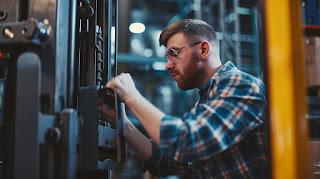
Keeping your forklift running smoothly can be a challenge. Planned maintenance is crucial, helping to avoid costly downtime and repairs. This guide will give you the tools and knowledge you need to keep your lift trucks in top shape, ensuring safety and efficiency on the job.
Dive in to discover maintenance made easy!
Key Takeaways
- Regular forklift maintenance enhances safety by preventing accidents and ensuring safety features are working properly. It also keeps the machine running smoothly, leading to increased productivity.
- Adhering to OSHA’s daily examination requirements and using their checklists can help identify maintenance issues early on, keeping the workplace safe and compliant with regulations.
- Preventive maintenance plans should include daily checks as well as non – driving and driving inspections, focusing on aspects like fluid levels, brakes, tires, batteries, and lights.
- Professional forklift maintenance services offer quality assurance and use of the right parts. They help preserve warranties while saving time that would be lost during equipment downtime.
- Performing DIY tasks such as replacing filters, checking fluid levels, inspecting batteries, monitoring tire condition can contribute significantly to a forklift’s longevity while reducing repair costs.
Importance of Forklift Maintenance
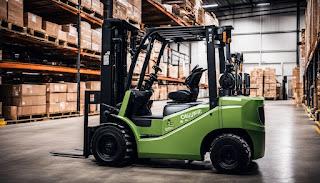
Forklift maintenance is crucial for enhancing safety, increasing productivity, and extending the service life of the equipment. It also helps in reducing costs associated with repairs and downtime.
Enhances Safety
Regular maintenance of forklifts is a key factor in preventing accidents and ensuring the safety of operators and other employees. By performing routine checks, potential hazards like leaks or brake issues can be identified and addressed before becoming dangerous.
Ensuring that seatbelts, warning lights, and other safety features are functioning properly also contributes to a safer environment.
Safety precautions go hand in hand with maintaining equipment reliability. Well-maintained forklifts operate more predictably, reducing the chances of unexpected malfunctions that could lead to injuries or property damage.
Moreover, adherence to OSHA’s stringent safety regulations through methodical forklift maintenance keeps workplaces compliant and workers protected from preventable mishaps.
Increases Productivity
Keeping your forklift well-maintained means it’s always ready to tackle the job at hand. Sudden breakdowns and prolonged downtime become rare, letting operators work efficiently without unexpected stops.
This steady stream of performance boosts a company’s output significantly. Equipment that receive routine maintenance run smoother and are less likely to suffer from the wear and tear that slows down operations.
Scheduling professional forklift maintenance services leads to quality repairs that also preserve important warranties. These experts handle issues before they escalate, which saves time by avoiding long repair sessions.
With everything in top condition, forklifts move materials quickly and safely through warehouses, allowing businesses to meet deadlines with ease and stay ahead in fast-paced markets.
Extends Service Life
Regular maintenance not only keeps forklifts running smoothly but also significantly extends their service life. Following the manufacturer’s recommended schedule ensures that each component gets the attention it needs before minor issues grow into major problems.
Preventative maintenance, such as checking fluid levels, inspecting tires and brakes, and changing the oil, helps avoid the wear and tear that can shorten a forklift’s lifespan. By taking care of these small tasks regularly, you can keep your forklift truck operational for years beyond what might be expected with less diligent care.
A well-maintained forklift does not suffer from frequent breakdowns that often indicate a machine is nearing the end of its useful life. Investing in consistent upkeep means internal components like valves, pumps, and bushings stay in working order longer.
This leads to reduced downtime due to repairs and ensures the vehicle remains reliable throughout its extended life cycle. With every completed checklist task or lubricant change—be it hydraulic oil or engine coolant—the potential service period of your heavy machinery increases, giving you more value from your investment over time.
Lower Costs
Keeping forklifts in top shape through preventive maintenance can slash your expenses significantly. It curbs the need for frequent repairs and reduces the risk of costly downtimes.
