and enforcing them through regular inspections.
They cover all industries, including operations involving powered industrial trucks like forklifts. Their website offers multilingual information on all aspects of safety at the workplace, including comprehensive resources about safe use of forklifts.
An essential feature they offer is an eTool named “Powered Industrial Trucks (Forklift)”, which provides details about various types of forklifts and their safe operation procedures in an accessible manner.
OSHA firmly believes in training as a vital contributor to reducing accidents – their research shows most incidents involving forklifts could have been avoided with proper training.
Role of OSHA in Forklift Training
OSHA plays a significant role in forklift training, setting out stringent requirements to ensure employee safety. Employers are required to follow OSHA’s guidelines for both formal instruction and practical training of their operators.
One of the primary responsibilities is creating detailed operating procedures that align with federal government websites and regulations set by the U.S. Department of Labor. This includes regulating vehicle stability, capacity, inspection protocols, refueling methods, charging/recharging batteries as well as load manipulation techniques like stacking and unstacking.
The aim is not only to maintain safe truck operation but also minimize accidents through hazard identification and effective supervision measures.
OSHA Forklift Training Requirements
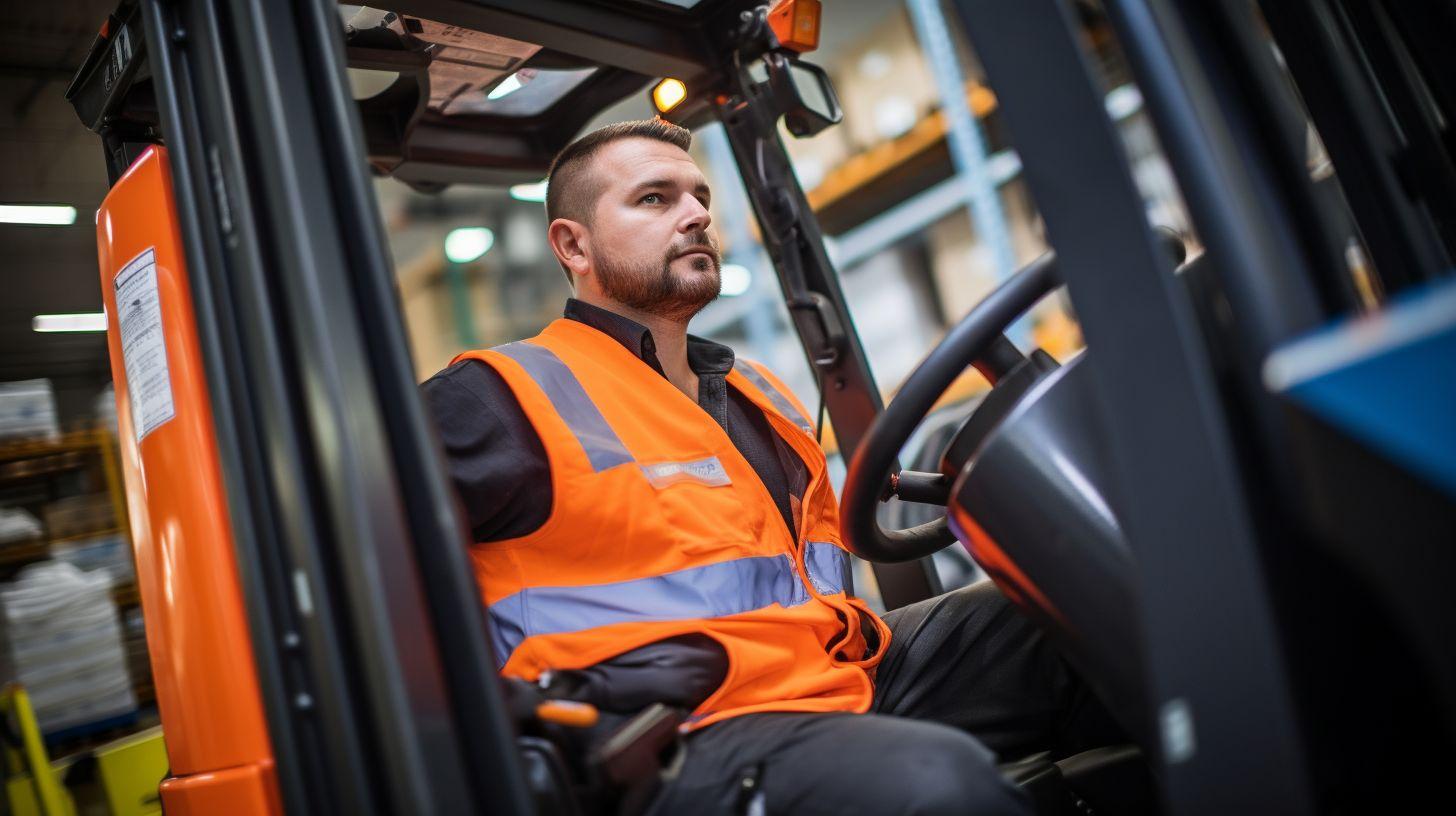
OSHA sets specific requirements for forklift training, including formal instruction, operator qualifications, trainer qualifications, and specialized training.
Formal instruction necessities
OSHA has specified important formal instruction necessities for forklift training. These guidelines ensure the safety and efficiency of operations in workplaces:
- Comprehensive training: The program must cover a wide range of topics, from truck-related issues to workplace-related issues.
- Classroom teaching: Online or in-person classroom instruction is required as a part of the training.
- Interactive sessions: OSHA stresses on interactive learning where trainees can ask questions.
- Multimedia usage: Utilization of video materials, written content, and practical demonstrations is encouraged in the training session.
- Use of qualified trainers: Trainers need to have the necessary knowledge, training, and experience to train operators accurately.
- Realistic simulation: OSHA requires realistic simulations that mirror actual workplace conditions for effective learning.
- Written exams: To gauge understanding and retention, written exams are required at the end of the formal instruction phase.
- Review of truck-related topics: This includes vehicle stability, vehicle capacity, refueling processes, load manipulation techniques among others.
Operator qualifications
Forklift operators must meet certain qualifications under OSHA standards to ensure safety in the workplace. These qualifications include:
- Demonstrating competence in operating a forklift safely
- Understanding the physical conditions of the workplace, including pedestrian traffic, ramps and grades, narrow aisles, and hazardous areas.
- Exhibiting knowledge about vehicle stability, vehicle capacity, and vehicle inspection and maintenance procedures.
- Having skills in load manipulation, stacking and unstacking items with a forklift.
- Completing formal instruction and practical training on forklift operation.
- Passing an operator performance evaluation conducted by trainers or evaluators with necessary knowledge, training, and experience.
- Retraining every three years or when changes in workplace conditions could affect safe operation of the truck.
Trainer qualifications
Trainers for OSHA forklift training must possess the necessary knowledge, training, and experience to effectively train operators and evaluate their competence. Here are important qualifications for trainers:
- Have in – depth knowledge of forklift operations, safety standards, and regulations
- Possess sufficient experience operating forklifts in various workplace environments
- Understand OSHA’s training requirements and guidelines for forklift operators
- Be familiar with different types of powered industrial trucks and their specific hazards
- Demonstrate effective communication skills to deliver clear instructions and explanations
- Show proficiency in conducting practical training sessions to simulate real – life scenarios
- Stay updated on the latest developments in forklift technology, safety practices, and regulations
- Provide evidence of successful completion of an accredited train-the-trainer program or certification course
Specialized Training
OSHA requires specialized training for forklift operators to ensure their safety and the safety of others. This training covers specific topics and skills that are essential for operating a powered industrial truck. The specialized training includes:
- Hazard identification: Operators learn how to identify potential hazards in the workplace, such as uneven surfaces, obstacles, or overhead obstructions.
- Load manipulation: Training focuses on proper techniques for picking up, carrying, and setting down loads safely and securely.
- Stacking and unstacking: Operators are taught how to stack and unstack materials correctly to prevent accidents and maintain stability.
- Operating limitations: Specialized training covers the limits of the forklift’s capabilities, including weight capacity and height restrictions.
- Hazardous areas: Operators learn how to navigate through hazardous areas in the workplace, such as areas with flammable materials or restricted spaces.
- Refueling procedures: Training includes instructions on safe refueling practices for different types of forklifts, whether they use batteries or fuel.
- Maintenance and repair procedures: Operators receive guidance on performing routine maintenance tasks and recognizing when a forklift needs repairs.
Common FAQs about OSHA Forklift Training
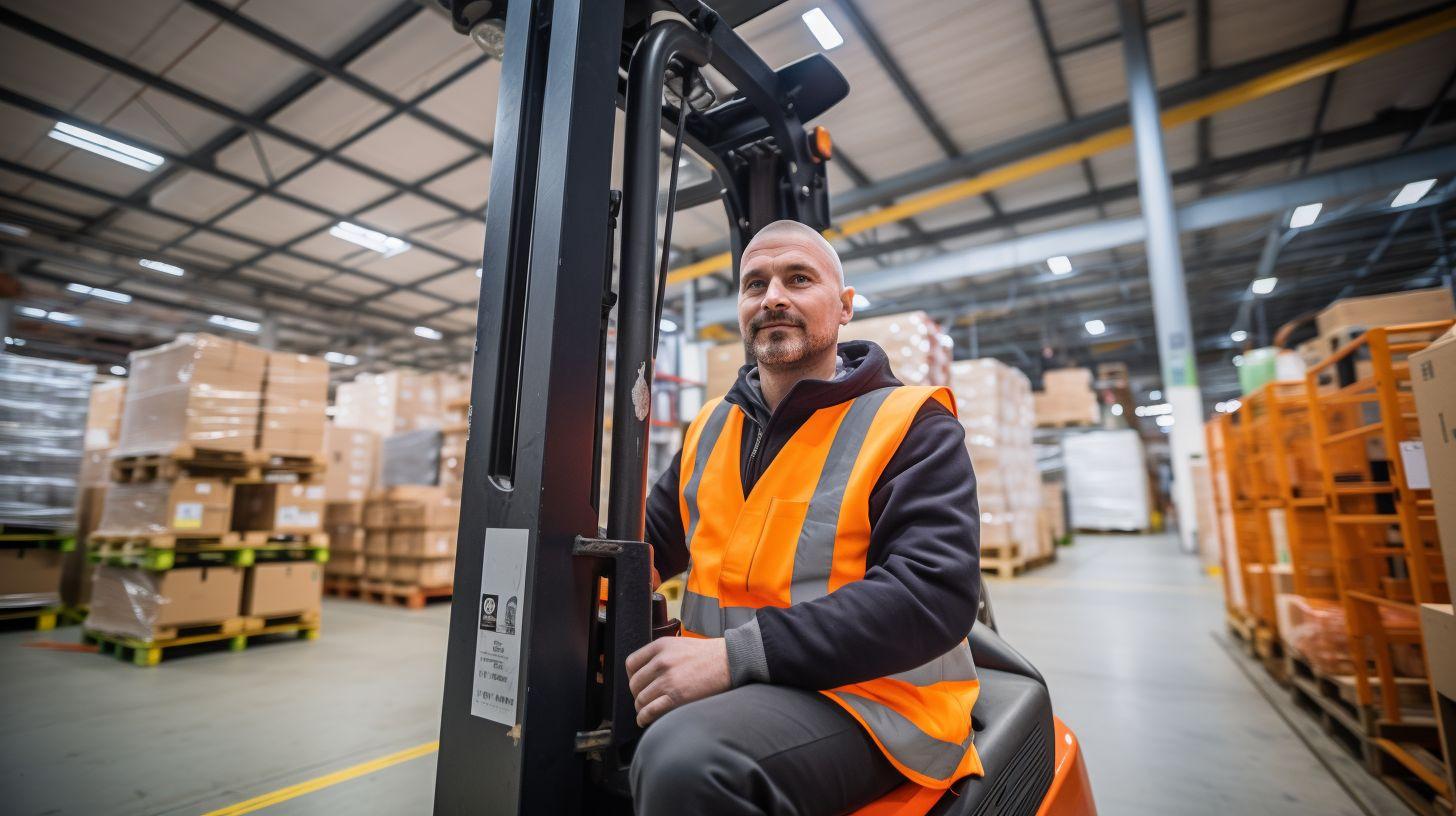
Are you wondering if annual OSHA forklift driver training is required? Who can train, evaluate, and certify forklift operators? Do you need to provide forklift operator training for each make and model? Find out the answers to these common questions and more in our blog on OSHA forklift training requirements.
Is annual OSHA forklift driver training required?
OSHA does not require annual forklift driver training. However, refresher training is necessary in certain situations such as unsafe operation or accidents. It’s important to stay updated on safety protocols and ensure that operators receive the necessary training to operate forklifts safely and effectively.
Who can train, evaluate, and certify forklift operators?
Trainers and evaluators for forklift operators must have the necessary knowledge, training, and experience to effectively train and assess competence. This means that any qualified person in the workplace can provide hands-on instruction and evaluation for forklift operators.
It is the employer’s responsibility to certify that their employees have received all required training and are capable of safely operating forklifts. While OSHA does not require a specific certification or ID for forklift operators, employers may choose to provide certificates or ID cards as evidence of training.
Ultimately, ensuring that only qualified individuals train, evaluate, and certify forklift operators is crucial in maintaining a safe work environment.
Do we need to provide forklift operator training for each make and model?
Forklift operator training is required for each “type” of truck, not necessarily for each make and model. This means that if you have different makes and models of forklifts that fall under the same type category, you do not need to provide separate training for each specific make and model.
However, it is important to ensure that your operators are trained on the specific type of truck they will be using in order to operate it safely and efficiently. Employers must evaluate the applicability and adequacy of prior training when employing new or temporary operators with previous forklift experience, but ultimately it is crucial to provide proper training based on the specific type of truck being used.
Conclusion
In conclusion, OSHA stands for Occupational Safety and Health Administration in forklift training. It is a crucial government agency that ensures safe and healthy working conditions.
By providing guidelines and resources, OSHA plays a vital role in promoting forklift operator safety and reducing workplace accidents.
FAQs
1. What does OSHA stand for in forklift training?
In forklift training, OSHA stands for Occupational Safety and Health Administration, a part of the U.S. Department of Labor responsible for safety standards.
2. What are the key components of OSHA’s Forklift Training Program?
The program includes understanding the workplace conditions, recognizing hazards such as narrow aisles or loading docks, operating procedures and maintenance guidance like vehicle inspections and refueling.
3. How often do I need to renew my Online Forklift Certification according to OSHA standards?
OSHA advises periodic refresher training and requires operator performance evaluation to maintain certification status.
4. Do Federal government websites offer online resources pertaining to Powered Industrial Trucks (Forklift) training assistance?
Yes, secure connection Federal government websites provide valuable information on topics ranging from legal compliance assistance to safe truck operation techniques that can aid in your own customized training program development.
5. Can I get certified as a Forklift Operator by going through an Online Forklift Training course?
Absolutely! Employers can issue you an employer certification after you have completed formal instruction followed by practical application based interactive fork lift simulation exercises alongside regular evaluations provided in a blended approach format online.
6. Does adhering strictly with rules highlighted under ‘Operating Limitations’ improve overall facility design?
Indeed it does! Recognizing and respecting vehicle capacity limits not only safeguards against accidents but also helps streamline facility design; contributing significantly towards achieving optimum energy efficiency within industrial settings.
Forklift accidents can be serious and costly for businesses. OSHA’s standards exist to keep workers safe around these powerful machines. Our blog lays out key details to help meet training requirements and avoid fines.
Keep reading to make safety a priority!
Key Takeaways
- Employers must provide comprehensive forklift training to their workers according to OSHA regulations, ensuring that the training covers essential safety topics and is conducted by a qualified trainer.
- Forklift training should combine classroom learning with hands – on experience to ensure operators can apply what they’ve learned about physical hazards directly to their work environment.
- Refresher training every three years or after an accident or near-miss incident is crucial to reinforce safety practices and maintain regulatory compliance, as per OSHA guidelines.
- Staying current with the most recent OSHA regulations for forklift operators is vital in promoting a safe working environment while avoiding potential penalties or liability issues.
Understanding the Occupational Safety and Health Administration (OSHA)
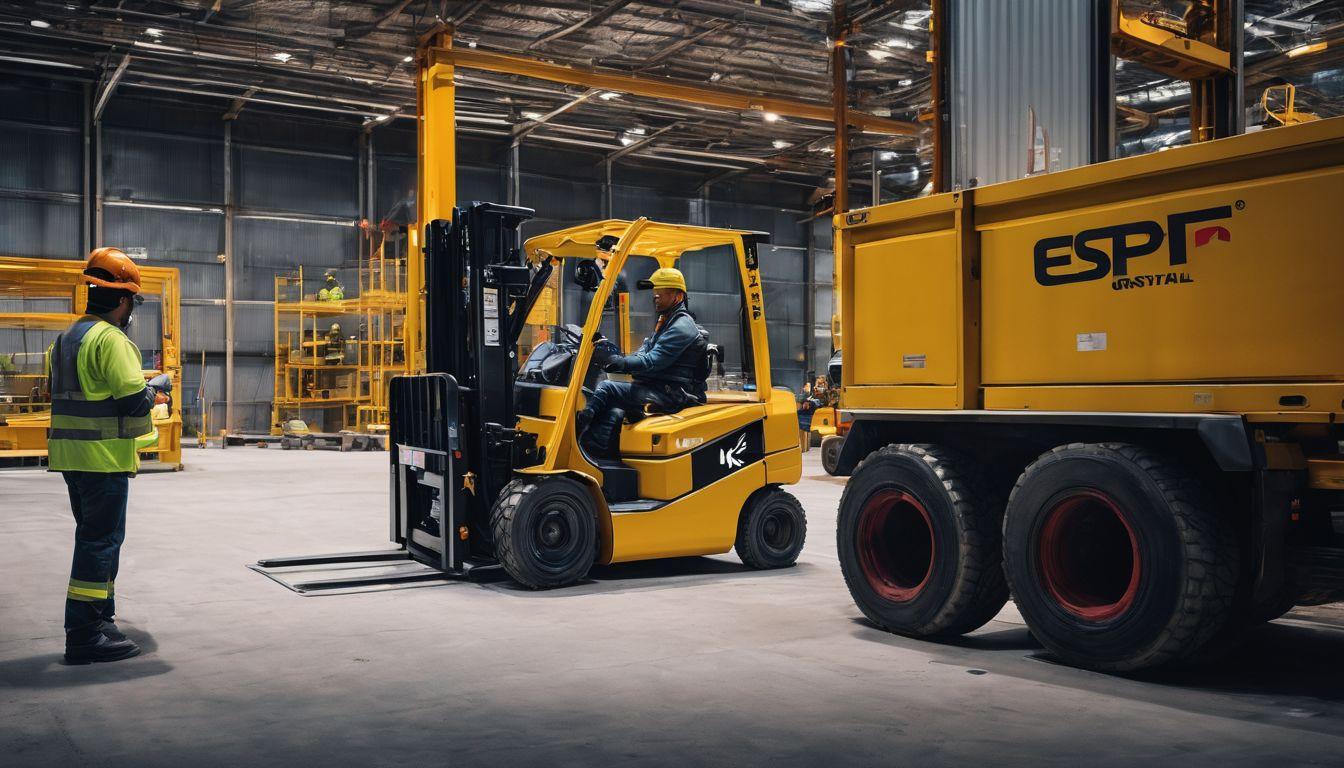
The Occupational Safety and Health Administration, known as OSHA, plays a crucial role in ensuring workplace safety across the United States. Created by Congress under the Occupational Safety and Health Act of 1970, this agency sets and enforces protective workplace safety and health standards.
OSHA’s mission is clear: to prevent work-related injuries, illnesses, and deaths by issuing rules on everything from forklift operation to emergency exits.
Employers are responsible for providing a safe working environment that complies with OSHA regulations. This includes conducting regular inspections, providing essential safety training to employees, and correcting any identified hazards promptly.
Specific to forklifts—a common yet potentially dangerous piece of equipment—OSHA mandates rigorous training program sto safeguard operators from accidents like overturns or collisions which can lead to severe injuries or fatalities.
Compliance with these regulations is not optional; failure to adhere can result in hefty fines and increased scrutiny from this federal agency dedicated to occupational safety and health.
OSHA-Compliant Forklift Safety Training Standards
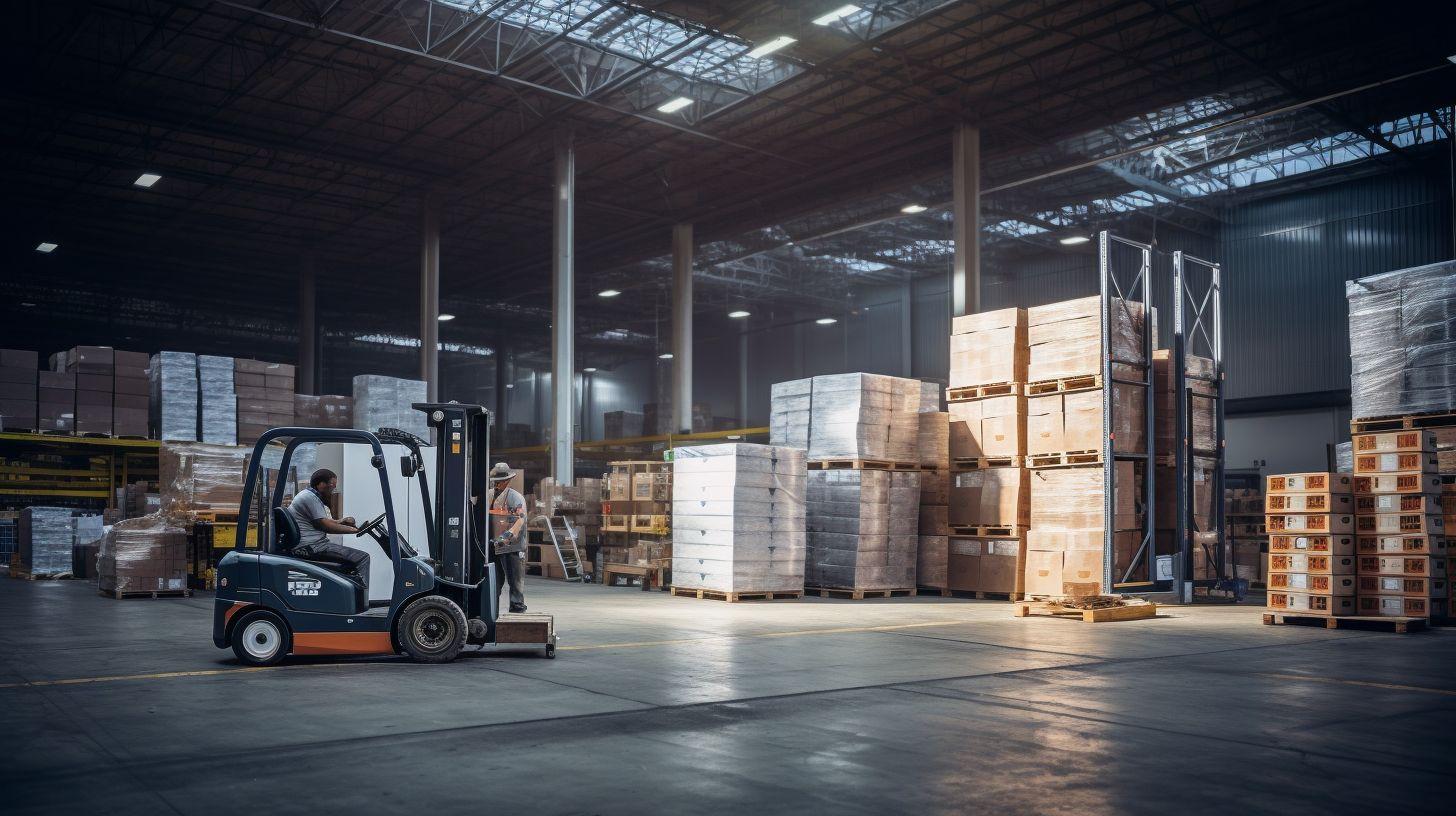
The OSHA-compliant forklift safety training standards include specific requirements for training content, format, trainers, and timing to ensure the safe operation of forklifts in the workplace.
Training Requirements Under OSHA Regulations
Employers must provide comprehensive forklift training to their workers. To comply with OSHA regulations, this training must meet specific criteria and cover essential safety topics.
- Every forklift operator needs proper certification before handling equipment.
- A qualified trainer, who has the necessary knowledge and experience, should conduct the training.
- Training programs must include instructions on safely operating a forklift in various conditions.
- Regular updates and reviews of the training material ensure that it meets current OSHA standards.
- Forklift safety sessions should cover how to avoid workplace injuries, such as slips, trips, and falls.
- Practical, hands – on practice is crucial for operators to gain experience in a controlled environment.
- Employers are required to keep detailed records of all forklift training conducted, which includes certification dates and the subjects that were taught.
- In addition to operation techniques, maintenance procedures should be taught to reduce risks related to fuel systems, exhaust emissions, and battery care.
- The importance of using seat belts while operating a forklift truck must be emphasized during the training sessions.
- Operators need education on recognizing potential fire hazards associated with flammable materials or combustible storage batteries found in electric forklifts.
- Training must address site – specific hazards such as loading dock safety and materials handling near flammable substances.
- Safety precautions like wearing high – visibility jackets and hard hats are part of the core content in compliance training programs.
Forklift Training Format
Forklift training combines classroom learning with hands-on experience. Instructors give operators the rundown on safety protocols, maintenance checks, and operational tactics for various types of forklifts: from electric pallet jacks to heavy-duty forklift trucks.
Trainees must grasp the specifics of handling these vehicles safely before moving to practical exercises. These exercises take place in settings that mimic real-world scenarios where operators might navigate through warehouses, maneuver around pallets, or transport materials.
Hands-on sessions focus on teaching skills like safe stacking, load balancing, and navigating tight spaces. Operators learn how to inspect their equipment daily, identifying any potential issues that could pose risks during operation.
Real-life conditions are simulated to ensure trainees can apply what they’ve learned about physical hazards directly to their work environment. From using a forklift truck in routine tasks to responding appropriately during an emergency – each aspect is crucial for compliance with OSHA standards and ensuring workplace safety.
Training Content
Training content for forklift operators must dive into essential topics such as proper vehicle inspection and regular maintenance procedures. This includes checking the fork truck before each shift for any potential issues that could lead to malfunctions or safety hazards.
Operators learn how to identify problems with pneumatic tires, internal combustion engines, or electronic communications systems that may affect operation.
The curriculum also zeroes in on safe operating practices tailored to specific work environments. For instance, someone working in construction might face different risks than someone operating a cherry picker in a warehouse setting.
Training covers the safe handling of materials, avoiding incidents with pedestrians, and understanding various load capacities. It emphasizes best practices when lifting, stacking, or placing items like boxes or heavy equipment.
Operators receive instruction on recognizing workplace hazards unique to their job site—be it exposure to explosive materials or navigating tight spaces densely packed with goods.
Detailed training helps them respond appropriately during emergencies and understand labor laws tied to their employment duties. This comprehensive approach ensures operators are not only efficient but also uphold safety in the workplace at all times.
Training the Trainers
Selecting a qualified trainer with the necessary knowledge and experience is crucial for effective forklift operator training. It’s essential to ensure that trainers are well-versed in OSHA requirements, safe operation, maintenance, and other relevant topics.
Keeping accurate training records, regularly reviewing and updating programs, and conducting refresher training as required by OSHA are vital steps for ensuring compliance with forklift training safety standards.
Timing of forklift training
Employers must schedule forklift training promptly upon hiring and before the operator engages in any forklift operation. Refresher training every three years or after an accident or near-miss incident is crucial to reinforce safety practices and maintain regulatory compliance.
Additionally, employers should provide further training if operators are observed operating a forklift unsafely, ensuring employees remain knowledgeable about safe practices.
Forklift training timing is essential as it helps in reducing workplace accidents leading to property damage, injuries, and even fatalities. Such timely adherence to OSHA regulations demonstrates a commitment to employee safety while maintaining operational efficiency within the organization.
Most Recent OSHA Regulations for Forklift Operators
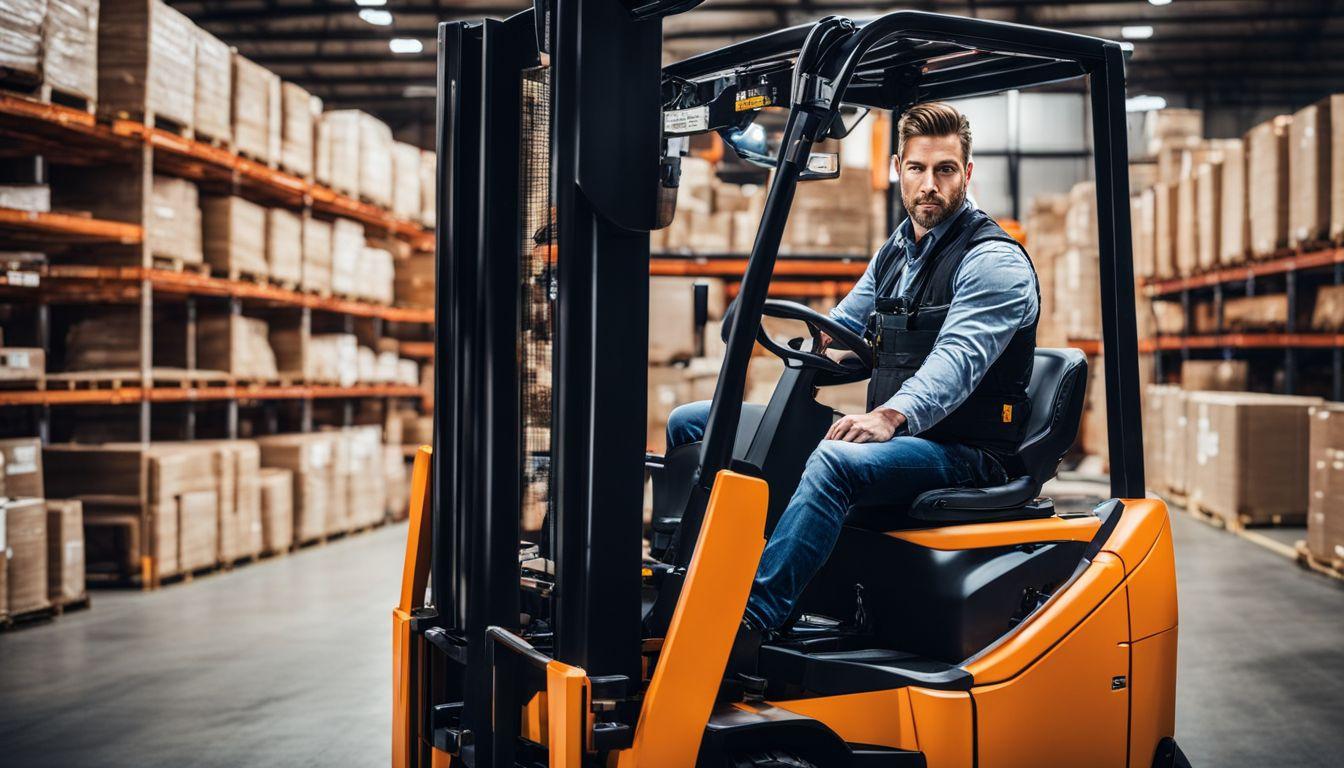
OSHA recently updated regulations to enhance forklift operator safety. These changes include stricter requirements for training and certification, as well as an emphasis on ongoing education and recertification.
Employers must ensure that their forklift operators are informed about these latest standards to maintain compliance.
These new regulations also incorporate advancements in forklift technology and safety measures, reflecting the industry’s continuous evolution. Employers need to stay current with OSHA updates and modify their training programs accordingly.
Ensuring compliance with the most recent OSHA regulations is vital in promoting a safe working environment while avoiding potential penalties or liability issues.
Different Types of Forklifts and Their Safety Standards
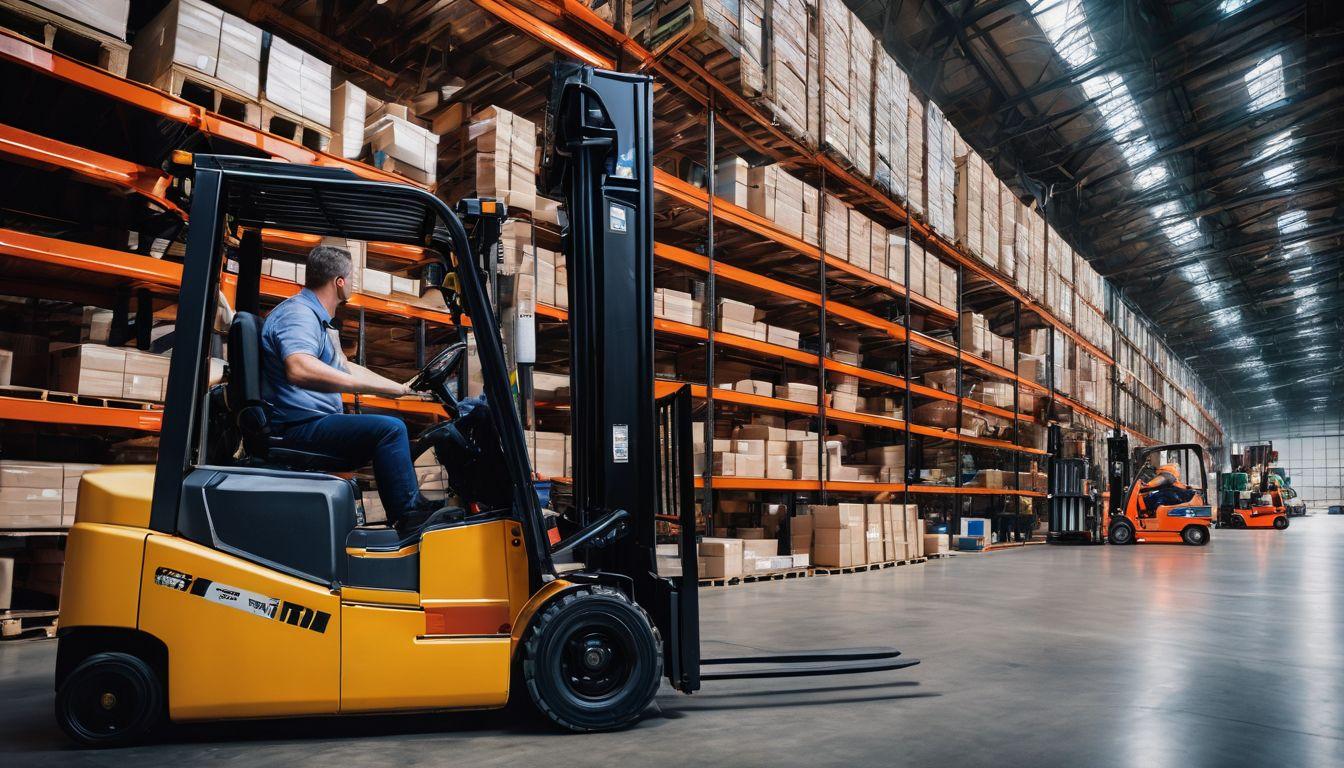
Understanding the safety standards for different types of forklifts is crucial for ensuring compliance with OSHA regulations. From electric pallet jacks to heavy duty forklifts, each type requires specific training and safety measures.
Read on to learn more about how to maintain compliance with OSHA standards for various types of forklifts.
Electric Forklifts
Employers must ensure that electric forklift operators receive proper OSHA-compliant training, covering topics such as inspection, maintenance, safe operation, and specific workplace hazards.
This training should combine formal instruction with practical experience to certify operators before they can work with electric forklifts. Employers are also required to maintain detailed records of the training provided and certification for all types of forklifts, including electric ones.
OSHA mandates refresher training every three years or when an operator is observed operating a forklift in an unsafe manner, has been involved in an accident or near-miss incident.
Electric Pallet Jacks
Employers must ensure that electric pallet jack operators receive proper OSHA-compliant training and certification. Training programs should cover OSHA requirements, safe operation, maintenance, and relevant topics.
Accurate records of training dates, topics covered, and employee certifications must be maintained by the employers to comply with OSHA regulations. It is crucial for employers to regularly review and update their training programs for electric pallet jack operators to avoid significant fines and penalties resulting from non-compliance.
Reach Trucks
Employers need to provide specific training for reach truck operators concerning workplace hazards associated with these vehicles. It is critical that employers adhere to OSHA regulations for reach trucks and ensure a safe work environment.
Keeping detailed records of reach truck training and certification for operators is essential, as well as conducting refresher training every three years or after specific incidents.
Relevant Keywords: reach trucks, OSHA regulations, workplace hazards, training, certification
Internal Combustion: Cushion Tires
Forklifts with cushion tires are commonly used indoors and are powered by internal combustion engines. Operators must undergo training to handle forklifts outfitted with these tires, specifically covering inspection and maintenance.
Employers need to maintain detailed certification records that include specific training for operating cushion tire forklifts. Regular reviews of training programs should prioritize the safe operation of forklifts equipped with cushion tires, ensuring compliance with OSHA standards.
Heavy Duty Forklifts
Heavy duty forklift operators need to undergo comprehensive training and certification as per OSHA standards. Employers must ensure that the training program covers safe operation, maintenance, and other crucial topics.
OSHA mandates a combination of formal instruction and hands-on training, with performance evaluations in the workplace. Refresher training is also necessary every three years to maintain compliance with safety standards.
The heavy-duty forklifts are commonly used in various industries like general manufacturing, freight handling as well as in warehouse operations. Hence, it is crucial for employers to prioritize robust training programs to ensure safe operation and compliance with OSHA regulations for heavy duty forklifts.
Automated Guided Vehicles
Automated Guided Vehicles, known as AGVs, are self-operating vehicles used for the movement of materials in warehouses and manufacturing facilities. They are guided by a combination of software and sensor-based technology that enables them to navigate through the workspace without human intervention.
These innovative vehicles can transport heavy loads, such as pallets or containers, efficiently and safely. Employers incorporating AGVs into their operations need to ensure that they comply with OSHA’s safety standards regarding training requirements for employees who will be working alongside or in close proximity to these automated vehicles.
AGVs contribute to improving workplace safety by reducing the risk of accidents caused by human error during material handling activities. It is essential for employers to provide comprehensive training programs focusing on safe interaction with AGVs, including understanding their operation, navigation patterns, emergency procedures, and potential hazards associated with their use.
Improving Safety in Different Industries
The safety standards for forklift operations are crucial in various industries including food storage, general warehouse, general manufacturing, retail, and freight. Each industry has its own unique challenges and requirements when it comes to forklift safety, and it is important for employers to train their employees accordingly.
Food Storage
Employers in the food storage industry must ensure forklift operators are properly trained and certified to comply with OSHA standards. Training programs for forklift operators should cover OSHA requirements, safe operation, maintenance, and other relevant topics.
Employers are responsible for maintaining accurate records of forklift training including dates, topics covered, and employee certifications. OSHA requires employers to regularly review and update training programs to ensure compliance with evolving standards and best practices.
General Warehouse
General warehouses must ensure that forklift operators receive proper training and certification, as required by OSHA regulations. Accurate training records must be maintained, and regular review and updates to the training programs could help in staying compliant with OSHA standards.
The goal is to prevent workplace accidents and injuries through adherence to safety protocols outlined by OSHA. Refresher training for forklift operators should be provided every three years or following an unsafe operation, accident, or near-miss incident.
By complying with these essential requirements, general warehouses can provide a safe working environment while avoiding penalties and fines from OSHA.
General Manufacturing
Manufacturing facilities utilizing forklifts must adhere to OSHA forklift training safety standards to ensure a safe working environment. Employers in general manufacturing settings are responsible for providing comprehensive forklift training programs that cover OSHA requirements, safe operation, and maintenance protocols.
In addition, these employers must maintain accurate records of employee certifications, including refresher trainings every three years or after any accidents involving a forklift operator.
Failure to comply with OSHA regulations can result in significant fines and penalties.
Retail
Retail environments often involve the operation of forklifts for various tasks, such as stocking and organizing inventory. Ensuring compliance with OSHA standards is crucial to protect employees and customers from potential hazards.
Identifying the need for training among retail personnel is essential, and developing a comprehensive program that covers safe operation, maintenance, and relevant topics is vital in this setting.
Regularly reviewing and updating the training program will help ensure ongoing compliance with evolving OSHA standards while also maintaining an effective safety protocol in the retail environment.
Freight
Freight companies need to prioritize forklift safety training to ensure compliance with OSHA regulations. Employers should assess their workforce, identifying those who require forklift training and certification.
Qualified trainers with the necessary knowledge and experience must be selected to effectively train forklift operators in freight industries.
Forklift operators in the freight industry are required to adhere strictly to OSHA regulations, ensuring the safe operation of different types of forklifts such as electric pallet jacks or heavy-duty forklifts.