Well-maintained machines mean less money spent on replacing parts that wear out prematurely or fixing major issues that could have been avoided. This attention to routine care pays off by preserving the lifespan of your investment, ensuring you get the most value from every dollar.
Conducting proper operations also protects your bottom line. Training operators to handle forklifts with care, avoid overloading, and navigate ramps cautiously minimizes damage to equipment.
Less strain on components like engines and batteries leads to reduced fuel consumption or battery-charging costs over time, as well as fewer tire replacements due to decreased wear from heavy loads or improper maneuvering.
Smart handling coupled with diligent maintenance translates into significant savings and a healthier business valuation.
OSHA Requirements for Forklift Maintenance
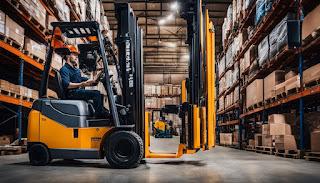
OSHA mandates daily examinations for industrial trucks to ensure immediate correction of any defects or unsafe conditions. Additionally, OSHA’s planned maintenance checklists can be utilized for training forklift operators and identifying essential maintenance issues.
Different planned maintenance checklists are designed for different types of forklifts, such as internal combustion engine or electric forklifts. Adhering to these requirements ensures compliance with OSHA regulations and helps in maintaining a safe working environment.
Thorough and regular inspections help identify patterns of wear, mitigate potential hazards over time, and ensure adherence to the set guidelines.
Maintaining comprehensive records assists in tracking the equipment’s condition over time while also ensuring compliance with OSHA requirements. These practices not only promote workplace safety but also contribute to avoiding unnecessary risks related to machinery operation and maintenance.
Creating a Preventive Maintenance Plan
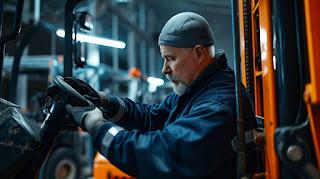
Developing a preventive maintenance plan for your forklift is essential to ensure that it remains in optimal condition. This includes daily, non-driving, driving, and forklift-specific checklists to catch potential issues before they become major problems.
Daily Maintenance Checklists
- Conduct a visual inspection of the forklift for any leaks, damages, or signs of wear and tear.
- Check the fluid levels, including engine oil, hydraulic fluid, coolant, and brake fluid, and top them up if necessary.
- Inspect the tires for any damage, wear, or proper inflation levels according to the manufacturer’s recommendations.
- Test all safety features such as lights, alarms, horns, and seatbelts to ensure they are functioning correctly.
- Examine the battery for corrosion and ensure it is securely connected with no visible damage to the cables.
- Test the brakes by engaging them in a safe environment to ensure they are responsive and not making unusual noises.
- Clean the forklift both inside and out to maintain proper hygiene and prevent debris from affecting its performance.
Non-Driving Maintenance Checklists
Perform these maintenance checks regularly to ensure the proper functioning of your forklift:
- Inspect the brakes for wear and tear, including brake pads and hydraulic systems. Replace any worn – out components promptly to maintain braking efficiency.
- Check the hydraulics for leaks or damage, assessing the condition of hoses, seals, and cylinders. Address any issues immediately to prevent potential breakdowns.
- Examine the lift chains or forks for signs of wear, such as stretching or cracks. Ensure they are properly lubricated and free from any obstructions that could affect their performance.
- Test the lights, horn, and other safety features to ensure they are functioning correctly. Replace any faulty bulbs or repair damaged wiring to maintain visibility and compliance with safety regulations.
- Monitor the overall condition of the forklift’s body, ensuring there are no dents, cracks, or other structural damage that could compromise its stability and safety during operations.
- Verify the functionality of the cooling system by checking coolant levels and inspecting for any leaks or blockages in the radiator, hoses, and connections.
Forklift-Specific Maintenance Checklists
Forklift-specific maintenance checklists are crucial for ensuring the proper upkeep of different types of forklifts, as each type has unique maintenance requirements.
- Electric Forklifts:
- Regularly inspect and maintain the battery, including checking water levels and cleaning terminals to ensure optimal performance and longevity.
- Conduct thorough checks on the electrical system, including wiring, connections, and controls to prevent malfunctions and ensure safe operation.