Conclusion
FAQs
1. What does OSHA require for safe forklift operation by employees?
OSHA demands that all employees who operate a forklift are properly trained in safety practices to prevent accidents and injuries on the job.
2. Can I hire a contractor to train my workers on forklift safety?
Yes, you can bring in a qualified contractor who knows the ins and outs of OSHA standards to ensure your workers receive comprehensive forklift training.
3. Does OSHA need information about our forklift training program?
Absolutely, you must keep detailed records that show how your training program meets OSHA’s requirements and provide this information when requested.
4. Are there different safety standards if we use specialized equipment like a vape warehouse forklift?
Even with specialized equipment like forklifts in vape warehouses, it’s critical to adhere to OSHA’s regulations tailored to specific machinery types to guarantee worker safety.
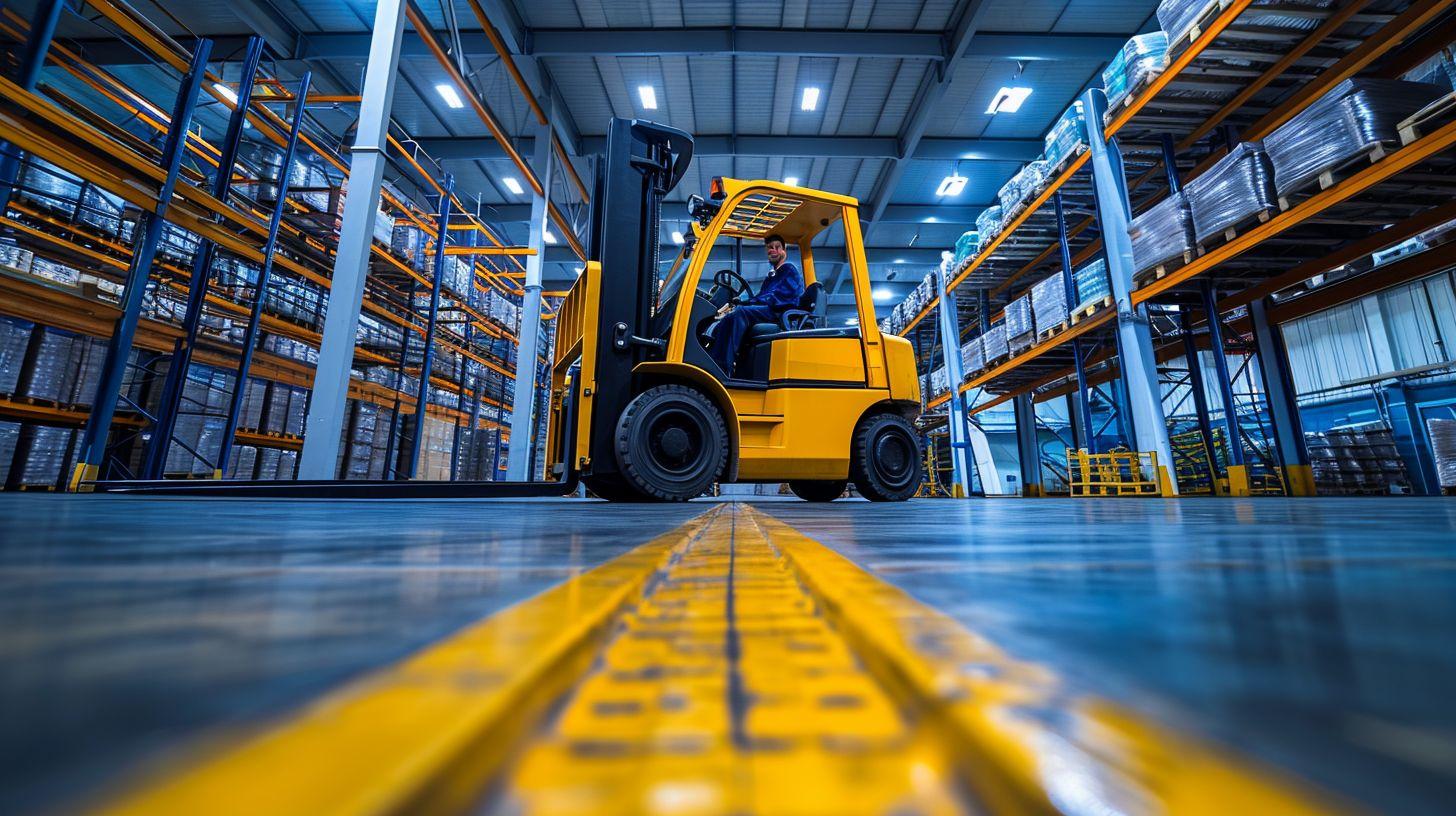
Before powering up a forklift, there’s an essential routine to keep everyone safe. Did you know that OSHA insists on daily safety checks before operating any forklift? Our blog walks through the crucial steps to ensure your lift is ready and secure, safeguarding you and your team.
Keep reading; it’s all about staying safe out there!
Key Takeaways
- Every day, forklift operators must conduct safety checks before using the equipment to avoid accidents and maintain efficiency. This includes both visual pre-operation inspections and operational inspections.
- Specific checklists should be used that include examining fluid levels, brakes, steering, lights, alarms, and seatbelts to ensure everything functions properly according to OSHA guidelines.
- Different types of forklifts such as electric, internal combustion, and liquid propane have unique inspection requirements which must be carefully followed to ensure safe operation.
- Regular maintenance checks at 250 – hour intervals can catch minor issues before they become serious problems. More extensive checks should be performed every 500 hours and major maintenance is needed after 2,000 hours of operation.
- Cleanliness is vital not just for the machine’s longevity but also for safety; keeping a clean workspace helps identify hazards while operating a forklift.
Importance of Conducting Forklift Safety Checks
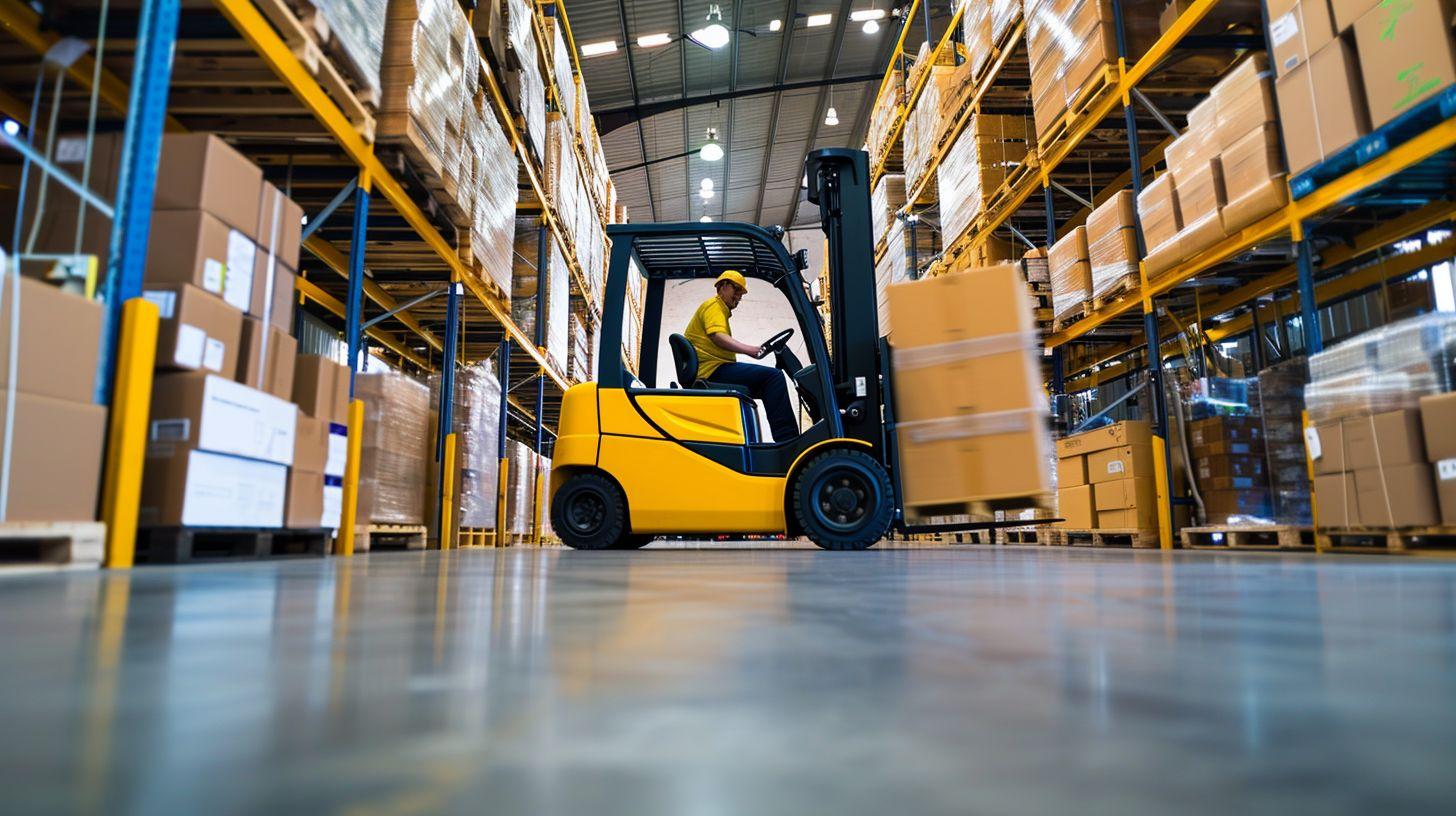
Conducting forklift safety checks before each shift can prevent accidents and save lives. Forklifts are heavy, powerful machines that pose serious risks if not properly maintained or operated.
Safety inspections uncover potential mechanical problems like faulty brakes, leaks in the hydraulic hoses, or damaged fork condition which could lead to equipment failure or accidents during operation.
Checking fluid levels and ensuring that forklift attachments are secure also minimizes the risk of malfunction.
Ensuring a forklift is in top working condition enhances workplace efficiency since regular maintenance reduces unexpected breakdowns and downtime. It’s crucial to ensure all safety decals and nameplates are legible and that limit switches function correctly to keep both the operator and surrounding employees safe from harm.
After completing safety checks, operators have peace of mind knowing their vehicle meets occupational safety standards set forth by agencies such as OSHA, reducing the likelihood of legal action due to non-compliance-related incidents.
Following thorough inspections, we move on to understanding how exactly these critical daily assessments are performed through an operational inspection checklist.
How to Conduct a Daily Forklift Safety Inspection
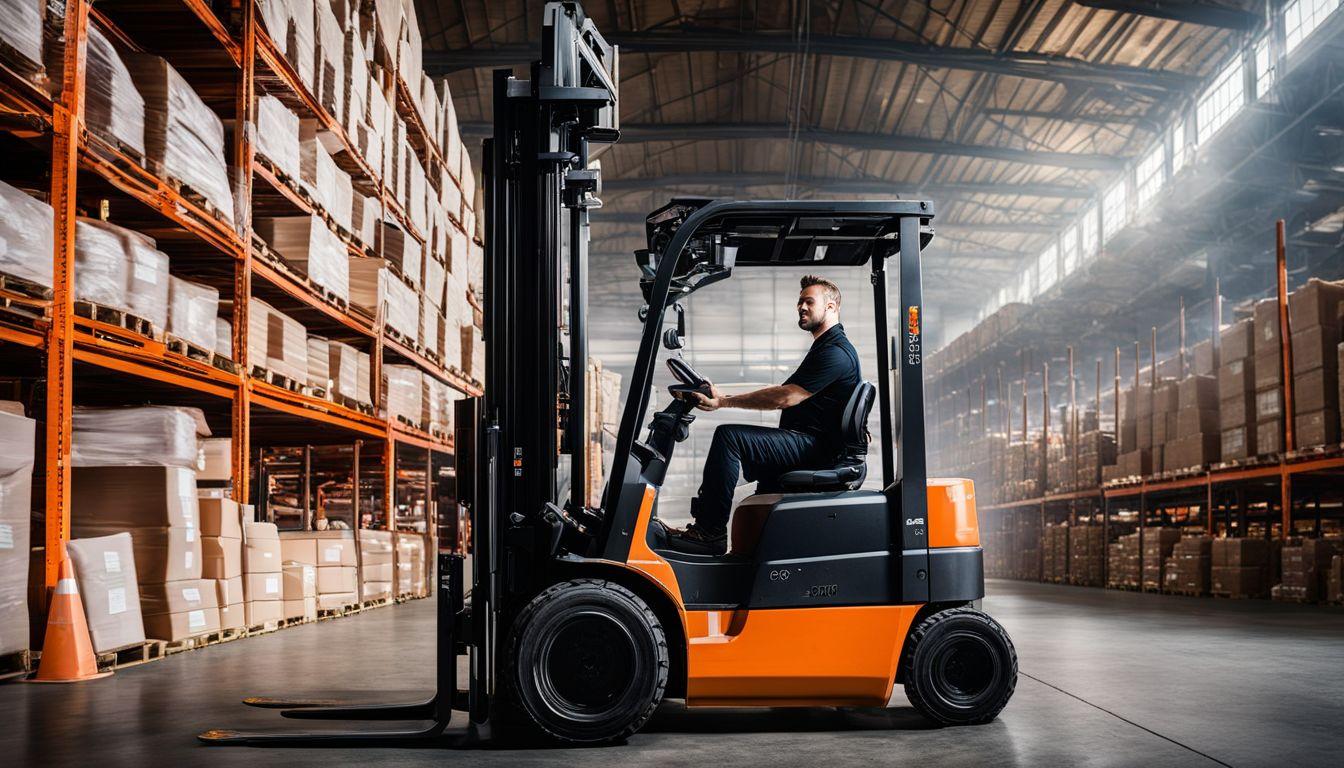
Before using a forklift, it is crucial to conduct a daily safety inspection. This includes visual pre-operation checks and operational inspections to ensure the forklift is in proper working condition.
Visual Pre-operation Inspection Checklists
Conducting a visual pre-operation inspection is mandatory for ensuring the safety and functionality of a forklift. These thorough checklists help operators identify any potential hazards or malfunctions before starting the machine.
- Check the operator compartment to ensure it is clean, with no loose bolts or damaged controls.
- Inspect the seat belt and parking brake to confirm they are functioning correctly and will hold the vehicle in place when engaged.
- Look over the mast and ensure its integrity; there should be no cracks, deformities, or hydraulic leaks.
- Examine forks, including the top clip retaining pin and heel, for any signs of wear, bending, or cracking that could lead to failures during use.
- Verify that load backrest extension is properly secured and capable of supporting a load without risk of shifting or collapse.
- Review both headlights and warning lights to make sure they are operational for visibility in dimly lit areas.
- Scan wheels and tires for damage like cuts or bulges that could impair safe operation of the lift truck.
- Test all gauges in the dashboard to confirm accurate readings that will guide safe operations throughout usage.
- Evaluate liquid levels such as coolant, engine oil, brake fluid, and if applicable, electrolyte levels in batteries; replenish as required following guidelines.
- Assess all belts and hoses under the hood for signs of wear or damage; replace parts showing excessive deterioration.
- Ensure battery restraints are secure to prevent movement that could disrupt electrical connections during operation.
- Confirm that safety decals and nameplates are clearly visible with legible operating instructions for driver reference.
Operational Inspection Checklist
Before a forklift takes on the day’s tasks, a thorough operational inspection is key. This process ensures each component functions correctly and safely.
- Start the forklift engine; listen for unusual noises that could signal malfunctions or needed repairs.
- Test the brake pedal to make sure it feels firm and brings the vehicle to a stop smoothly without any pulling to either side.
- Check that the steering mechanism operates easily and doesn’t stick, making sure it keeps the forklift on a steady course without any drift.
- Operate the lift control to raise and lower forks, ensuring smooth movement without delays or jerks.
- Inspect safety devices like lights, horns, and flashing beacons to confirm they are functional and visible from all directions.
- Examine the condition of seatbelts and other protective equipment; they must be in good shape to keep operators secure during use.
- Verify that all gauges are working correctly — fuel, battery charge, temperature, oil pressure — since these provide vital information about forklift health.
- Use tilt controls to move the mast forward and backward; it should do so freely with no stiffness or resistance.
- Activate warning signals such as backup alarms and check their audibility in a typical warehouse environment.
- Conduct tests on hydraulic systems by raising the load to full height then lowering it slowly; look out for leaks or drops in pressure that indicate issues.
- Monitor exhaust emissions for excessive smoke or fumes which can not only harm health but also suggest combustion problems.
- Confirm that radiator fluid levels are within acceptable limits, preventing overheating during extended operations.
Specific Inspections for Different Types of Forklifts
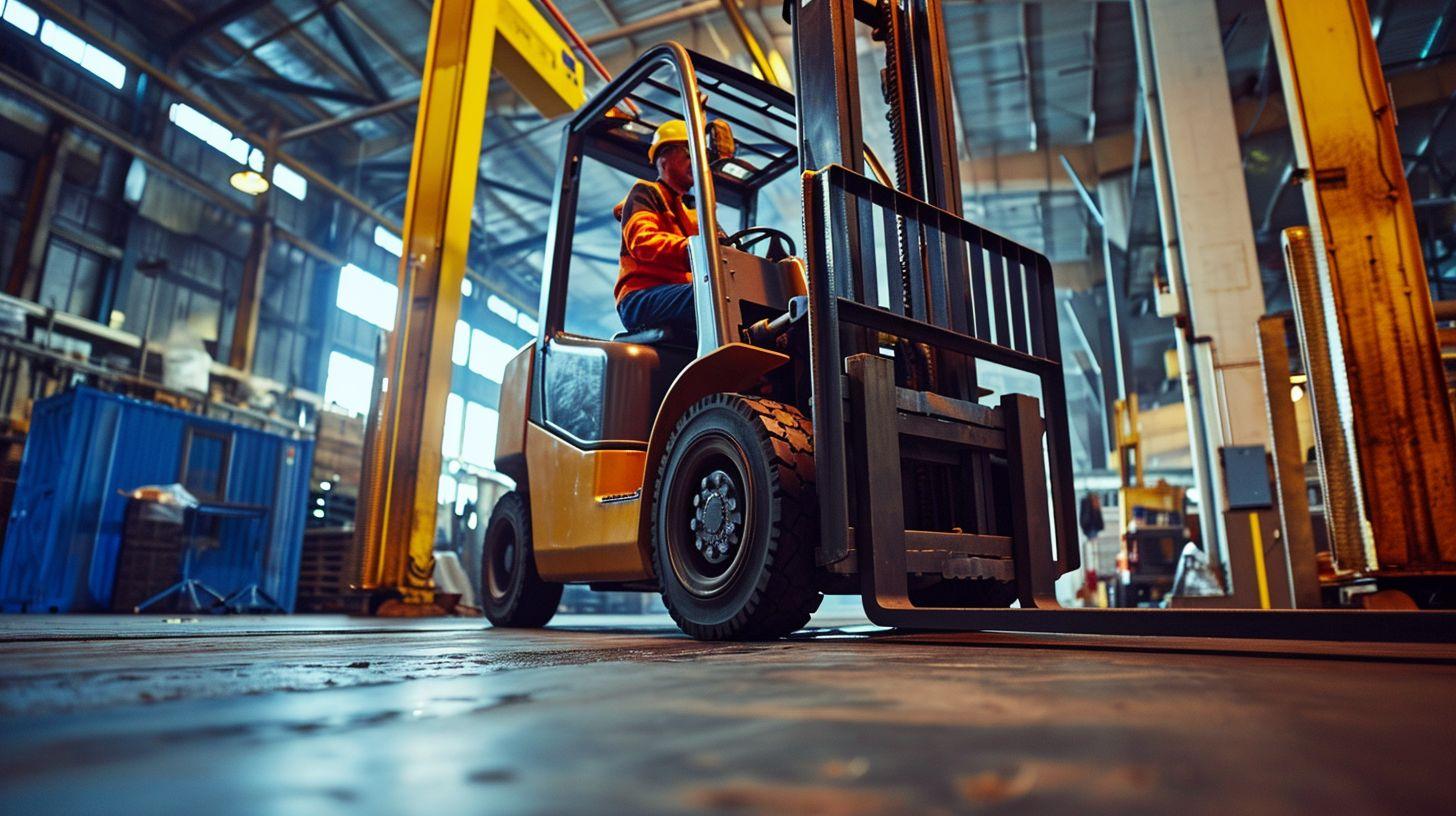
When it comes to conducting daily safety inspections, different types of forklifts require specific checks. For example, electric forklifts may need battery and charging system inspections, while internal combustion forklifts may require engine coolant and oil level checks.
Understanding the specific needs of each type of forklift is crucial in ensuring their safe operation.
Electric Forklifts
Electric forklifts demand a unique set of safety inspections before daily use. It’s essential to follow a comprehensive checklist to ensure they are operating safely.
- Start by inspecting the cables for any signs of wear or damage. Frayed or exposed wires can lead to electrical hazards.
- Check all connectors to make sure they are secure and free of corrosion, as poor connections can affect the forklift’s performance.
- Examine battery restraints to confirm they are in place and functioning properly. Batteries must be secured to avoid accidents during operation.
- Assess electrolyte levels in batteries, ensuring they are within recommended levels to maintain proper battery health and longevity.
- Make sure that the hood latch is firmly closed. An open latch can obstruct the operator’s view or lead to parts becoming dislodged.
Internal Combustion Forklifts
Before using an internal combustion forklift, it is crucial to conduct specific inspections to ensure its safe operation. Daily checks must include examining the engine oil, engine coolant, air filters, radiator, and hood latch for any signs of damage or leaks. It is also important to inspect the tires for proper inflation, wear, and tear.
Liquid Propane Forklifts
Liquid propane forklifts require specific inspections, including checking the tank mounting, pressure relief valve, connectors, hoses, tank condition, and proper fitting. These checks are vital to ensure safe operation and prevent accidents. Here are key components that need to be examined as part of the daily safety inspection:
- Tank Mounting: Verify that the tank is securely and properly mounted to the forklift frame.
- Pressure Relief Valve: Inspect the pressure relief valve to ensure it is in good working condition and free from blockages.
- Connectors and Hoses: Check all connectors and hoses for signs of wear, leaks, or damage.
- Tank Condition: Examine the overall condition of the propane tank for any signs of rust, corrosion, or other damage that may compromise its integrity.
- Proper Fitting: Ensure that the tank is properly fitted to the forklift with no loose connections or fittings.
Safety Considerations During Forklift Operation
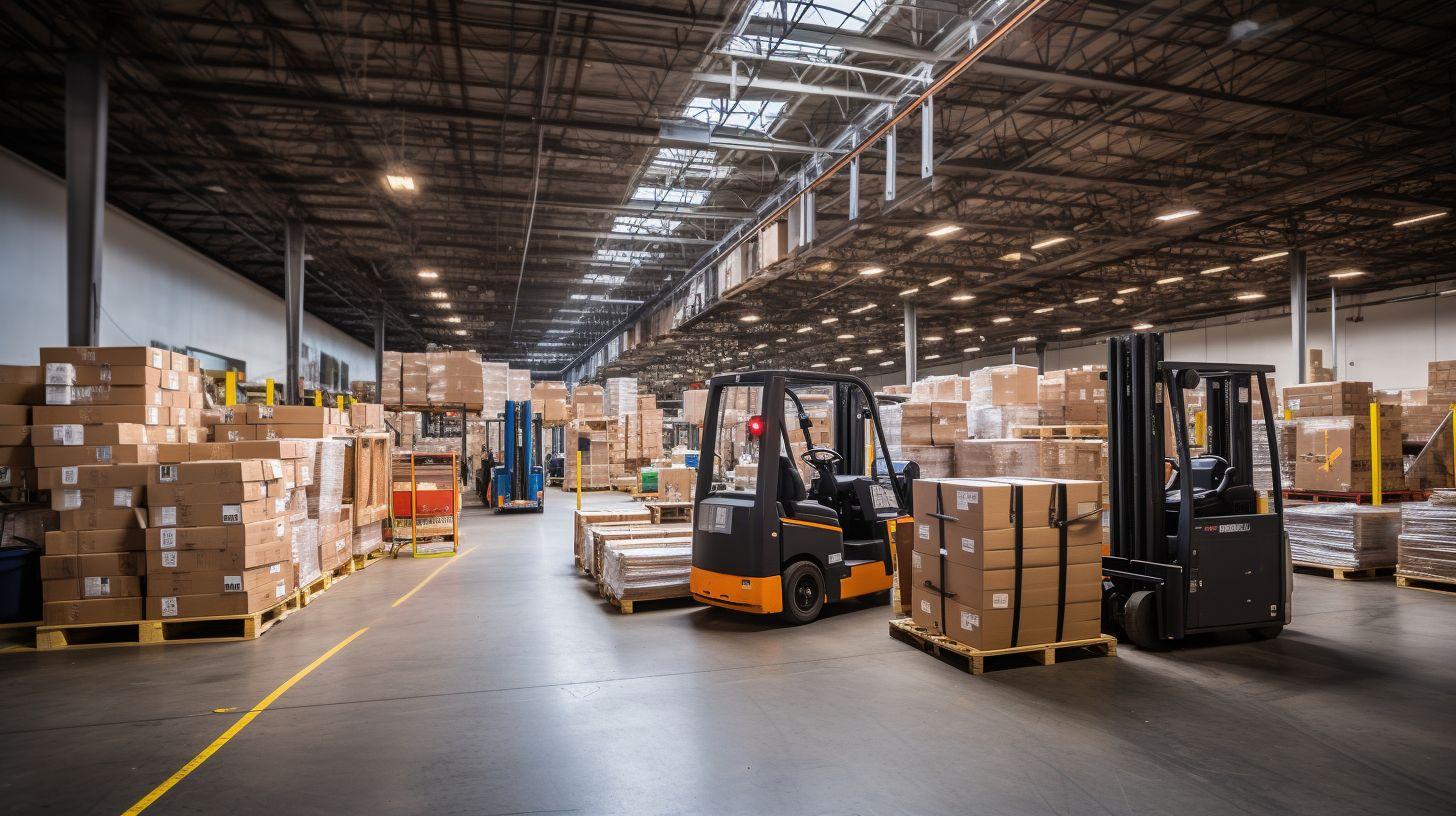
Ensure to always wear the seatbelt and keep all body parts within the confines of the forklift during operation. Operate at a safe speed, allowing ample time for braking and maneuvering.
Be vigilant of pedestrians and other equipment in the work area, using caution while turning and reversing. Avoid distractions that may affect your ability to operate the forklift safely, such as mobile phones or radios.
Regularly check that warning lights are functioning properly, indicating reverse gear or operational status. Keep an eye on hydraulic controls to ensure they are responsive and correctly manipulate loads.
Always observe load capacity limits and avoid overloading.
Inspect your surroundings before starting any task to ensure adequate visibility from the operator compartment. Conduct thorough inspections of operating controls before use, ensuring their proper functionality.
Finally, report any malfunctions or safety concerns immediately.
Long-Term Forklift Truck Maintenance Checks
Long-term forklift truck maintenance is crucial to ensure the continued safety and efficiency of the equipment. This section will discuss the various maintenance checks needed at different intervals to keep forklifts in top working condition.
Minor Maintenance (250 hours)
Perform minor maintenance checks every 250 hours of forklift operation to ensure safe and efficient functioning. This includes:
- Inspecting fluid levels to prevent potential leaks and ensure proper lubrication for the engine, transmission, hydraulic system, and coolant system.
- Checking for any leaks in the hydraulic system, oil seepage, fuel tank or lines, and coolant as per OSHA requirements to maintain a hazard-free environment.
- Assessing the condition of mast chains for any signs of wear or damage that may compromise lifting safety.
- Verifying tire conditions by inspecting for cuts, gouges, uneven wear patterns, or exposed cords to guarantee optimal traction and stability.
- Examining fork condition to identify any cracks, bends, or excessive wear on the forks that could affect load bearing capability.
- Ensuring the load backrest extension is secure and undamaged to provide protection against shifting loads during operation.
- Checking finger guards for damage to prevent potential harm from moving parts during operation.
- Verifying the presence and legibility of safety decals for visibility instructions and warnings required by OSHA guidelines.
- Confirming the availability of the operator’s manual in the designated storage area within reach of operators at all times.
- Testing functional safety devices such as lights, alarms, seat belts, horns,
Intermediate Maintenance (500 hours)
At 500 hours of forklift usage, the following maintenance tasks must be carried out to ensure optimal performance and safety:
- Inspect the engine cooling system, including hoses, belts, and radiator for any signs of wear or leaks. Replace or repair as necessary.
- Check the ignition timing and adjust if required to maintain efficient engine operation and fuel consumption.
- Examine the oil filter and replace it to prevent contaminants from circulating through the engine, which can lead to damage.
- Test the accelerator function to ensure smooth and responsive operation during use.
- Verify the condition of all valves and replace any that show signs of wear or malfunction to maintain proper fuel combustion.
- Inspect roll-over protection structures (ROPS) for any damage or deformation, ensuring they are capable of providing adequate protection in case of a tip-over incident.
Major Maintenance (2,000 hours)
At 2,000 hours of use, forklifts require major maintenance tasks to ensure their continued safe and efficient operation. These tasks include:
- Replacing coolant to maintain proper engine temperature regulation and prevent overheating.
- Changing the fuel strainer and water separator to ensure clean fuel supply and prevent engine damage.
- Replacing distribution belt and gasket seal to maintain proper engine performance and prevent leaks.
- Cleaning or replacing the interior ventilation filter for optimal air quality within the operator’s cabin.
- Replacing wheel bearing grease to minimize friction and wear on wheel bearings, ensuring smooth operation.
- Replacing transmission filter and oil to maintain proper lubrication and smooth gear shifting.
- Changing hydraulic oil to ensure proper hydraulic system function and prevent equipment failure.
- Changing brake fluid for reliable braking performance and overall safety.
How to Operate a Forklift Safely
Obtain OSHA-approved certification and understand the forklift type. Keep the forklift clean, be aware of the work area, and follow safety precautions to ensure safe operation.
Obtain OSHA-Approved Certification
To operate a forklift, it is essential to obtain OSHA-approved certification. This certification ensures compliance with safety standards and reduces the risk of accidents. Forklift operators must undergo training and complete daily inspections as mandated by OSHA to obtain this crucial certification.
Regular inspections help prevent potential hazards, maintain a safe work environment, and reduce the likelihood of injuries or damage.
Completing forklift inspection reports is necessary for obtaining OSHA-approved certification. These reports document that the pre-operational tasks and safety checks have been completed in accordance with OSHA regulations.
Understand the Forklift Type
Different types of forklifts, such as electric pallet jacks and internal combustion forklifts, have specific operational requirements. It’s important to obtain OSHA-approved certification and understand the particular type of forklift being operated before use.
This ensures that proper safety measures are taken into account and that the equipment is used in accordance with its individual specifications.
Knowing the specifics of a particular forklift type is crucial for maintaining a safe work environment. Keeping them clean, being aware of the work area, and understanding speed limits are all essential components of safe operation.
Keep the Forklifts Clean
Regular cleaning of forklifts is crucial to ensure safe and efficient operation. Clean the forklift daily to remove any debris, dirt, or other potential hazards. Use a soft brush or compressed air to clean out dust and debris from the engine compartment, radiator, and brakes.
Inspect the forklift for any signs of fluid leaks and promptly address any spills or drips. Regularly check the tires for wear and tear, as well as removing any buildup of mud or other substances that could affect traction.
Maintaining cleanliness extends beyond just the exterior; regularly inspect and clean filters, such as air filters, to prevent clogging which can impact engine performance. A clean forklift not only promotes safety but also helps identify potential maintenance issues before they become more significant problems.
Be Aware of the Work Area
After ensuring the forklifts are clean, it is crucial to be aware of the work area before operating them. Daily inspections should involve checking for any potential hazards or obstacles in the vicinity.
Additionally, operators must keep an eye out for changes in the work area, such as new obstacles or hazardous materials. It’s important to be mindful of other workers and pedestrians in the area to ensure their safety while operating a forklift.
Being aware of the clearance height and width of the work area is essential to avoid collisions or accidents. Furthermore, operators should pay attention to the type of surface they are operating on as different surfaces may require different techniques for safe forklift operation.
Conclusion
Performing a thorough daily forklift safety check is crucial to ensure safe operation. The responsibility for completing the inspection lies with the operator, in line with OSHA standards.
Specific inspections are required for various types of forklifts, such as electric, internal combustion, and liquid propane models. Employers must provide comprehensive checklists to comply with safety guidelines and reduce liability risks.
Regular inspections not only prevent accidents but also facilitate predictive maintenance and cost savings.
FAQs
1. Why do I need to inspect a forklift every day?
Daily forklift inspections are required to ensure safety and health at the workplace, as guided by OSHA (Occupational Safety and Health Administration).
2. What steps should I follow when doing a pre-use forklift check?
Before using a forklift, check the operator manual, look over all parts of the equipment including tires and controls, and make sure there’s no damage or hazards.
3. Can daily checks on a forklift help prevent accidents?
Yes! Daily checks can identify potential issues early which helps in preventing personal injury and unsafe working conditions around construction equipment like forklifts.
4. Should I wear any special gear when operating a forklift?
Always wear personal protective equipment as suggested in the health and safety guidelines to protect yourself from flames or other dangers while using a forklift.
5. What kind of maintenance should be performed regularly on a forklift?
Regular preventive maintenance, such as checking fluids like liquefied petroleum gas (LPG) levels or hydraulic pumps, is key to keeping your machine running smoothly.
6. Where can I find information about whistleblower protections if I report an unsafe situation with my company’s equipment?
Information about whistleblower protections under U.S Department of Labor’s Occupational Safety and Health Administration regulations can often be found within your workplace hazard communication resources or directly from OSHA.
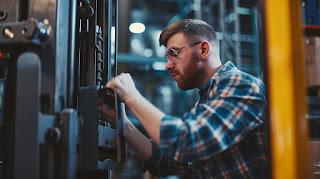
Keeping your forklift running smoothly can be a challenge. Planned maintenance is crucial, helping to avoid costly downtime and repairs. This guide will give you the tools and knowledge you need to keep your lift trucks in top shape, ensuring safety and efficiency on the job.
Dive in to discover maintenance made easy!
Key Takeaways
- Regular forklift maintenance enhances safety by preventing accidents and ensuring safety features are working properly. It also keeps the machine running smoothly, leading to increased productivity.
- Adhering to OSHA’s daily examination requirements and using their checklists can help identify maintenance issues early on, keeping the workplace safe and compliant with regulations.
- Preventive maintenance plans should include daily checks as well as non – driving and driving inspections, focusing on aspects like fluid levels, brakes, tires, batteries, and lights.
- Professional forklift maintenance services offer quality assurance and use of the right parts. They help preserve warranties while saving time that would be lost during equipment downtime.
- Performing DIY tasks such as replacing filters, checking fluid levels, inspecting batteries, monitoring tire condition can contribute significantly to a forklift’s longevity while reducing repair costs.
Importance of Forklift Maintenance
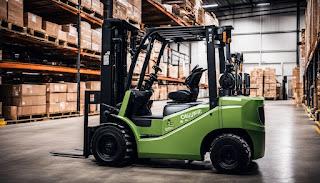
Forklift maintenance is crucial for enhancing safety, increasing productivity, and extending the service life of the equipment. It also helps in reducing costs associated with repairs and downtime.
Enhances Safety
Regular maintenance of forklifts is a key factor in preventing accidents and ensuring the safety of operators and other employees. By performing routine checks, potential hazards like leaks or brake issues can be identified and addressed before becoming dangerous.
Ensuring that seatbelts, warning lights, and other safety features are functioning properly also contributes to a safer environment.
Safety precautions go hand in hand with maintaining equipment reliability. Well-maintained forklifts operate more predictably, reducing the chances of unexpected malfunctions that could lead to injuries or property damage.
Moreover, adherence to OSHA’s stringent safety regulations through methodical forklift maintenance keeps workplaces compliant and workers protected from preventable mishaps.
Increases Productivity
Keeping your forklift well-maintained means it’s always ready to tackle the job at hand. Sudden breakdowns and prolonged downtime become rare, letting operators work efficiently without unexpected stops.
This steady stream of performance boosts a company’s output significantly. Equipment that receive routine maintenance run smoother and are less likely to suffer from the wear and tear that slows down operations.
Scheduling professional forklift maintenance services leads to quality repairs that also preserve important warranties. These experts handle issues before they escalate, which saves time by avoiding long repair sessions.
With everything in top condition, forklifts move materials quickly and safely through warehouses, allowing businesses to meet deadlines with ease and stay ahead in fast-paced markets.
Extends Service Life
Regular maintenance not only keeps forklifts running smoothly but also significantly extends their service life. Following the manufacturer’s recommended schedule ensures that each component gets the attention it needs before minor issues grow into major problems.
Preventative maintenance, such as checking fluid levels, inspecting tires and brakes, and changing the oil, helps avoid the wear and tear that can shorten a forklift’s lifespan. By taking care of these small tasks regularly, you can keep your forklift truck operational for years beyond what might be expected with less diligent care.
A well-maintained forklift does not suffer from frequent breakdowns that often indicate a machine is nearing the end of its useful life. Investing in consistent upkeep means internal components like valves, pumps, and bushings stay in working order longer.
This leads to reduced downtime due to repairs and ensures the vehicle remains reliable throughout its extended life cycle. With every completed checklist task or lubricant change—be it hydraulic oil or engine coolant—the potential service period of your heavy machinery increases, giving you more value from your investment over time.
Lower Costs
Keeping forklifts in top shape through preventive maintenance can slash your expenses significantly. It curbs the need for frequent repairs and reduces the risk of costly downtimes.
Well-maintained machines mean less money spent on replacing parts that wear out prematurely or fixing major issues that could have been avoided. This attention to routine care pays off by preserving the lifespan of your investment, ensuring you get the most value from every dollar.
Conducting proper operations also protects your bottom line. Training operators to handle forklifts with care, avoid overloading, and navigate ramps cautiously minimizes damage to equipment.
Less strain on components like engines and batteries leads to reduced fuel consumption or battery-charging costs over time, as well as fewer tire replacements due to decreased wear from heavy loads or improper maneuvering.
Smart handling coupled with diligent maintenance translates into significant savings and a healthier business valuation.
OSHA Requirements for Forklift Maintenance
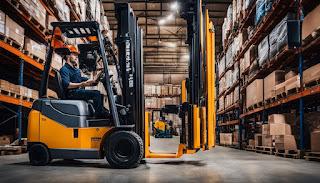
OSHA mandates daily examinations for industrial trucks to ensure immediate correction of any defects or unsafe conditions. Additionally, OSHA’s planned maintenance checklists can be utilized for training forklift operators and identifying essential maintenance issues.
Different planned maintenance checklists are designed for different types of forklifts, such as internal combustion engine or electric forklifts. Adhering to these requirements ensures compliance with OSHA regulations and helps in maintaining a safe working environment.
Thorough and regular inspections help identify patterns of wear, mitigate potential hazards over time, and ensure adherence to the set guidelines.
Maintaining comprehensive records assists in tracking the equipment’s condition over time while also ensuring compliance with OSHA requirements. These practices not only promote workplace safety but also contribute to avoiding unnecessary risks related to machinery operation and maintenance.
Creating a Preventive Maintenance Plan
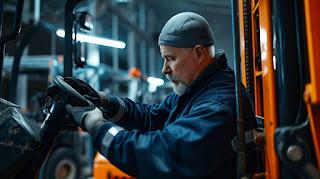
Developing a preventive maintenance plan for your forklift is essential to ensure that it remains in optimal condition. This includes daily, non-driving, driving, and forklift-specific checklists to catch potential issues before they become major problems.
Daily Maintenance Checklists
- Conduct a visual inspection of the forklift for any leaks, damages, or signs of wear and tear.
- Check the fluid levels, including engine oil, hydraulic fluid, coolant, and brake fluid, and top them up if necessary.
- Inspect the tires for any damage, wear, or proper inflation levels according to the manufacturer’s recommendations.
- Test all safety features such as lights, alarms, horns, and seatbelts to ensure they are functioning correctly.
- Examine the battery for corrosion and ensure it is securely connected with no visible damage to the cables.
- Test the brakes by engaging them in a safe environment to ensure they are responsive and not making unusual noises.
- Clean the forklift both inside and out to maintain proper hygiene and prevent debris from affecting its performance.
Non-Driving Maintenance Checklists
Perform these maintenance checks regularly to ensure the proper functioning of your forklift:
- Inspect the brakes for wear and tear, including brake pads and hydraulic systems. Replace any worn – out components promptly to maintain braking efficiency.
- Check the hydraulics for leaks or damage, assessing the condition of hoses, seals, and cylinders. Address any issues immediately to prevent potential breakdowns.
- Examine the lift chains or forks for signs of wear, such as stretching or cracks. Ensure they are properly lubricated and free from any obstructions that could affect their performance.