- Diesel Forklifts:
- Regularly inspect the engine components such as air filters, fuel filters, and oil levels to maintain efficient performance and prevent breakdowns.
- Ensure proper maintenance of the exhaust system to minimize emissions and comply with environmental regulations.
- Propane Forklifts:
- Verify the condition of fuel lines, connectors, and tanks regularly to prevent leaks or malfunctions that could pose safety hazards.
- Inspect the cooling system, including coolant levels and radiator condition, to avoid overheating issues that can affect performance.
- Pneumatic Tire Forklifts:
- Check pneumatic tires regularly for wear, damage, or low pressure to maintain stability and traction.
- Inspect the hydraulic system for leaks or malfunctions to ensure smooth lifting operations without safety risks.
- Warehouse-Use Forklifts:
- Inspect load handling attachments such as forks and clamps for wear or damage that could compromise load stability or operator safety.
- Regularly check mast components for proper lubrication and alignment to ensure smooth vertical movement when handling loads.
- Rough Terrain Forklifts:
- Periodically inspect the undercarriage components, including axles, drive train, and suspension systems for signs of wear or damage due to rugged operating conditions.
- Ensure regular inspection of additional safety features specific to rough terrain forklifts such as roll-over protection structures (ROPS) for compliance.
Driving Maintenance Checklists
To ensure the proper upkeep of forklifts, regular driving maintenance checklists are essential. Regular checks help in identifying and addressing potential issues before they escalate. Here is a comprehensive list of driving maintenance tasks:
- Inspect the tires for wear and tear, ensuring proper inflation levels to maintain stability and maneuverability.
- Check the brakes to ensure they are functioning effectively, reducing the risk of accidents and damage to goods.
- Examine the steering system to guarantee smooth operation and precise control during usage.
- Test the accelerator and engine – off functions to ensure efficient performance while minimizing fuel consumption.
- Verify that all lights, including headlights, taillights, and indicators, are operational for enhanced safety in dimly lit areas.
- Assess the fluid levels, such as oil, hydraulic fluid, and coolant, to prevent mechanical issues and overheating.
Common Forklift Maintenance Repairs
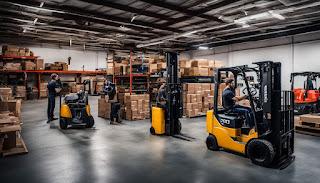
From mast problems to steering and starting issues, forklifts can face a range of common maintenance repairs that need attention. Want to know more about how to tackle these issues? Keep reading for the ultimate guide to forklift maintenance.
Mast Problems
Mast problems affect a forklift’s lifting and lowering capabilities. These issues can lead to reduced productivity and increased downtime if not addressed promptly. It is crucial to regularly inspect the mast system as part of a comprehensive maintenance plan to ensure optimal performance and safety.
When mast problems arise, it is essential to take immediate action to prevent further damage or potential accidents. Regular inspection and timely repairs can help avoid costly disruptions in operations and maintain a safe working environment.
Steering Problems
Strange noises while turning and difficulty in steering may indicate potential steering problems with a forklift. These issues can be caused by worn-out pressure valves, gears, or misaligned tires.
If left unaddressed, steering problems can lead to safety hazards and decrease productivity.
By addressing steering problems promptly, you can ensure the safety of your operators and extend the service life of your forklifts. Regular maintenance checks should include inspecting the steering system for any signs of wear or misalignment to prevent more severe issues from developing.
Starting Problems
After addressing steering problems, it’s essential to consider starting problems for efficient forklift maintenance. To tackle starting issues, checking the battery charging level is crucial.
Regular monitoring and ensuring the appropriate charge are fundamental in preventing these common maintenance concerns. Moreover, prompt attention to any irregularities in battery power can significantly reduce downtime and improve overall productivity.
Starting problems on electric forklifts often stem from insufficient or improper battery charging. By actively managing this aspect of maintenance, operators can proactively address potential starting issues before they escalate into larger repair needs.
DIY Forklift Maintenance Tasks
Regular maintenance tasks for forklifts are vital to ensure their proper functioning and longevity. Here’s a list of DIY maintenance tasks that can help keep your forklift in top condition:
- Filter Replacements: Regularly replace air, fuel, and oil filters as part of your maintenance routine to ensure the engine runs smoothly and efficiently.