- Test the lights, horn, and other safety features to ensure they are functioning correctly. Replace any faulty bulbs or repair damaged wiring to maintain visibility and compliance with safety regulations.
- Monitor the overall condition of the forklift’s body, ensuring there are no dents, cracks, or other structural damage that could compromise its stability and safety during operations.
- Verify the functionality of the cooling system by checking coolant levels and inspecting for any leaks or blockages in the radiator, hoses, and connections.
Forklift-Specific Maintenance Checklists
Forklift-specific maintenance checklists are crucial for ensuring the proper upkeep of different types of forklifts, as each type has unique maintenance requirements.
- Electric Forklifts:
- Regularly inspect and maintain the battery, including checking water levels and cleaning terminals to ensure optimal performance and longevity.
- Conduct thorough checks on the electrical system, including wiring, connections, and controls to prevent malfunctions and ensure safe operation.
- Diesel Forklifts:
- Regularly inspect the engine components such as air filters, fuel filters, and oil levels to maintain efficient performance and prevent breakdowns.
- Ensure proper maintenance of the exhaust system to minimize emissions and comply with environmental regulations.
- Propane Forklifts:
- Verify the condition of fuel lines, connectors, and tanks regularly to prevent leaks or malfunctions that could pose safety hazards.
- Inspect the cooling system, including coolant levels and radiator condition, to avoid overheating issues that can affect performance.
- Pneumatic Tire Forklifts:
- Check pneumatic tires regularly for wear, damage, or low pressure to maintain stability and traction.
- Inspect the hydraulic system for leaks or malfunctions to ensure smooth lifting operations without safety risks.
- Warehouse-Use Forklifts:
- Inspect load handling attachments such as forks and clamps for wear or damage that could compromise load stability or operator safety.
- Regularly check mast components for proper lubrication and alignment to ensure smooth vertical movement when handling loads.
- Rough Terrain Forklifts:
- Periodically inspect the undercarriage components, including axles, drive train, and suspension systems for signs of wear or damage due to rugged operating conditions.
- Ensure regular inspection of additional safety features specific to rough terrain forklifts such as roll-over protection structures (ROPS) for compliance.
Driving Maintenance Checklists
To ensure the proper upkeep of forklifts, regular driving maintenance checklists are essential. Regular checks help in identifying and addressing potential issues before they escalate. Here is a comprehensive list of driving maintenance tasks:
- Inspect the tires for wear and tear, ensuring proper inflation levels to maintain stability and maneuverability.
- Check the brakes to ensure they are functioning effectively, reducing the risk of accidents and damage to goods.
- Examine the steering system to guarantee smooth operation and precise control during usage.
- Test the accelerator and engine – off functions to ensure efficient performance while minimizing fuel consumption.
- Verify that all lights, including headlights, taillights, and indicators, are operational for enhanced safety in dimly lit areas.
- Assess the fluid levels, such as oil, hydraulic fluid, and coolant, to prevent mechanical issues and overheating.
Common Forklift Maintenance Repairs
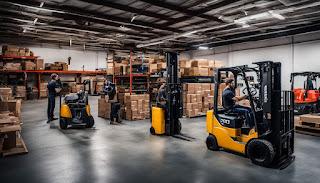
From mast problems to steering and starting issues, forklifts can face a range of common maintenance repairs that need attention. Want to know more about how to tackle these issues? Keep reading for the ultimate guide to forklift maintenance.
Mast Problems
Mast problems affect a forklift’s lifting and lowering capabilities. These issues can lead to reduced productivity and increased downtime if not addressed promptly. It is crucial to regularly inspect the mast system as part of a comprehensive maintenance plan to ensure optimal performance and safety.
When mast problems arise, it is essential to take immediate action to prevent further damage or potential accidents. Regular inspection and timely repairs can help avoid costly disruptions in operations and maintain a safe working environment.
Steering Problems
Strange noises while turning and difficulty in steering may indicate potential steering problems with a forklift. These issues can be caused by worn-out pressure valves, gears, or misaligned tires.
If left unaddressed, steering problems can lead to safety hazards and decrease productivity.
By addressing steering problems promptly, you can ensure the safety of your operators and extend the service life of your forklifts. Regular maintenance checks should include inspecting the steering system for any signs of wear or misalignment to prevent more severe issues from developing.
Starting Problems
After addressing steering problems, it’s essential to consider starting problems for efficient forklift maintenance. To tackle starting issues, checking the battery charging level is crucial.
Regular monitoring and ensuring the appropriate charge are fundamental in preventing these common maintenance concerns. Moreover, prompt attention to any irregularities in battery power can significantly reduce downtime and improve overall productivity.
Starting problems on electric forklifts often stem from insufficient or improper battery charging. By actively managing this aspect of maintenance, operators can proactively address potential starting issues before they escalate into larger repair needs.
DIY Forklift Maintenance Tasks
Regular maintenance tasks for forklifts are vital to ensure their proper functioning and longevity. Here’s a list of DIY maintenance tasks that can help keep your forklift in top condition:
- Filter Replacements: Regularly replace air, fuel, and oil filters as part of your maintenance routine to ensure the engine runs smoothly and efficiently.
- Fluid Top-offs: Check and top off all necessary fluids, including engine oil, transmission fluid, coolant, and hydraulic fluid, to prevent potential damage.
- Quick Inspections: Conduct routine visual inspections of the forklift for any signs of wear and tear, leaks, or loose components that may affect its performance.
- Battery Checks: Inspect the battery terminals, electrolyte levels, and overall battery condition to ensure it is functioning optimally and avoid unexpected downtime.
- Tire Changes: Regularly monitor tire tread wear and replace tires when necessary to maintain traction and stability while operating the forklift.
- Tire Damage Monitoring: Keep an eye out for any punctures, cuts, or other damage to the tires that may compromise safety or performance on different surfaces.
Benefits of Professional Forklift Maintenance Services
Professional forklift maintenance services provide quality assurance and the use of the right parts, preserving the warranty and saving time for your business. Learn more about how these services can benefit your fleet management and overall productivity.
Quality Assurance
Quality assurance in forklift maintenance is crucial to ensure that the equipment operates safely and efficiently. Regular maintenance checks contribute to identifying potential issues early, minimizing the risk of unexpected breakdowns that may compromise safety and productivity.
By adhering to quality standards, such as OSHA requirements and manufacturer guidelines, businesses can uphold a safe working environment while maximizing the lifespan of their forklift fleet.
Thorough documentation of maintenance activities not only helps track compliance with regulatory standards but also provides valuable insights into long-term wear patterns and overall upkeep costs.
Right Parts
Using professional forklift maintenance services ensures that you get the right parts for repairs and replacements, which is crucial for keeping your equipment running smoothly. By using genuine parts, you can be confident in the quality and compatibility with your specific forklift model, reducing the risk of future issues.
Additionally, proper maintenance helps in preserving warranties on forklift parts, providing added financial protection and peace of mind. Planned maintenance allows scheduling servicing appointments using the right parts during convenient times for operations.
This proactive approach minimizes downtime while maximizing efficiency.
Warranty Preservation
Preserving the warranty of your forklift is crucial for avoiding unexpected repair costs. Professional maintenance services help ensure that any warranty claims are not compromised due to neglect or improper handling.
Regular upkeep and adherence to manufacturer’s recommendations can go a long way in safeguarding the warranty of your valuable equipment.
Using licensed technicians and genuine parts for repairs also contributes to upholding the warranty conditions. Additionally, keeping detailed records of all maintenance activities and adhering to OSHA requirements further support warranty preservation efforts.
Time Saving
Moving from warranty preservation to time-saving, it’s clear that efficient forklift maintenance not only safeguards your investment but also optimizes operational productivity. By strategically scheduling servicing appointments during non-peak hours, businesses can minimize downtime and save valuable time.
Adhering to a regular maintenance plan prevents emergency interruptions and unplanned expenses, ensuring consistent workflow without unnecessary delays.
Conclusion
In conclusion, regular forklift maintenance is crucial for workplace safety and productivity. This comprehensive guide highlights the importance of planned maintenance, OSHA requirements, creating a preventive maintenance plan, common repairs, DIY tasks, and the benefits of professional services.
By implementing these strategies, businesses can ensure smooth operations and maximize the lifespan of their fleet while minimizing costs in the long run.
FAQs
1. Why is forklift maintenance important?
Forklift maintenance is key to keeping these vehicles running safely and efficiently; it can help prevent accidents, reduce maintenance costs, and ensure compliance with the Occupational Safety and Health Administration (OSHA) standards.
2. What are some common forklift parts that need regular checks?
You should regularly check your forklift’s power steering, clutch, fuel economy aspects, internal-combustion engine components if applicable, and bearings as part of ongoing maintenance to avoid breakdowns.
3. How does proper maintenance affect a forklift’s return on investment (ROI)?
Maintaining your forklift will lower repair costs over time and keep it in operation longer without issues, which enhances the overall return on investments by prolonging the vehicle’s life span.
4. What safety gear do I need when performing forklift repairs?
Always use personal protective equipment (PPE), such as gloves and goggles when doing repairs or maintenance work to adhere to occupational health and safety guidelines.

Operating a forklift comes with its risks. Each year, OSHA reports around 35,000 serious accidents involving forklifts. This article offers essential tips and practices to keep you safe while handling a forklift.
Stay safe; read on.
Key Takeaways
- Getting certified and understanding your forklift are the first steps to safety. You learn how to avoid accidents and what your machine can handle.
- Always wear safety shoes, hard hats, and high – visibility clothing when operating a forklift. These protect you from injuries if things go wrong.
- Know your forklift’s load limit. Overloading can cause serious accidents like tipping over.
- Check your forklift every day for any problems with brakes, steering, or warning devices. This keeps it running safely.
- Keep an eye on everything around you while driving a forklift. Make sure you see people walking by and avoid any obstacles in your way.
Understanding Forklift Safety
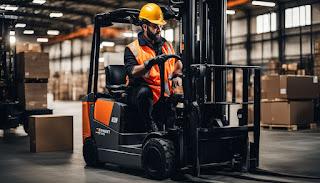
Forklift safety is all about knowing how to avoid accidents and injuries. Every year, OSHA reports nearly 35,000 serious forklift incidents, including 85 that end in death. This shows just how critical it is to understand these machines inside out.
Knowing your forklift’s limits and abilities can make the difference between a normal day at work and a catastrophic event.
To stay safe, operators must get proper training and certification. This isn’t just a one-time deal — employers should check on their employees’ skills every three years to make sure they’re still sharp.
Also, wearing the right gear like hard hats, safety shoes, and high-visibility vests is non-negotiable when you’re behind the wheel of a lift truck. You can’t overlook any part of this: from how much weight your forklift can handle to making sure it’s inspected daily for any signs of trouble.
Essential Safety Tips for Forklift Operation
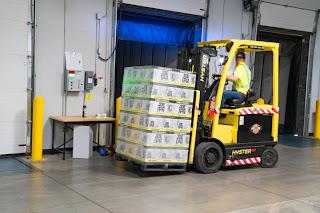
Obtain forklift certification to ensure proper training. Always wear appropriate safety attire while operating a forklift.
Attaining Forklift Certification
Getting a forklift certification is a must for anyone looking to operate lift trucks safely and legally. Through training, individuals learn how to avoid accidents and handle materials properly.
Courses often cover topics like occupational health and safety, load capacity, and the correct use of personal protective equipment (PPE). The Occupational Health and Safety Administration (OSHA) requires this certification because it proves that operators understand crucial safety procedures.
Online Forklift Certification programs make learning convenient. They offer comprehensive lessons on everything from manual handling to avoiding physical hazards in the workplace. After completing these courses, operators must pass an exam to get their license.
This process ensures that only qualified personnel are behind the controls of a forklift, helping to minimize risks of injuries and improve workplace safety. Regular evaluations every three years help keep skills sharp and up-to-date.
Wearing Appropriate Safety Attire
After getting certified, focus on wearing the right safety gear for maximum protection. Operators must have safety shoes, hard hats, and high-visibility clothing every time they operate a forklift.
These items shield them from severe injuries if an incident occurs. High-visibility clothing makes sure other workers can easily see the operator, reducing the chance of collisions.
Hard hats protect against head injuries from falling objects or bumps against surfaces. Safety shoes with steel caps guard feet against heavy loads that might fall off a pallet during material handling.
Always fasten seat belts before driving to stay secure in your seat, minimizing risks in case of sudden stops or turns.
Adhere to Load Capacity Guidelines
Forklift operators must know their machine’s load capacity. This knowledge keeps everyone safe on the job. Pushing a forklift beyond its limit risks tip-overs and serious accidents.
Always check the load capacity before lifting. This prevents damage to goods and protects workers.
Next, conduct regular and thorough inspections of your forklift.
Regular and Thorough Forklift Inspections
Regular and thorough forklift inspections are crucial to ensure safe operation. Daily checks should be conducted to assess brakes, steering, controls, warning devices, tires, horn, lights, and backup alarms.
Additionally, employers should organize periodic comprehensive examinations to identify any potential issues that could compromise the safety of the equipment.
Inspecting a forklift ensures proper functioning in accordance with OSHA regulations. Routine assessments also help prevent accidents and maintain a safe working environment.
Ensuring Load Stability and Security
To maintain load stability and security, operators should always adhere to the forklift’s load capacity guidelines. Understanding the weight limit helps prevent tilting or tipping accidents, ensuring a secure working environment.
Utilizing proper lifting attachments when handling irregularly-shaped or oversized loads is crucial for maintaining load stability.
Inspecting pallets, containers, and securing straps before transporting goods on the forklift guarantees that items remain stable throughout the operation. Forklift operators can reduce the risk of hazards by utilizing these safety measures while handling and transferring loads.
Maintaining Awareness of Surroundings
Forklift operators must constantly remain alert to their surroundings, watching for pedestrian traffic and being mindful of blind spots. This includes regularly checking for any obstacles or potential hazards in their path as they navigate through the workspace.
In addition, proper lighting in the facility is crucial for maintaining clear visibility and minimizing accidents caused by poor illumination.
Now let’s focus on examining “Common Mistakes by Forklift Operators” to ensure a safer working environment overall.
Common Mistakes by Forklift Operators
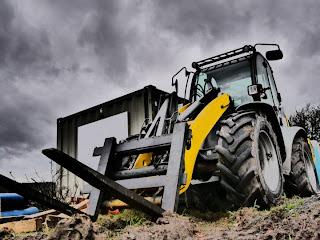
- Operating a forklift without proper certification can lead to serious accidents and is a violation of OSHA regulations.
- Failure to wear appropriate safety attire, such as steel-capped boots and protective eyewear, puts operators at risk of injuries from falling objects and collisions.
- Ignoring load capacity guidelines can lead to the destabilization of the forklift, increasing the likelihood of tipping over and causing severe injuries to the operator and others nearby.
- Neglecting routine inspections of the forklift can result in overlooked mechanical issues that may lead to malfunctions while in operation, posing a danger to both the operator and other individuals in the vicinity.
Importance of Safety Measures for Employers and Operators
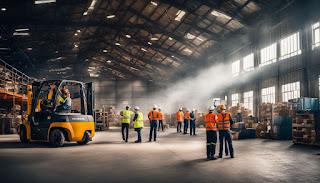
Employers and operators must prioritize safety to mitigate the risk of accidents. Proper training, certification, and regular inspections are crucial for creating a secure environment.
Emphasizing load capacity guidelines, maintaining awareness of surroundings, and ensuring stable loads are vital elements in preventing mishaps. Additionally, implementing safety protocols such as designated refueling areas and floor marking systems can significantly enhance workplace safety.
Employers should also provide ongoing safety training to raise awareness about musculoskeletal injuries, fire hazards, pedestrian safety, and ergonomic practices.
Creating a culture of safety not only safeguards employees but also minimizes operational downtime due to accidents or injuries. Regular toolbox talks help reinforce the importance of adhering to speed limits and lockout tagout procedures.
Furthermore, employers should consider investing in comprehensive insurance coverage tailored to forklift operations to ensure effective risk management.
Conclusion
Forklift safety is crucial for preventing accidents. Operators must be certified and wear proper attire. Regular inspections and load stability awareness are key. Employers play a vital role in ensuring safety measures are in place.
It’s everyone’s responsibility to prioritize forklift safety.
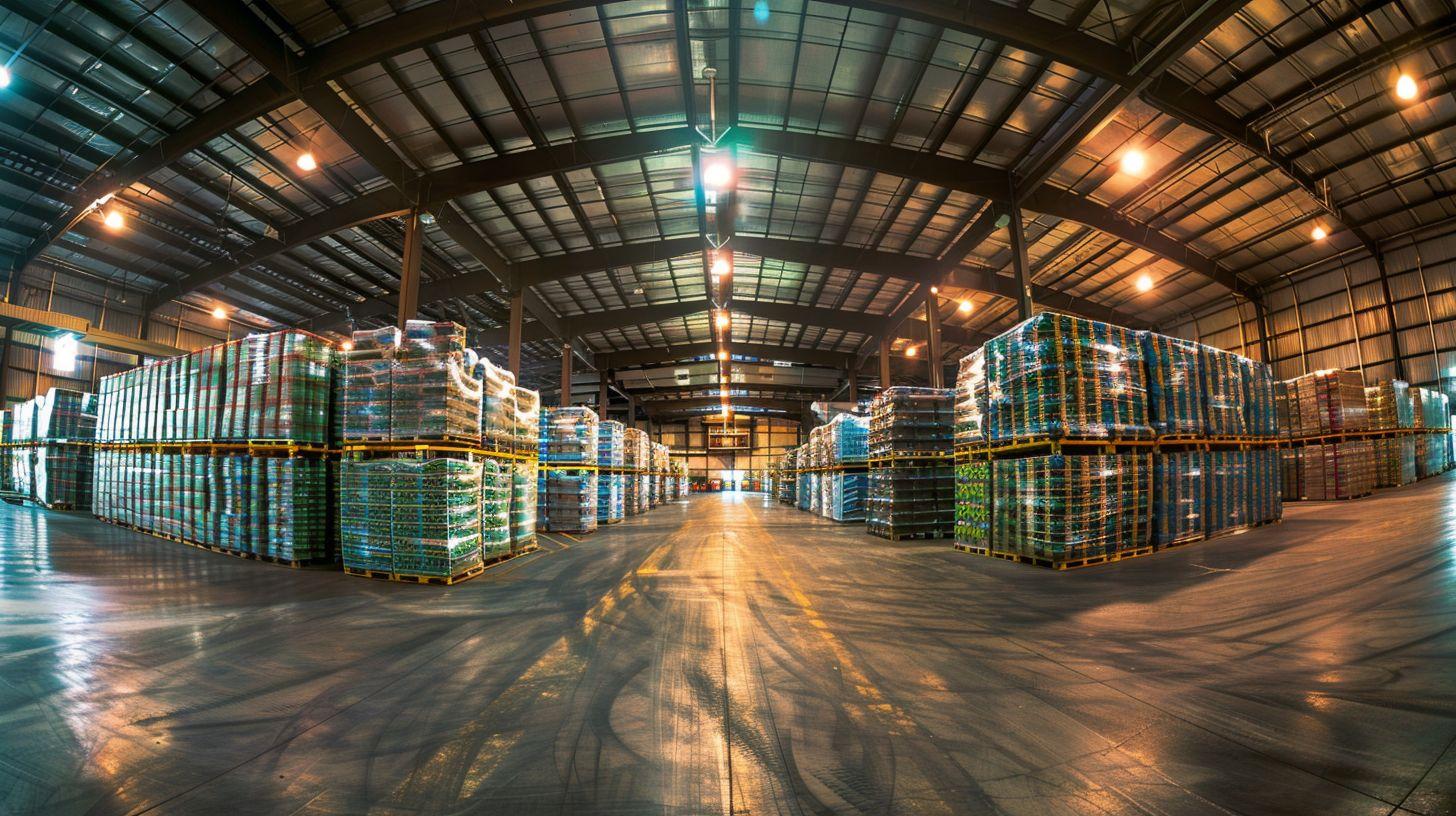
Finding the right job can be tough. High-paying jobs for forklift operators are out there in 2024. This article will guide you to where these jobs are and which companies pay the most.
Keep reading to boost your career!
Key Takeaways
- In 2024, Skidder Operators and Stacker Operators are among the highest-paid forklift jobs, earning up to $57,500 and $45,000 a year, respectively.
- Getting certified as a Forklift Operator can increase your salary potential with Certified Operators earning between $34,000 and $42,000 annually.
- Wisconsin is the top state for forklift drivers in 2024 offering median salaries of $36,688 while companies like DeWitt LLP Law Firm and BD rank among the highest paying employers.
High Paying Forklift Jobs in 2024

In 2024, forklift jobs like Skidder Operator and Warehouse Operator are among the highest paying in the industry. Certified Forklift Operator and General Labor Forklift Operator roles also offer competitive salaries.
Skidder Operator
Skidder operators have a key role in safely removing trees from forests. They earn between $52,500 and $57,500 a year for their work. These professionals use skidder accessories to move trees where they need to go.
This job is about strength, safety, and skill with heavy machinery.
The next position on our list of high-paying jobs for forklift operators in 2024 is the stacker operator job.
Stacker Operator
Stacker operators work in busy environments where they move and stack goods with precision. They earn between $37,500 and $45,000 a year. This job requires them to operate heavy equipment safely.
Stacker operators get paid very well for their skills.
Their salary does not change much with more experience. All stacker operators, no matter how long they have worked, make about the same amount of money. They play a key role in keeping warehouses organized and efficient.
Certified Forklift Operator
Certified forklift operators earn between $34,000 and $42,000 a year. They play a crucial role in supply chain management by ensuring goods are moved safely and efficiently. Getting a forklift certification can boost your chances of landing high-paying jobs.
Companies value certified operators because they minimize the risk of workplace accidents, proving that investing in certification pays off.
Next on the list is the lift operator position, which also offers competitive salaries and opportunities for growth within various industries.
Lift Operator
After talking about certified forklift operators, we shift our focus to another high-paying role: the lift operator. This job is crucial in keeping warehouses and construction sites running smoothly.
Lift operators handle different types of lifting equipment, not just forklifts. They play a key role in moving goods safely and efficiently.
Lift operators need proper training and certifications such as OSHA Forklift Certification. These qualifications help them land jobs at top companies like DHL Supply Chain. Working as a lift operator can lead to great pay, especially when you’re skilled and certified.
Warehouse Operator
A warehouse operator’s salary ranges from $33,500 to $40,500 per year. They are responsible for processing orders, managing inventory, and operating heavy equipment like forklifts.
Most jobs require a high school degree or GED certificate, prior warehouse experience, mechanical skills, a clean driving record, and in some cases, a special operator’s license.
General Labor Forklift Operator
The general labor forklift operator earns a salary range of $33,000 to $40,500 per year. With the highest-paying states being Wisconsin, Minnesota, and North Dakota. The top companies for forklift operators in 2024 include DHL Supply Chain and Walmart.
Zippia offers helpful tools such as Chrome extensions and customizable resume templates tailored towards forklift drivers.
Forklift Operator
Forklift operators handle material handling equipment to transport goods in warehouses and distribution centers. Certification and experience are vital for the job, which requires precision and attention to safety protocols.
Demand is high across the United States, with Wisconsin offering the highest median salary for forklift drivers at $36,688. The top companies hiring include DHL Supply Chain, Walmart, DeWitt LLP Law Firm, BD, Exel Inc., and ManpowerGroup.
Zippia provides tools like a Chrome extension for job applications and customizable resume templates tailored towards forklift operator positions.
Clamp Truck Driver
A Clamp Truck Driver earns a yearly salary between $33,500 and $40,000. Their main duty is handling heavy objects within a warehouse using specialized clamp trucks. These drivers play a crucial role in the logistics network of various companies, ensuring efficient movement and safe positioning of goods.
With the demand for skilled forklift operators on the rise, acquiring an online forklift certification can unlock opportunities to secure these high-paying jobs.
Top 10 States for Forklift Operators in 2024
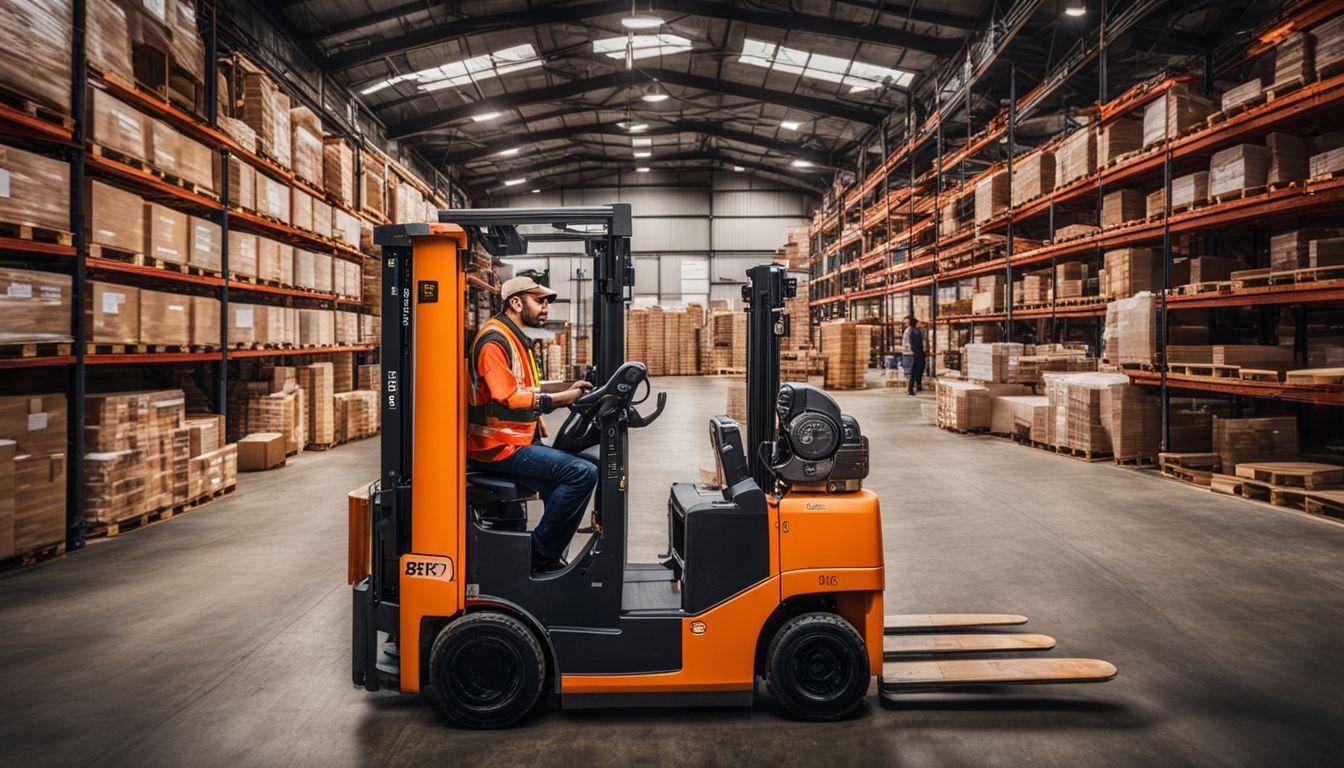
Forklift operators can find lucrative opportunities in various states, such as Wisconsin and Minnesota. These states offer promising prospects for career growth in the forklift operation sector.
Wisconsin
Wisconsin tops the list as the best state for forklift drivers, offering a median salary of $36,688. Fairbanks is the city in Wisconsin that provides the highest pay for forklift drivers.
This makes Wisconsin an ideal location for those seeking high-paying opportunities within this field.
The Forklift Academy and Walmart are known to be significant players in providing employment opportunities for forklift operators in Wisconsin. With its diverse economy and growing job market, Wisconsin offers favorable conditions for seeking substantial career growth and stability within this industry.
Minnesota
Minnesota ranks as the second best state for forklift drivers in 2024, with a median salary and job count provided. It is among the top 10 best states for forklift drivers, with details about the average annual salary and location quotient.
Minnesota is one of the highest paying states for forklift operator jobs, offering competitive salaries and numerous job opportunities within this field.
North Dakota
North Dakota ranks third for forklift drivers in 2024, boasting 73 jobs with an average annual salary of $42,539. The state offers a solid job market for forklift operators, with many companies hiring across the region.
North Dakota stands among the top five states offering lucrative opportunities for forklift drivers this year.
Alaska
Alaska ranks fourth for forklift drivers in 2024, with an average annual salary of $39,870 and 350 available jobs. Fairbanks is one of the highest-paying cities for forklift operators.
The job market in Alaska is active, offering several opportunities as companies are hiring across various positions.
Massachusetts
In 2024, Massachusetts secures its place as the 5th best state for forklift drivers. The average annual salary here is competitive, and the job market offers favorable opportunities with many actively hiring companies.
The state’s industry concentration for forklift driver jobs exceeds the national average, underlining a strong demand in this sector. Alongside other high-paying states like Wisconsin, Minnesota, and North Dakota, Massachusetts makes it to the top 10 states list for forklift drivers.
Now let’s explore the highest paying companies that offer opportunities for forklift operators in 2024.
Ohio
Ohio ranks as the 6th best state for forklift operators in 2024, offering a median salary that places it within the top 10 highest paying states. The active job market in Ohio provides numerous opportunities for forklift operator positions across the state.
With its competitive salaries and a significant number of job openings, Ohio emerges as one of the top states with favorable prospects for professionals in this field.
South Dakota
South Dakota ranks 7th for highest paying forklift operator jobs in 2024. The average annual salary for forklift drivers in South Dakota is competitive, and the state offers numerous job opportunities.
Zippia provides recent job postings and salary information, positioning South Dakota as a favorable location for forklift operators.
Montana
Montana, one of the top 10 states for forklift drivers in 2024, offers appealing opportunities. The state boasts a rising demand for skilled operators and provides an average annual salary that is competitive.
Montana’s location quotient within the forklift driver industry indicates a noteworthy presence and steady employment prospects. Furthermore, Zippia extends support to Montana-based workers by offering customizable resume templates and expert advice tailored towards enhancing their careers.
In conclusion, let’s delve into the promising landscape of opportunities for forklift operators in Montana.
Oregon
Oregon ranks as one of the top 10 states for forklift drivers in 2024, with a median salary of $36,162. It has a total of 7,220 forklift driver jobs with an average annual salary of $38,110.
The lowest 10 percent earn about $30,400 and the highest earners take home around $48,000. Oregon’s location quotient for forklift drivers is at 0.7, indicating a relatively high concentration of these jobs compared to the national average.
This makes Oregon an attractive state for skilled forklift operators looking to secure well-paying employment opportunities in this sector based on job availability and competitive salaries.
Nevada
Nevada ranks among the top 10 best states for forklift operators in 2024. Zippia’s research indicates an active job market with numerous opportunities across the state. The average annual salary, lowest 10 percent earned, highest 10 percent earned, and location quotient data is provided to help understand the prospects for forklift drivers in Nevada.
The information shows that there are significant employment possibilities and a favorable environment for those seeking work as forklift operators in Nevada.
Highest Paying Companies for Forklift Operators in 2024
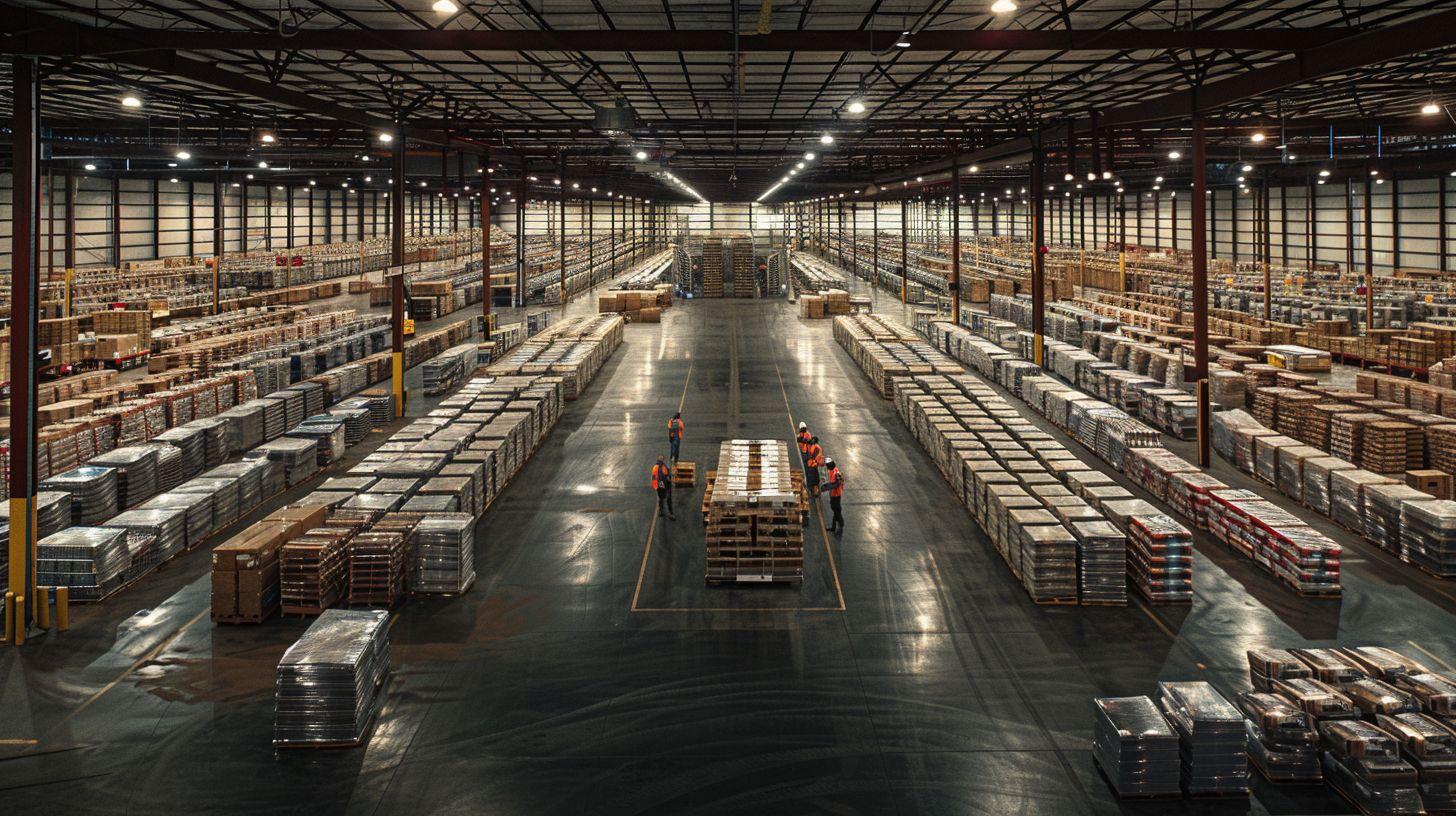
These companies offer the highest pay for forklift operators in 2024. To explore more, Keep on reading as we dive into these companies!
DeWitt LLP Law Firm
DeWitt LLP Law Firm ranks among the highest paying companies for forklift operators in 2024. The median salary for a forklift operator at DeWitt LLP Law Firm is $47,352, making it an attractive option.
This places DeWitt LLP at the top, with an average salary of $47,352 for forklift operators.
BD
BD, a medical technology company focused on improving drug delivery and healthcare solutions, is among the highest paying companies for forklift operators. The average salary at BD for forklift operators stands at $46,866, showcasing the company’s dedication to providing competitive compensation.
Additionally, BD offers opportunities to work in a dynamic and innovative environment with a focus on employee satisfaction and quality healthcare solutions. This positions BD as an employer of choice within the realm of high-paying companies for forklift operators in 2024.
Nabors Industries
Nabors Industries, an American global oil and gas drilling contractor, offers forklift operators an average salary of $45,758 in 2024. It stands as one of the highest paying companies for forklift operators in the US this year.
Ventura Foods
Ventura Foods, a top producer of custom dressings and sauces, offers an average forklift operator salary of $44,670. It stands among the highest paying companies for forklift operators in the US in 2024.
The information is updated as of October 6, 2023.
The average annual salary at Ventura Foods is $44,670 which positions it among the highest-paying companies for forklift operators in 2024.
Kemps
Kemps, an American dairy company, offers an average forklift operator salary of $43,764. This places Kemps among the top paying companies for forklift operators in 2024. The information about Kemps is up to date as of October 6, 2023.
Schnitzer Steel
Schnitzer Steel leads the global market in recycled steel collection and sales. The average salary for forklift operators at Schnitzer Steel ranges from $43,370 to $43,527 annually, making it one of the top-paying companies for this role in the US in 2024.
With a focus on recycling, Schnitzer Steel offers lucrative opportunities for individuals seeking high-paying forklift operator jobs.
Teleflex
Teleflex, a company dedicated to medical technology, offers attractive salaries for forklift operators. The average salary at Teleflex ranges from $43,370 to $43,527 yearly. Zippia provides tailored resume templates for those interested in positions at Teleflex.
These facts highlight the competitive pay scale and employee dedication associated with Teleflex.
Dairy Farmers of America
Dairy Farmers of America stands out as one of the best-paying companies for forklift operators in 2024, offering an average annual salary ranging from $43,370 to $43,527. The organization is closely linked with the dairy industry and provides lucrative opportunities for skilled forklift operators.
Dairy Farmers of America is renowned for its commitment to providing high-quality jobs within the dairy sector and has positioned itself as a favorable employer for forklift operators seeking stability and competitive compensation.
Seneca Foods
Seneca Foods is a top-paying employer for forklift operators in the US, offering an annual salary ranging from $43,370 to $43,527. The company focuses on packaging and processing various fruits and vegetables while providing equal employment opportunities.
Seneca Foods supports economic growth through its warehousing and low carbon practices. At Seneca Foods, employees experience a supportive work environment and diverse opportunities within the realm of logistics services.
Darigold
Darigold, a prominent dairy product manufacturer, stands out as one of the highest paying companies for forklift operators in the US in 2024. The average annual salary for forklift operators at Darigold ranges from $43,370 to $43,527.
Known for its commitment to employee welfare and dedication, Darigold offers competitive compensation to its workforce.
With a focus on simplicity and clarity, Darigold has carved a niche as a leading producer of dairy goods while ensuring fair remuneration for its employees.
Conclusion
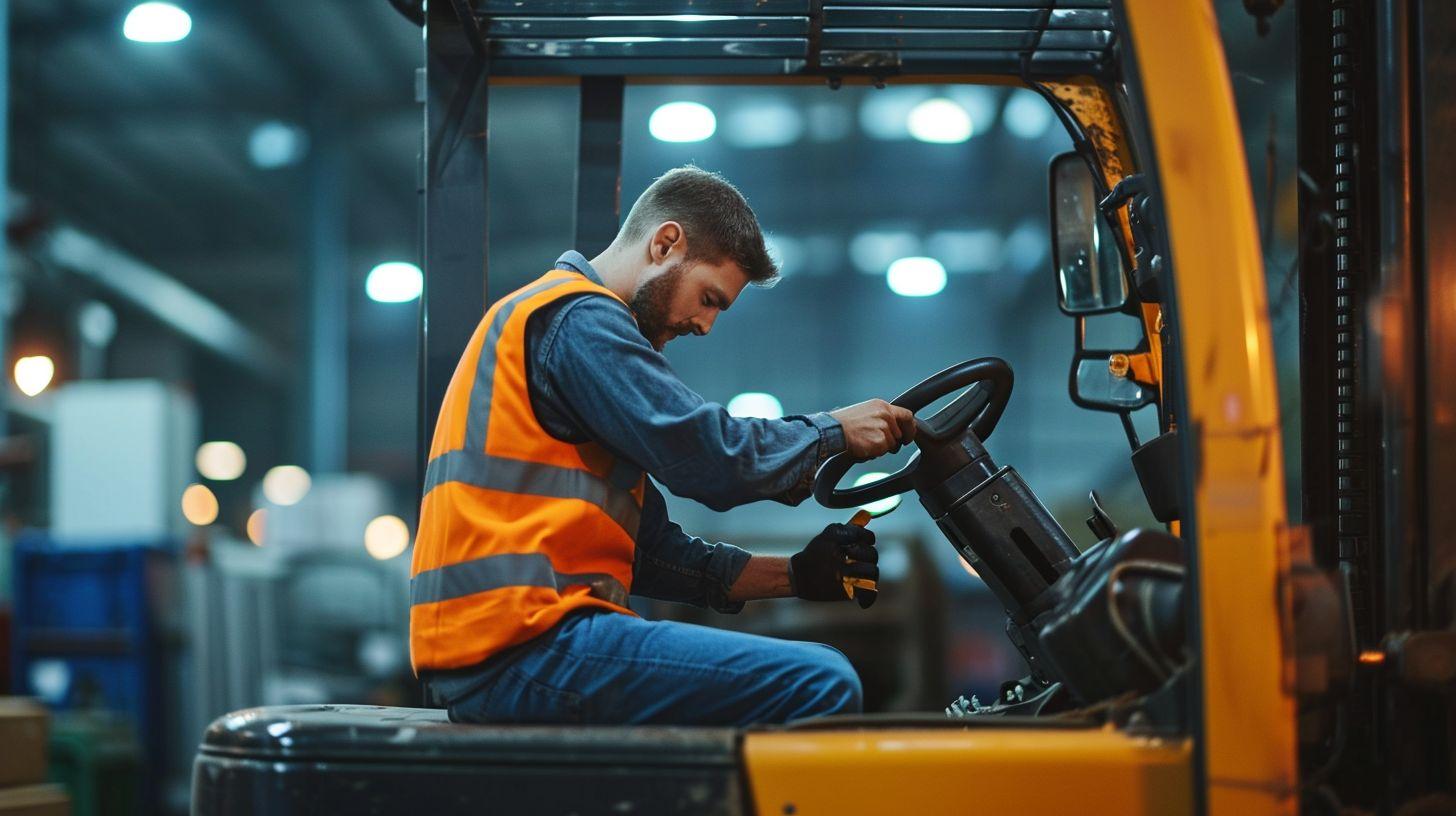
Forklift operator jobs in 2024 offer high pay in industries like logging, warehousing, and cargo handling. Experience and certification are crucial for these roles. The job market is active across the United States, with Wisconsin being the top state for forklift drivers.