- Fluid Top-offs: Check and top off all necessary fluids, including engine oil, transmission fluid, coolant, and hydraulic fluid, to prevent potential damage.
- Quick Inspections: Conduct routine visual inspections of the forklift for any signs of wear and tear, leaks, or loose components that may affect its performance.
- Battery Checks: Inspect the battery terminals, electrolyte levels, and overall battery condition to ensure it is functioning optimally and avoid unexpected downtime.
- Tire Changes: Regularly monitor tire tread wear and replace tires when necessary to maintain traction and stability while operating the forklift.
- Tire Damage Monitoring: Keep an eye out for any punctures, cuts, or other damage to the tires that may compromise safety or performance on different surfaces.
Benefits of Professional Forklift Maintenance Services
Professional forklift maintenance services provide quality assurance and the use of the right parts, preserving the warranty and saving time for your business. Learn more about how these services can benefit your fleet management and overall productivity.
Quality Assurance
Quality assurance in forklift maintenance is crucial to ensure that the equipment operates safely and efficiently. Regular maintenance checks contribute to identifying potential issues early, minimizing the risk of unexpected breakdowns that may compromise safety and productivity.
By adhering to quality standards, such as OSHA requirements and manufacturer guidelines, businesses can uphold a safe working environment while maximizing the lifespan of their forklift fleet.
Thorough documentation of maintenance activities not only helps track compliance with regulatory standards but also provides valuable insights into long-term wear patterns and overall upkeep costs.
Right Parts
Using professional forklift maintenance services ensures that you get the right parts for repairs and replacements, which is crucial for keeping your equipment running smoothly. By using genuine parts, you can be confident in the quality and compatibility with your specific forklift model, reducing the risk of future issues.
Additionally, proper maintenance helps in preserving warranties on forklift parts, providing added financial protection and peace of mind. Planned maintenance allows scheduling servicing appointments using the right parts during convenient times for operations.
This proactive approach minimizes downtime while maximizing efficiency.
Warranty Preservation
Preserving the warranty of your forklift is crucial for avoiding unexpected repair costs. Professional maintenance services help ensure that any warranty claims are not compromised due to neglect or improper handling.
Regular upkeep and adherence to manufacturer’s recommendations can go a long way in safeguarding the warranty of your valuable equipment.
Using licensed technicians and genuine parts for repairs also contributes to upholding the warranty conditions. Additionally, keeping detailed records of all maintenance activities and adhering to OSHA requirements further support warranty preservation efforts.
Time Saving
Moving from warranty preservation to time-saving, it’s clear that efficient forklift maintenance not only safeguards your investment but also optimizes operational productivity. By strategically scheduling servicing appointments during non-peak hours, businesses can minimize downtime and save valuable time.
Adhering to a regular maintenance plan prevents emergency interruptions and unplanned expenses, ensuring consistent workflow without unnecessary delays.
Conclusion
In conclusion, regular forklift maintenance is crucial for workplace safety and productivity. This comprehensive guide highlights the importance of planned maintenance, OSHA requirements, creating a preventive maintenance plan, common repairs, DIY tasks, and the benefits of professional services.
By implementing these strategies, businesses can ensure smooth operations and maximize the lifespan of their fleet while minimizing costs in the long run.
FAQs
1. Why is forklift maintenance important?
Forklift maintenance is key to keeping these vehicles running safely and efficiently; it can help prevent accidents, reduce maintenance costs, and ensure compliance with the Occupational Safety and Health Administration (OSHA) standards.
2. What are some common forklift parts that need regular checks?
You should regularly check your forklift’s power steering, clutch, fuel economy aspects, internal-combustion engine components if applicable, and bearings as part of ongoing maintenance to avoid breakdowns.
3. How does proper maintenance affect a forklift’s return on investment (ROI)?
Maintaining your forklift will lower repair costs over time and keep it in operation longer without issues, which enhances the overall return on investments by prolonging the vehicle’s life span.
4. What safety gear do I need when performing forklift repairs?
Always use personal protective equipment (PPE), such as gloves and goggles when doing repairs or maintenance work to adhere to occupational health and safety guidelines.