Zippia provides tools to track job applications and customizable resume templates. Top companies hiring forklift operators include DHL Supply Chain, Walmart, DeWitt LLP Law Firm, and BD.
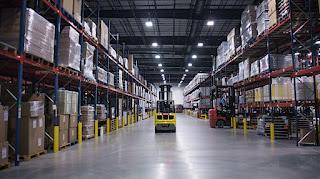
Having trouble mastering forklift operations can slow down work in warehouses and construction sites. Forklift operators need a unique set of skills to work efficiently and safely.
This article will outline five crucial skills every forklift operator should learn to improve their job performance. Keep reading to discover how you can become a top-notch forklift operator.
Key Takeaways
- Forklift operators need to be very careful and pay attention to every detail. This means watching the load, knowing where they are going, and seeing any dangers.
- It’s important for them to work well with their hands and eyes together. They have to drive through tight spots without hitting anything or anyone.
- Being able to manage time helps them do more work in less time without rushing and making mistakes.
- Good talking skills help operators stay safe by making sure everyone knows what is happening around the forklifts.
- Solving problems quickly keeps the job moving smoothly when unexpected things happen.
Understanding the Role of a Forklift Operator
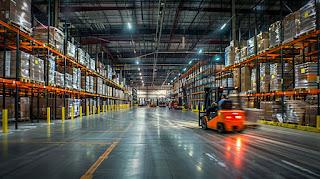
Forklift operators are key players in keeping warehouses and construction sites running smoothly. They handle the crucial task of moving goods, improving efficiency and contributing to the stocking process.
With skills in driving forklifts safely, they ensure materials reach their designated spots without any hitches. Their job involves not just driving but also packing and labeling items for shipment, showcasing their understanding of proper stock packaging methods.
Maintaining equipment is another important part of their role. Operators must inspect forklifts before use to keep them in good working condition, adhering strictly to safety rules set by both government and corporate standards.
This responsibility reduces risks and prevents accidents on site, making sure operations proceed without delay or harm. Next up: essential skills a forklift operator must have.
Essential Forklift Operator Skills
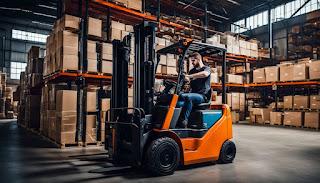
Mastering the skills of attention to detail, coordination, time management, communication, and problem-solving are essential for every forklift operator. These abilities contribute to safe and efficient operations in various working conditions.
Attention to Detail
Paying close attention to every detail is key for a forklift operator. This skill means always being alert about the load, where the forklift is, and what dangers might be around. Forklift operators have to check their machines often to make sure they work right.
This prevents accidents and keeps goods or buildings from getting damaged.
Being careful helps keep everyone in the warehouse safe and makes things run smoothly. Operators must follow all rules and safety steps without fail. Their sharp eyes help avoid problems before they happen, keeping work flowing without stops or troubles.
Coordination
Coordination is crucial for forklift operators. They must move through tight spaces and around obstacles smoothly. Good hand-eye coordination helps them control the vehicle safely.
This skill keeps work flowing without accidents or injuries.
Operators also need to coordinate with teammates in busy warehouses or industrial areas. By talking clearly, they make sure everyone knows where the forklift is going. This teamwork prevents crashes and boosts safety on the job site.
Time Management
Time management is a key skill for any forklift operator. It helps them prioritize tasks and work more efficiently throughout the day. Good time management means planning out the day so that there’s less downtime and higher productivity.
Forklift operators need to balance various tasks, from moving pallets to ensuring their areas are safe. They must keep an eye on how fast they complete their duties while maintaining safety standards.
Efficiently managing time also reduces the risk of accidents in the warehouse by allowing operators to focus on one task at a time without rushing. This careful planning leads to fewer errors and smoother operations overall.
As they master this skill, forklift operators contribute significantly to the effectiveness of warehouse activities, making sure everything runs on schedule. Next, we look at another critical component: communication skills.
Communication
Effective communication is vital for forklift operators, contributing to workplace safety and productivity. Clear and concise communication among team members is crucial when operating heavy machinery like forklifts to prevent accidents and ensure efficient material handling.
Adhering to safety protocols is closely linked to effective communication, making it an essential skill for forklift operators to master in their day-to-day operations.
Problem-solving
A forklift operator needs to quickly and effectively solve any issues that arise during work. This skill is crucial for maneuvering around tight spaces and obstacles in the warehouse.
Effective problem-solving contributes to smooth operation and resolving mechanical issues with the machinery, making continuous training necessary.
Forklift operators need to swiftly address any challenges that emerge while working, contributing to seamless operations in the warehouse setting. They are also responsible for troubleshooting and resolving mechanical issues with the machinery, highlighting how essential problem-solving skills are.
Forklift Operation and Safety Procedures
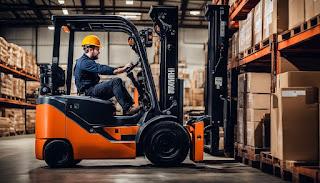
Operate the forklift safely by following proper safety procedures and guidelines. Regularly inspect and maintain the forklift, including load handling and stacking techniques.
Operating the forklift safely
To ensure safety, always conduct pre-operation checks on the forklift, including inspecting tires and ensuring proper tire pressure. Regularly maintaining the forklift by checking brakes, lights, steering, and keeping it clean is crucial.
Adhering to OSHA guidelines is essential.
Spot potential hazards in the operating environment and avoid them. Wear seat belts while operating the forklift to prevent accidents or injuries. Operate at a safe speed, taking into account load weight and height.
Always be mindful of surrounding vehicles and pedestrians.
Inspection and maintenance
Ensuring the forklift is in optimal condition is crucial for safe operation. Regular inspections need to be carried out to identify any potential issues before they become problematic.
This includes checking for leaks, maintaining proper tire inflation, and verifying that all safety features are functioning as intended. Proper maintenance helps prevent breakdowns and accidents, making it essential to conduct routine servicing of the forklifts in accordance with manufacturer guidelines.
Moreover, operators should have a keen eye for identifying potential hazards and addressing them through proper maintenance procedures.
Regular inspection and maintenance are pivotal aspects of ensuring safe and efficient forklift operations. Operators must conduct thorough pre-operation inspections, including checks for leaks, tire inflation, and functionality of safety features.
Load handling and stacking
Forklift operators must understand weight capacities, load distribution, and stacking heights to maintain stability. Efficient load handling and stacking techniques are crucial to prevent accidents, damage to goods, and injuries.
Proper skills in these areas ensure smooth operations while working with heavy loads and stacked materials. It’s essential for operators to be meticulous about the weight distribution and stacking arrangement to prevent tipping or unstable conditions that might lead to potential hazards.
Operators need a clear understanding of the specific requirements for each load as well as how it affects the balance of the forklift. This knowledge underpins safe and efficient load handling and stacking processes.
Importance of Hazard Awareness and Accident Prevention
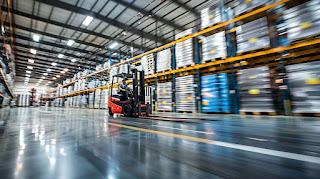
Forklift operators must vigilantly identify and anticipate potential hazards in the workplace. Being aware of weight limits and surrounding dangers is crucial to preventing accidents.
Effective hazard awareness ensures the safety of both the operator and other personnel, creating a secure work environment. Communication skills are essential for alerting others about potential risks, while teamwork enhances accident prevention measures.
Stress management training is vital for remaining calm during operations, further reinforcing accident prevention efforts.
The Role of Communication and Teamwork in Forklift Operations
Effective communication and teamwork are crucial for forklift operators to enhance efficiency in a warehouse or construction environment. Clear and active listening skills help in coordinating movements, ensuring smooth operations while preventing accidents.
Additionally, working as a team enables operators to communicate effectively about inventory control and safety compliance, contributing to improved productivity and a safer work atmosphere.
Encouraging effective communication among operators also aids in problem-solving, thereby improving overall workflow.
Moving on from the essential role of communication and teamwork in forklift operations emphasizes the significance of hazard awareness and accident prevention measures within this setting.
Conclusion
Mastering the essential skills for operating a forklift is crucial in improving efficiency and safety in warehouse and construction settings. Attention to detail, coordination, time management, communication, and problem-solving are key competencies that every forklift operator should possess.
These skills enable operators to handle machinery safely, maintain equipment effectively, prevent accidents, and contribute positively to inventory control. Forklift operators play a vital role in materials handling operations by ensuring the seamless transport of goods while upholding strict safety standards.
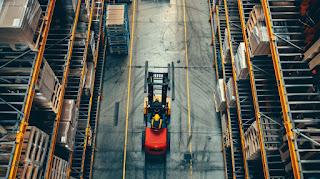
Many people worry that robots might take their jobs. Automation is changing how forklifts work in big ways. Our article shows you how to keep your job and thrive with new tech. Keep reading to learn more!
Key Takeaways
- Automation brings big changes to forklift jobs, needing workers to learn new skills like robotics and software use.
- Specialized training programs help forklift operators adapt to automated environments, including certifications from OSHA and ANSI.
- Future jobs in the forklift industry include roles as automation specialists, fleet managers, or data analysts due to the rise of automation.
Understanding Automation in the Forklift Industry
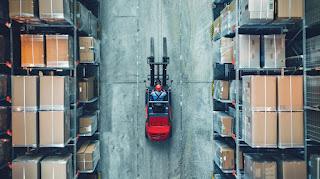
The shift from traditional forklift operations to automation marks a significant evolution in the industry. Automation includes both semi-autonomous and fully autonomous forklifts, which bring major improvements to efficiency, safety, and cost savings.
These technological advancements incorporate artificial intelligence (AI), machine learning, and the Internet of Things (IoT) to create smarter warehousing solutions. Automated guided vehicles (AGVs) and cobots work alongside human operators, streamlining tasks like lifting, moving, and placing goods with precision.
This transformation is driven by the need for speedier logistics and safer working environments. Forklift manufacturers are continuously innovating, integrating systems like stability control, computer vision, and telematics into material-handling equipment.
Such innovations ensure automated forklifts can navigate very narrow aisles in warehouses without human intervention. The result is not just increased productivity but also reduced accidents within distribution centers—a win-win scenario for businesses aiming to stay competitive in a fast-paced market.
The Impact of Automation on Forklift Jobs
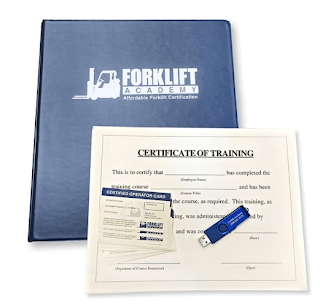
The current state of forklift jobs is evolving due to automation, presenting new job opportunities amidst technological advancements. Future forklift operators in an automated environment require essential skills to adapt and thrive.
The current state of forklift jobs
Forklift jobs are changing fast because of automation and new technology. Many forklift operators now need to know how to work with automated systems as much as they operate the trucks themselves.
This shift means that while some traditional driving roles decrease, other opportunities open up. These new roles often involve overseeing automated forklifts, managing software that controls them, or maintaining the advanced equipment.
Operators must stay current by learning about robotics, artificial intelligence, and software used in modern warehouses. Training programs and certifications for working with these innovations are more important than ever.
Skills in problem-solving, technical understanding, and adaptability have become key to thriving in this evolving field. As automation grows, so does the need for workers who can manage and maintain these complex systems effectively.
Job opportunities amidst automation
Automation in the forklift industry creates new job roles. People can now work as automation specialists, fleet managers, or data analysts. These jobs need skills in handling automated systems and understanding data-driven decision-making processes.
Training programs are available to help workers learn about automated forklifts and technological advances. These courses prepare them for modern challenges in material handling and logistics.
Essential Skills for Future Forklift Operators in an Automated Environment
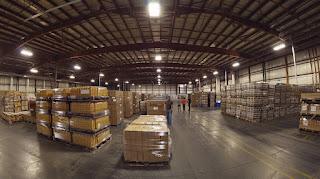
Forklift operators entering an automated environment must sharpen their technical skills. They must learn to work with advanced systems like autonomous mobile robots, onboard diagnostics, and automated forklifts.
Mastery of these technologies ensures smooth operation and maintenance of modern machinery. Operators should be comfortable using computers, whether a desktop or a laptop, as they will often monitor equipment via online training platforms or warehouse management systems.
Problem-solving and adaptability are also crucial in this new landscape. Forklift professionals will face unexpected challenges ranging from troubleshooting automation issues to adapting workflows around new technology integrations.
These soft skills complement the technical proficiency required, allowing operators to make quick decisions that keep operations running smoothly. Cultivating a mindset geared toward innovation helps future forklift operators thrive amidst the rapidly changing demands of materials handling and supply chain industries.
The Role of Training in Adapting to Automation
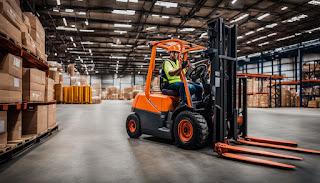
Training is crucial for adapting to automation in the forklift industry. To understand how this impacts you, read more!
Training and certifications for the modern forklift operator
Forklift operators need specialized training and certifications to adapt to automated systems. Here are essential training and certification programs for modern forklift operators:
- OSHA forklift operator certification: Ensures operators have the necessary skills and knowledge to operate forklifts safely, meeting OSHA guidelines.
- ANSI forklift operator certification: Recognized by the industry, this certification ensures operators are proficient in handling modern forklift equipment.
- Automated forklift certification: Tailored towards mastering the complexities of operating automated forklifts, including programming and interfacing with autonomous systems.
- Specialized training programs: Offered by Forklift Academy, these programs cover topics such as collision avoidance systems, light detection and ranging (LIDAR), and machine-to-machine communication in an ever-evolving realm of automation.
- Online forklift certification: Designed to enhance the skills of forklift operators through robust online modules covering topics like fleet management, ergonomic design, and electric-powered lift trucks.
- Individualized training courses: Tailored towards specific job roles in material handling equipment, focusing on collaboration with autonomous systems and sustainability in the world of warehouse operations.
- Forklift Certification near me: Providing hands-on training in sustainable energy efficiency practices, big data analytics for inventory management, and telemetry-equipped lift trucks.
- Industry-recognized certifications: Including Toyota Material Handling’s bespoke automated forklift certification program that dives into the complexities of self-driving lift trucks and their towing capacity within a logistical setting.
The Role of Employers in Embracing Automation
Employers must invest in specialized training programs to help forklift operators adapt to automation. They should also offer flexible work arrangements and communicate openly with their workforce.
Industry-recognized certifications like OSHA forklift operator certification are essential, and employers need to support their workforce in acquiring the necessary skills for the evolving landscape of automated forklifts.
The Future of Forklift Jobs and Automation
The future of forklift jobs is changing with automation. Read more about this evolving industry.
Preparing for the future: A guide for forklift professionals
- Stay informed about industry trends and advancements in automation technology to remain competitive in the evolving forklift industry.
- Seek out specialized training programs designed to enhance your skills in managing and maintaining automated systems, ensuring you stay relevant in the ever-evolving field of forklift operations.
- Embrace change proactively by honing new skills and adopting best practices that align with the demand for automated forklift operations.
- Explore opportunities to transition into specialized roles such as automation specialists, fleet managers, and data analysts, leveraging the wealth of job opportunities presented by automation in the forklift industry.
- Engage in ongoing education to strengthen your expertise and capabilities, equipping yourself with the knowledge required to thrive in a realm underpinned by IoT and automation.
- Proactively seek flexible work arrangements, and continuing remote work options that unlock the secrets to a balanced work-life dynamic while navigating the complexities of an ever-changing industry.
- Advocate for employer investment in training and education initiatives, creating a responsive workforce prepared to tackle the challenges posed by automated technologies within the realm of forklift operations.
- Communicate openly and transparently with employers regarding your commitment to adapting to automation, demonstrating your dedication towards embracing new technologies shaping the future of forklift jobs.
Conclusion: Navigating the Future of Forklift Jobs with Confidence
Prepare for the future by embracing automation and developing new skills. Stay informed about industry trends, seek out training opportunities, and adapt proactively to change. Employers should invest in training, offer flexible work arrangements, and communicate openly with their workforce.
The impact of automation on forklift training presents new opportunities for those willing to embrace change and stay relevant in the industry.
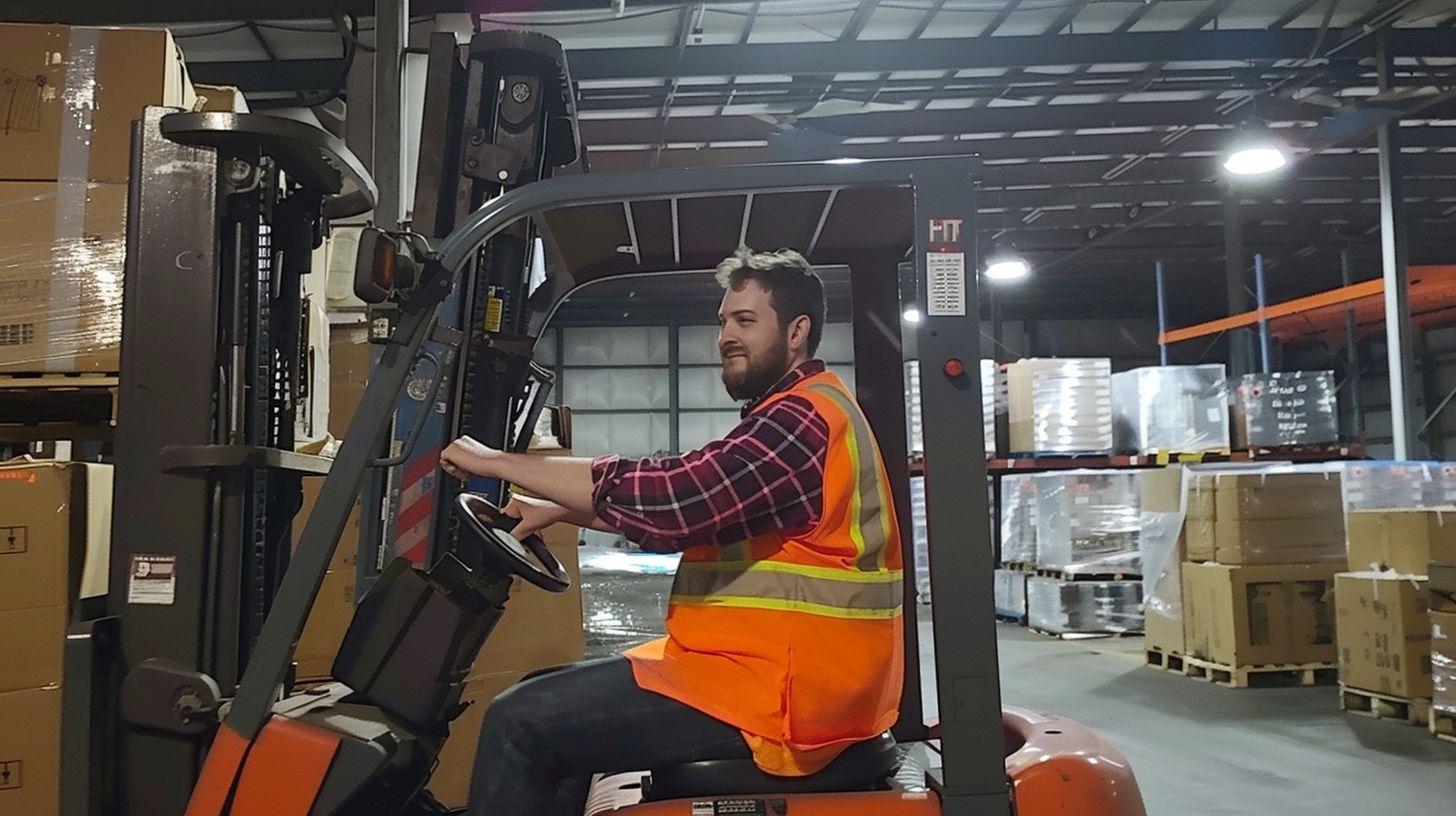
Are you wondering if getting forklift certified is worth it? On average, forklift operators make between $33,000 to $43,000 a year. This article will show you why earning your forklift certification can open up more job opportunities and ensure workplace safety. Read on to find out how simple steps can lead to big changes in your career.
What is Forklift Certification?

Forklift certification is a special permit that lift truck drivers must have. It shows they know how to operate forklifts safely and properly. The Occupational Safety and Health Administration, or OSHA, requires all operators of these heavy machines to get certified.
This rule helps keep working conditions safe and reduces the risk of work-related injuries in places like warehouses and construction sites.
Getting this certification involves passing an exam that covers important safety training topics. This process ensures drivers understand how to handle forklifts without putting themselves or others at risk.
Once certified, operators can legally drive forklifts in the United States and beyond, making it essential for employment in various industries where moving goods is a daily task.
Key Benefits of Forklift Certification
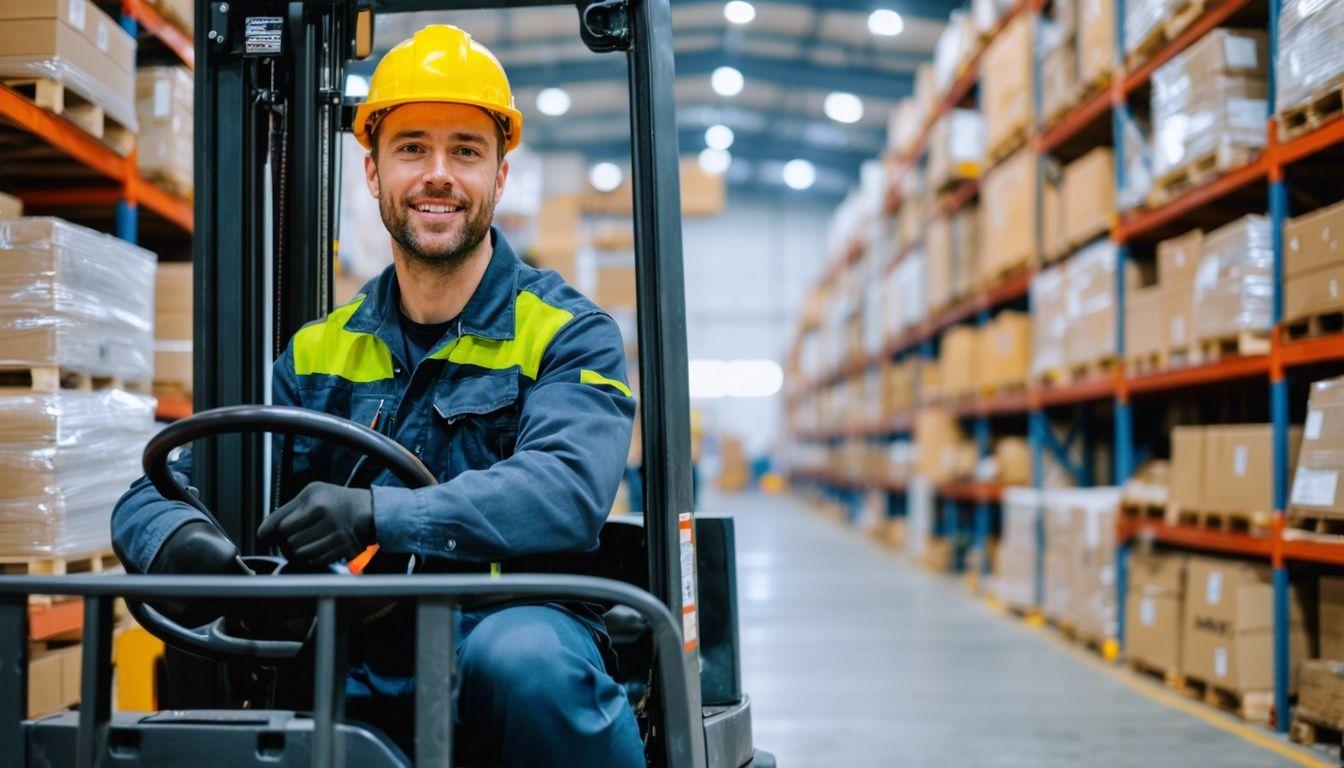
Forklift certification enhances workplace safety, reduces the risk of injuries, and ensures legal compliance. Certified forklift operators also have access to more job opportunities and potential for higher earnings.
Legal Compliance
Obeying the law is crucial for forklift drivers. The Occupational Safety and Health Administration (OSHA) sets these rules to ensure everyone’s safety at work. By getting certified, you show that you know how to operate heavy equipment like a forklift safely.
This certification isn’t just important; it’s required by law. Every operator must renew their proof of expertise every three years to stay legal.
This requirement protects employees from workplace injuries and reduces employers’ risk of facing hefty fines from OSHA violations. In fact, obeying these laws keeps insurance premiums lower for companies and safeguards workers’ compensation rights for employees.
Following these standards proves your commitment to maintaining a safe working environment.
Stay ahead in your career by meeting legal standards today.
Next, we’ll examine how this commitment impacts job safety on the warehouse floor.
Enhanced Job Safety
Getting forklift certified boosts job safety massively. This certification guarantees that operators know how to handle these large machines safely, protecting themselves and their coworkers from potential harm.
With the right training, certified drivers become experts in maneuvering around tight spaces, stacking goods high up without accidents, and maintaining a hazard-free workspace. Companies emphasize this by setting high standards for workplace safety and safety engagement.
Certification programs focus on practical training that is critical for avoiding workplace injuries. Operators learn the importance of pre-operation checks to ensure trucks are in good working order before starting shifts.
They also grasp essential safety precautions like proper lifting techniques and speed regulation to prevent tipping over. In effect, having trained personnel both meets legal compliance and leads to cost savings by reducing the money companies might otherwise spend on insurance claims or damages from accidents caused by untrained staff.
More Job Opportunities
Getting your forklift certification opens doors to more job opportunities in various industries. Companies always look for certified operators because they meet safety and standardization requirements set by insurance companies.
This certification boosts your resume and shows employers that you take job safety seriously. With this qualification, you can choose from a wide range of jobs, like working in warehouses, manufacturing plants, or construction sites.
It makes you stand out in the job market and often leads to quicker hiring.
Certified forklift operators enjoy better job security since their skills are in high demand across different sectors. They can pick where they want to work, thanks to the versatility of their certification.
From temp worker positions to full-time roles, there’s a variety of options available that cater to individual needs and preferences. Your LinkedIn profile gains more visibility among recruiters who constantly seek skilled staff for immediate openings.
Earning potential increases with forklift certification is next on our list.
Higher Earning Potential
With more job opportunities available, getting forklift certified also opens the door to earning a higher salary. Forklift operators make between $33,000 and $43,000 annually. Those with certification from an OSHA-approved course usually earn at the higher end of that scale.
This makes sense because employers value the safety and efficiency that come with proper training. They’re willing to pay more for workers who bring these qualities to their operations.
Certification doesn’t just bump up salaries; it often leads to promotions within companies. A certified operator has proven their skill level through both knowledge evaluation and practical exams, making them prime candidates for advancing their careers.
This career advancement directly impacts one’s earning potential over time.
Investing in online forklift certification can significantly boost your salary and career prospects.
Requirements for Forklift Certification
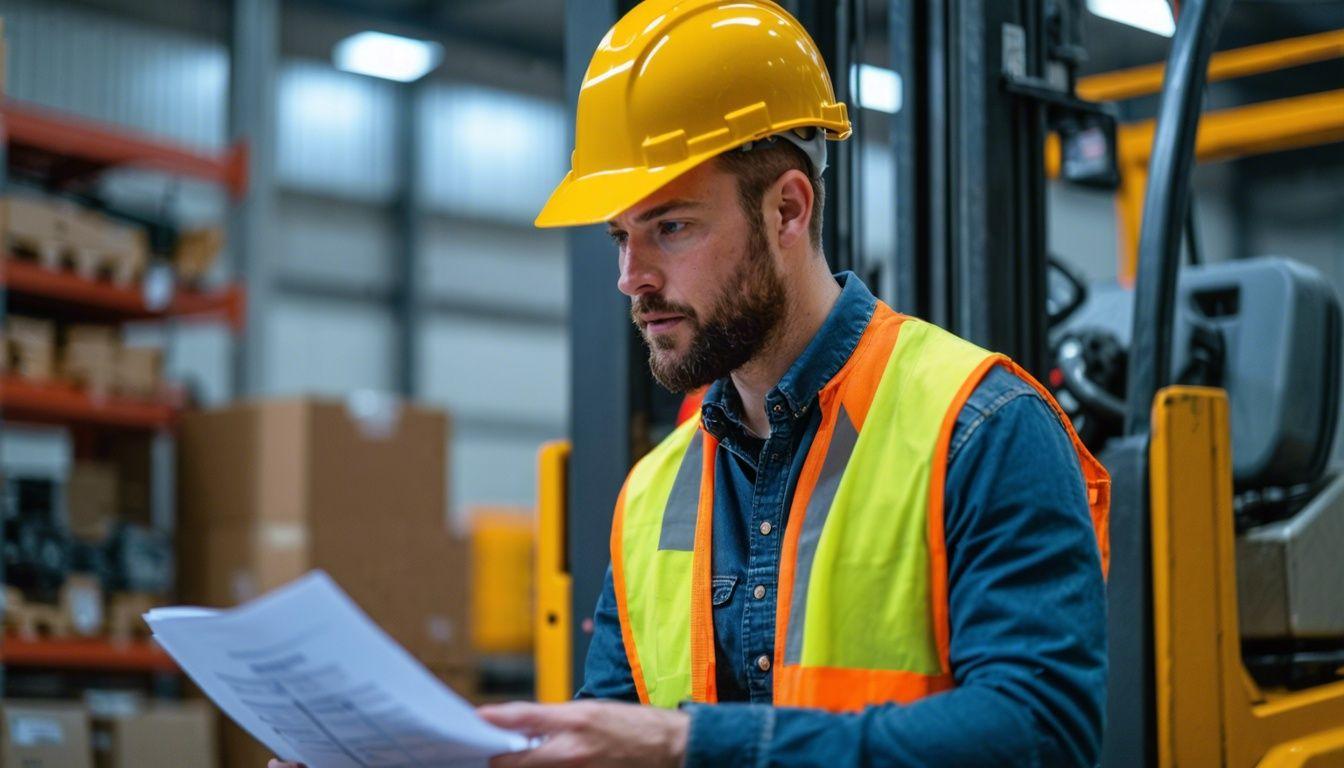
To obtain forklift certification, individuals must complete specific training requirements in accordance with OSHA standards. This entails undergoing an accredited course and passing a certification exam.
Training Requirements
To get forklift certified, you need to complete specific training that teaches you how to operate a forklift safely and efficiently. This training includes both in-person classes and online courses.
The in-person portion covers hands-on experience with the equipment, which is crucial for mastering the skills needed for safe operation. These programs usually take 1 to 2 days to finish, depending on the course’s intensity and schedule.
During these training sessions, instructors provide formal instruction covering all aspects of forklifting, from driving basics to more advanced techniques. You also go through practical exercises designed to mimic real-life scenarios you might encounter while working.
Once done with this stage of your certification journey, an employer must evaluate your performance and confirm your ability before you’re officially recognized as a certified operator.
OSHA Standards
After covering the pivotal training requirements for forklift certification, we move to a critical component of this process: OSHA standards. The Occupational Safety and Health Administration (OSHA) outlines clear mandates stating that all forklift operators must have certification.
This rule ensures every operator knows how to handle these powerful vehicles safely, protecting themselves and their coworkers from potential hazards.
OSHA’s guidelines serve as the backbone for safety protocols across various industries. They decree that certifications need renewal every three years. By adhering to these standards, companies align with legal obligations while fostering a safer work environment.
This compliance minimizes accidents and also shields businesses from costly penalties and insurance claims.
Certified operators ensure personal and co-worker safety, legal compliance, and cost savings.
How to Get Forklift Certified
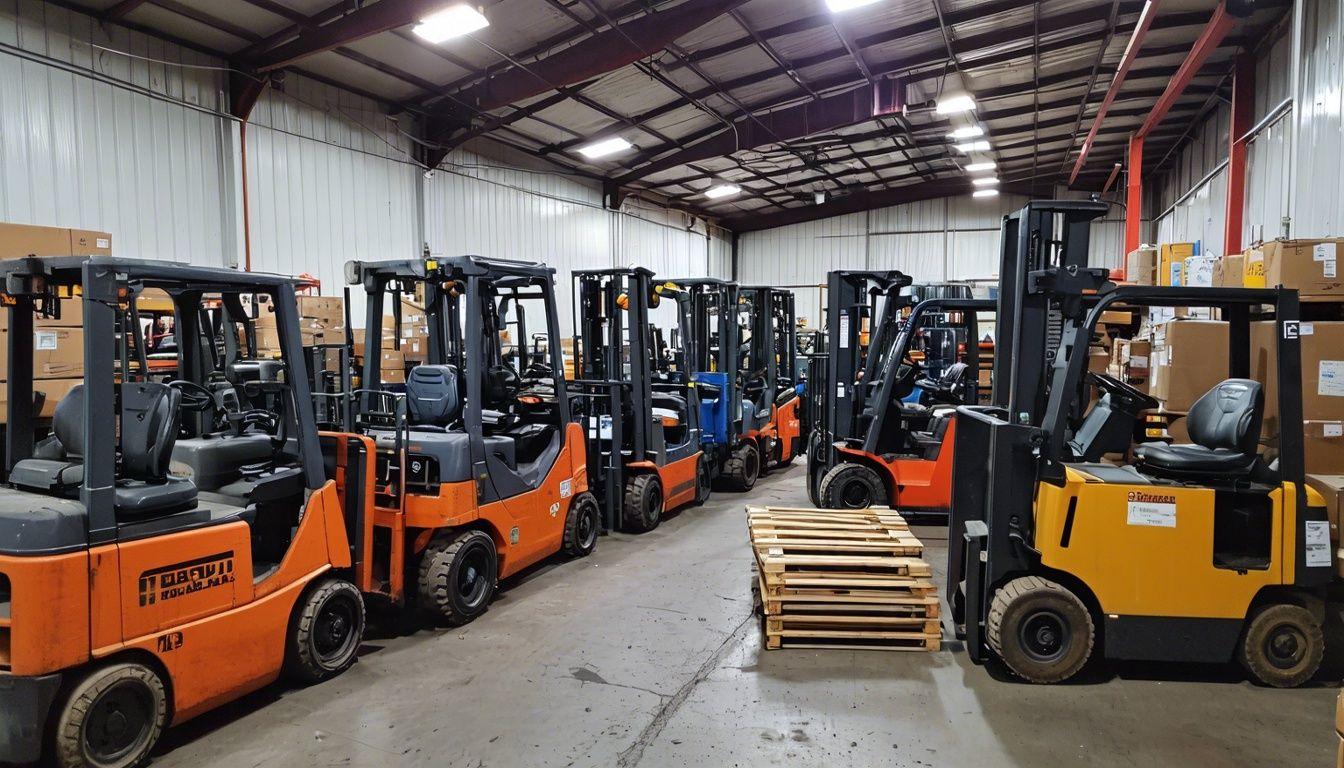
To obtain forklift certification, you can enroll in an accredited course and meet the experience requirements. Following this, you will need to pass the certification exam.
Enroll in an Accredited Course
Choosing the right course for your forklift certification is key. Look for accredited programs offered by respected institutions like Forklift Academy.
These organizations provide training that meets all legal standards and prepares you for a safer job environment. Their courses often come in two formats: in-person and online.
Deciding between an online program and an in-person class depends on your schedule and budget. Online training can cost between $40-$60, making it a budget-friendly option that you can complete at your own pace.
On the other hand, in-person training costs more, typically ranging from $150-$200 but offers hands-on experience under the guidance of an expert instructor. Both types of training will equip you with the necessary skills to operate a forklift safely and efficiently while adhering to insurance company requirements and staffing standardizations.
Meet the Experience Requirements
After signing up for an accredited course, the next big step is to gain some real-world experience. You need to be at least 18 years old and have handled a forklift before. This hands-on practice is critical because it prepares you for the practical part of your certification exam.
It also ensures you’re familiar with the basic functions and safety protocols of operating these heavy machines.
Gaining this experience means spending time on the job under supervision, learning how to work in different warehouse scenarios, and understanding how to maintain these vehicles to avoid breakdowns and costly repairs.
Each hour spent behind the controls makes you a safer, more competent driver. This meets OSHA standards and sets you up for success in your career as a certified operator.
Pass the Certification Exam
To become forklift certified, you will need to pass the certification exam with a minimum score of 75% to 80%. The test format usually consists of multiple-choice questions or a combination of multiple-choice and written answers.
If you do not achieve the passing score on your first attempt, you will be required to retake the exam. Once successfully passed, your certification card should include your name and training date as proof of completion.
Forklift Academy: Your Partner in Certification
Forklift Academy is a leading provider of OSHA-compliant forklift certification programs. With over 20 years of experience, they offer both online and in-person training options designed to fit various schedules and budgets.
Their courses cover all necessary safety and operational protocols, ensuring that participants are well-prepared to handle forklifts efficiently and safely. Forklift Academy’s commitment to excellence is reflected in their comprehensive training modules, experienced instructors, and supportive learning environment. By choosing Forklift Academy, individuals and businesses can ensure compliance with industry standards and enhance workplace safety.
The Importance of Renewing Your Forklift Certification
Renewing your forklift certification is crucial due to legal requirements and safety concerns. The certification expires after three years, necessitating re-evaluation and possibly additional training.
This process reinforces your knowledge, ensuring that you remain up to date with the latest safety protocols and operational best practices. Moreover, it demonstrates your commitment to maintaining a safe work environment.
Continuing education in forklift operation not only fulfills legal obligations but also enhances workplace safety, reducing the risk of accidents and associated costs. It also opens doors to continued career growth by delivering ongoing value to employers through enhanced skills and compliance with industry standards.
Conclusion
Becoming forklift certified is a significant achievement. It opens up new job opportunities, ensures legal compliance, and enhances workplace safety. Employers prefer certified operators for a safe and accident-free work environment.
Forklift certification offers higher earning potential and paves the way for career advancement. Getting certified not only boosts your marketability but also demonstrates your commitment to safety and professionalism in the workplace.
FAQs
1. Why is being forklift certified important?
Being forklift certified shows that you know how to safely operate a forklift, much like having a driver’s license proves you can safely drive a car.
2. Can anyone get forklift certified?
Yes, if you are the right age and complete the required training and tests, you can get your certification to operate a forklift.
3. Does having a forklift certification help with getting a job?
Absolutely! Many employers look for workers who are already certified to operate forklifts because it saves them time and resources on training.
4. How long does it take to become certified in operating a forklift?
The time it takes can vary, but most courses last from one day to one week. After completing your training, you’ll take a test to earn your certification.
5. Do forklift certifications expire?
Yes, forklift certifications need to be renewed every three years to ensure that operators stay up-to-date with the latest safety practices and regulations. This helps maintain a high standard of safety and efficiency in the workplace.
6. What types of jobs can I get with a forklift certification?
With a forklift certification, you can work in various industries such as warehouses, construction sites, manufacturing plants, and distribution centers. These roles often offer good job stability and opportunities for career growth.
7. Is the forklift certification exam difficult?
The difficulty of the exam can vary, but it typically covers the essential safety and operational procedures that you learned during your training. Proper preparation can help you pass, and many find the practical component particularly helpful for understanding real-world applications.